How to Be Safety Hygienist - Job Description, Skills, and Interview Questions
Steps How to Become
- Obtain a Bachelors Degree. To become a safety and hygiene professional, you must first obtain a bachelors degree in a related field such as occupational health and safety, industrial hygiene, public health, or environmental health.
- Secure Relevant Work Experience. After completing a degree, employers may require applicants to have several years of relevant work experience in order to qualify for the position. This could include working in a safety and health role in an industrial setting or a public health agency.
- Consider Certification. Organizations such as the National Environmental Health Association (NEHA) and the Board of Certified Safety Professionals (BCSP) both offer certifications for safety and hygiene professionals. Certification can demonstrate your knowledge and expertise in the field and can help you stand out from other job applicants.
- Maintain Your Credentials. Once you have obtained your certification, it is important to maintain it by taking continuing education classes and staying up-to-date on the latest safety and hygiene regulations and best practices.
- Network. You can also increase your chances of finding work by networking with other safety and hygiene professionals through professional associations, conferences, and job fairs.
Staying ahead and efficient as a safety hygienist requires dedication and a commitment to staying organized. By developing and following a plan, a safety hygienist can ensure that all tasks are completed in a timely manner. Setting aside time each day to review and update safety plans, inspect facilities, and update records can help to stay on top of tasks.
taking the initiative to investigate potential hazards and communicating potential safety concerns to management can help to avoid potential disasters. Taking the time to stay ahead and efficient as a safety hygienist can minimize the potential for workplace accidents and save time and money in the long run.
You may want to check Occupational Hygienist, Hospital Hygienist, and Chemical Hygienist for alternative.
Job Description
- Conduct workplace safety inspections and assessments to identify potential hazards and develop appropriate controls.
- Develop and implement workplace safety policies and procedures.
- Monitor and enforce workplace safety regulations.
- Investigate workplace accidents and injuries.
- Design and deliver safety training programs and materials.
- Develop emergency response plans and coordinate emergency response drills.
- Develop and maintain safety records, reports, and other documents.
- Research safety-related topics and stay up to date on changes in safety regulations.
- Analyze data to identify trends in accidents and suggest corrective measures.
- Provide advice on safe work practices and hazardous conditions.
- Collaborate with occupational health nurses, medical providers, and other professionals to identify, evaluate, and control health hazards in the workplace.
- Monitor and evaluate compliance with OSHA regulations, company policies, and other safety standards.
- Create plans to reduce or eliminate hazardous environmental elements in the workplace.
- Facilitate risk management processes to identify and address potential safety issues.
- Monitor the use of personal protective equipment (PPE) to ensure proper use.
- Implement safety hygiene protocols such as hand washing and sanitation procedures.
Skills and Competencies to Have
- Knowledge of safety regulations, protocols and procedures.
- Ability to identify and assess potential hazards and recommend solutions.
- Knowledge of industrial hygiene principles, practices and standards.
- Ability to create written reports, policies and procedures.
- Knowledge of hazardous materials and chemical safety.
- Knowledge of OSHA and other applicable safety regulations.
- Proficiency in the use of personal protection equipment.
- Ability to use sampling, testing and measuring devices and instruments.
- Ability to evaluate the effectiveness of safety programs and make recommendations for improvement.
- Knowledge of emergency response procedures and emergency management systems.
Safety Hygienists play an integral role in protecting workers and the public from health risks associated with hazardous materials. They are responsible for monitoring and evaluating potential hazards, such as chemicals, biological agents, and radiation, in the workplace and in the environment. To do this effectively, Safety Hygienists must possess a wide range of skills and knowledge, including an understanding of safety standards, regulations, and procedures; familiarity with relevant hazardous materials; the ability to recognize and identify potential hazards; and the ability to design, implement, and evaluate safety programs.
In addition to these skills, Safety Hygienists must have strong communication and organizational abilities, be able to work independently, and be willing to stay abreast of current developments in the field. These skills are essential for ensuring the effectiveness of safety programs, protecting workers and the public from harm, and ensuring compliance with regulations.
Public Health Hygienist, Laser Hygienist, and Animal Hygienist are related jobs you may like.
Frequent Interview Questions
- What experience do you have in the field of safety hygiene?
- How would you ensure regulatory compliance when it comes to workplace safety?
- What strategies do you use to promote safety awareness among employees?
- How do you identify and manage safety hazards in the workplace?
- What experience do you have in developing and implementing safety policies?
- How do you analyze reports and data to identify safety trends?
- Describe a time when you had to handle a difficult situation related to workplace safety.
- What measures do you take to ensure that safety protocols are followed?
- How do you investigate and respond to employee safety complaints?
- What methods do you use to ensure that safety training is effective?
Common Tools in Industry
- Respirator. A device worn over the mouth and nose to filter out airborne particles and protect from hazardous materials. (Eg: 3M N95 Respirator).
- Eye Protection. Safety goggles or glasses used to protect the eyes from hazardous material or debris. (Eg: Uvex Safety Eyewear).
- Hearing Protection. Earplugs or earmuffs designed to reduce the risk of hearing loss due to loud noises. (Eg: Howard Leight Hearing Protection).
- Face Shield. A transparent shield worn over the face to protect it from hazardous materials and debris. (Eg: Ergodyne Face Shield).
- Gloves. Specialized gloves worn to protect hands from hazardous materials and chemicals. (Eg: Nitrile Gloves).
- Masks. A cloth or paper device worn over the mouth and nose to protect against dust, smoke, or other airborne particles. (Eg: Disposable Surgical Mask).
- Disinfectants. Chemicals used to kill bacteria, viruses, and other germs on surfaces and equipment. (Eg: Lysol Disinfectant Spray).
Professional Organizations to Know
- American Society for Healthcare Environmental Services (ASHES)
- International Association for Healthcare Security and Safety (IAHSS)
- American Association of Occupational Health Nurses (AAOHN)
- American Industrial Hygiene Association (AIHA)
- American Board of Industrial Hygiene (ABIH)
- National Environmental Health Association (NEHA)
- American Conference of Governmental Industrial Hygienists (ACGIH)
- The International Society of Indoor Air Quality and Climate (ISIAQ)
- American National Standards Institute (ANSI)
- Association of Occupational Health Professionals in Healthcare (AOHP)
We also have Oral Hygienist, Research Hygienist, and Podiatry Hygienist jobs reports.
Common Important Terms
- Occupational Health and Safety. Refers to the practice of protecting workers from health and safety risks while on the job.
- Industrial Hygiene. The science of anticipating, recognizing, evaluating, and controlling workplace conditions that may cause workers to be exposed to hazardous materials.
- Risk Assessment. The process of identifying hazards, assessing their potential to cause harm, and taking action to reduce the risk of harm.
- Hazard Control. The practice of preventing or reducing the potential for harm from a hazard by implementing a set of strategies or controls.
- Safety Engineering. The practice of designing systems, processes, and products with the intention of reducing or eliminating potential accidents and injuries.
- Emergency Planning. The process of creating plans for responding to natural disasters or other emergencies.
- Ergonomics. The practice of designing equipment and systems to be more user-friendly, efficient, and comfortable for workers.
Frequently Asked Questions
What qualifications are needed to become a Safety Hygienist?
To become a Safety Hygienist, a minimum of a bachelor's degree in Occupational Safety and Health, Industrial Hygiene, or a related field is typically required.
What type of duties does a Safety Hygienist typically perform?
Safety Hygienists typically perform duties such as conducting safety inspections, evaluating workplace hazards, recommending safety measures, and monitoring compliance with safety regulations.
What is the typical salary of a Safety Hygienist?
The median annual salary of a Safety Hygienist is approximately $65,000 per year.
What type of environment does a Safety Hygienist typically work in?
Safety Hygienists typically work in industrial settings, such as manufacturing plants or construction sites.
What type of certifications may be required of a Safety Hygienist?
A Safety Hygienist may be required to hold certifications such as Certified Industrial Hygienist (CIH), Certified Safety Professional (CSP), or Certified Hazardous Materials Manager (CHMM).
What are jobs related with Safety Hygienist?
- Radiological Hygienist
- Water Hygienist
- Food Hygienist
- Clinical Hygienist
- Environmental Hygienist
- Clinical Dental Hygienist
- Industrial Hygienist
- Radiation Hygienist
Web Resources
- Safety and Industrial Hygiene - ehs.ucsc.edu ehs.ucsc.edu
- Safety Services New Certified Industrial Hygienist safetyservices.ucdavis.edu
- Safety, Health and Industrial Hygiene Degree www.mtech.edu
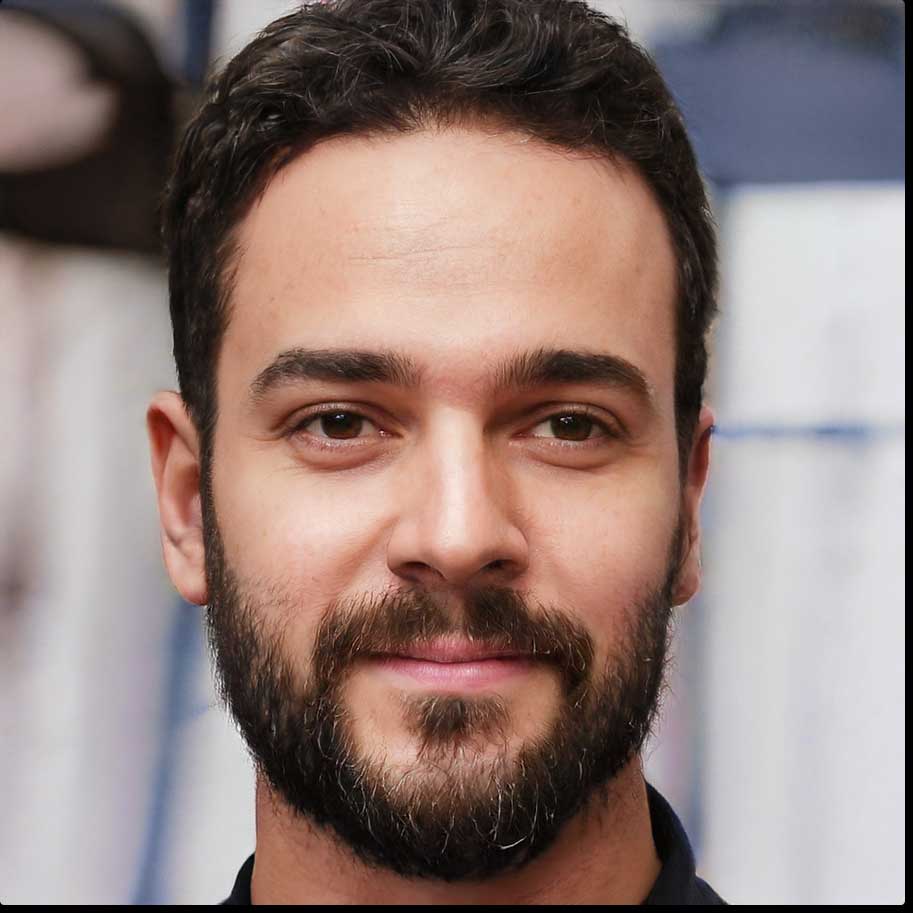