How to Be Occupational Hygienist - Job Description, Skills, and Interview Questions
Occupational hygienists play a vital role in preventing illness and injury in the workplace. They identify, evaluate, and control potential health hazards posed by physical, chemical, and biological agents in the environment, thereby protecting workers from exposure to hazardous materials. By recognizing the cause of health risks, they can develop strategies and procedures to reduce or eliminate them.
This can involve engineering controls, such as improved ventilation, use of protective equipment and clothing, and changes in work practices. In addition, occupational hygienists also assess and monitor existing work conditions to ensure compliance with safety regulations and guidelines. This may involve the use of dust sampling, noise surveys, and radiation measurement.
occupational hygienists help to create safe and healthy working environments for employees, thus reducing the risk of illness or injury.
Steps How to Become
- Obtain an undergraduate degree in a field related to occupational hygiene, such as biology, chemistry, engineering, or health science.
- Complete an accredited occupational hygiene program.
- Obtain certification from an approved organization, such as the American Board of Industrial Hygiene.
- Gain experience in the field through internships and other employment opportunities.
- Stay current on new developments and research in the field of occupational hygiene.
- Participate in continuing education activities and professional organizations to stay informed of trends and changes in the field.
- Maintain a current license to practice occupational hygiene in the jurisdiction where you are employed.
Occupational hygienists play an important role in protecting workers and the general public from hazardous conditions in the workplace. By evaluating the environment, they are able to identify and mitigate potential risks, such as exposure to hazardous materials and airborne contaminants. They assess the workplace for potential hazards, and then develop and implement a plan to reduce or eliminate them.
This helps to ensure that all employees are safe and that the work environment is not hazardous. Reliable and qualified occupational hygienists are essential for creating safe, healthy work environments. Without them, workers may be exposed to potentially dangerous conditions, putting their health and safety at risk.
You may want to check Animal Hygienist, Podiatry Hygienist, and Hospital Hygienist for alternative.
Job Description
- Develop and implement health and safety policies, procedures and systems in the workplace.
- Monitor and assess workplace conditions to identify potential hazards and risks.
- Analyze work environments to determine the presence of hazardous substances or conditions.
- Investigate accidents and incidents to identify root causes and recommend corrective action.
- Develop and implement hazardous materials management plans.
- Provide advice and guidance on how to reduce risk and ensure compliance with applicable laws and regulations.
- Prepare reports on findings and recommendations for corrective action.
- Educate employers, employees and other stakeholders about the importance of health and safety in the workplace.
- Monitor and evaluate health and safety initiatives to ensure effectiveness.
- Participate in hazard recognition and control programs.
Skills and Competencies to Have
- Knowledge of the principles of occupational hygiene and health and safety regulations.
- Knowledge of current health and safety legislation.
- Knowledge of the principles of toxicology, epidemiology, and industrial hygiene.
- Ability to identify workplace hazards and assess potential risks.
- Ability to assess noise levels, air quality, and hazardous substances in the workplace.
- Ability to develop, implement, and evaluate control measures.
- Ability to provide advice on health and safety issues to management and workers.
- Ability to communicate clearly and effectively with colleagues, employers, and clients.
- Ability to work independently and as part of a team.
- Ability to work accurately and efficiently under pressure.
- Knowledge of the use of appropriate monitoring equipment and techniques.
- Knowledge of computer software for data analysis, report writing, and presentation development.
Occupational Hygienists must possess a range of skills to be effective in their role. The most important skill an Occupational Hygienist should have is the ability to identify and assess potential risks in the workplace. This requires an understanding of the various sources of hazardous materials, the processes by which they enter the workplace, and their effects on workers.
Through a thorough risk assessment, an Occupational Hygienist can identify hazards and then develop appropriate controls to reduce or eliminate them. They must also have knowledge of engineering and administrative controls, personal protective equipment, and ventilation systems to ensure a safe work environment. Furthermore, occupational hygienists must have excellent communication skills to effectively educate employers and workers regarding safety and health hazards, as well as to provide advice on risk management strategies.
Finally, they must have good problem-solving skills to identify potential sources of harm and develop solutions. All of these skills are essential for an Occupational Hygienist to effectively reduce workplace risks.
Public Health Hygienist, Environmental Hygienist, and Food Hygienist are related jobs you may like.
Frequent Interview Questions
- What experience do you have in Occupational Hygiene?
- How would you assess a potential health hazard in the workplace?
- What measures would you take to control a health hazard?
- What procedures do you follow to assess the risk of exposure to hazardous materials?
- What methods of data collection do you use when monitoring hazardous workplaces?
- How do you ensure that safety and health standards are met in the workplace?
- How would you handle a situation where an employee is not following safety protocols?
- How do you ensure that Occupational Hygiene standards are being maintained throughout the company?
- Describe a successful Occupational Hygiene project that you have completed.
- What strategies do you use to keep up with industry standards and regulations?
Common Tools in Industry
- Dosimeter. A device used to measure levels of radiation (eg: Geiger counter).
- Particle Counter. A device used to measure the number of airborne particles in a given environment (eg: aerosol particle counter).
- Respirator. A device used to filter out hazardous particles from the air (eg: chemical cartridge respirator).
- Ventilation System. A system used to control air quality and reduce the risk of exposure to hazardous particles (eg: air filtration system).
- Air Sampler. A device used to collect air samples for analysis (eg: active air sampler).
- Protective Clothing. Clothing used to provide a barrier against hazardous substances (eg: chemical-resistant overalls).
- Noise Dosimeter. A device used to measure levels of noise (eg: sound level meter).
- Glove Box. A sealed container used to protect workers from hazardous materials (eg: glove box with ventilation).
- Lighting Measurement Device. A device used to measure the amount of light in an area (eg: lux meter).
- Gas Detector. A device used to detect hazardous gases (eg: combustible gas detector).
Professional Organizations to Know
- American Industrial Hygiene Association (AIHA)
- American Board of Industrial Hygiene (ABIH)
- British Occupational Hygiene Society (BOHS)
- National Institute for Occupational Safety and Health (NIOSH)
- Canadian Society of Safety Engineering (CSSE)
- European Industrial Hygiene Association (EIHA)
- International Occupational Hygiene Association (IOHA)
- American Society of Safety Professionals (ASSP)
- American Conference of Governmental Industrial Hygienists (ACGIH)
- International Labour Organization (ILO)
We also have Safety Hygienist, Oral Hygienist, and Research Hygienist jobs reports.
Common Important Terms
- Exposure Assessment. The process of determining the amount of a hazardous substance to which a person is exposed.
- Hazardous Substance. Any material or substance that has the potential to cause harm to human health or the environment, including physical, chemical, and biological agents.
- Risk Assessment. The process of evaluating the likelihood of harm from exposure to a hazardous substance.
- Contaminant. Any material that is foreign to the environment or that is present in concentrations which could cause harm to human health or the environment.
- Industrial Hygiene. The science of protecting and promoting the health and safety of workers and the environment.
- Air Quality. The quality of air in terms of its physical, chemical, and biological characteristics.
- Ergonomics. The study of how people interact with their environment, and how to design workspaces and equipment to optimize human performance and comfort.
- Occupational Health. The practice of preventing workplace illness and injury by identifying and controlling workplace hazards and promoting healthy work practices.
Frequently Asked Questions
Q1: What is an Occupational Hygienist? A1: An Occupational Hygienist is a professional trained to identify, assess, and control workplace health hazards, including physical, chemical, biological, and ergonomic hazards. Q2: What qualifications does an Occupational Hygienist need? A2: Occupational Hygienists typically require a minimum of a Bachelor's degree in Occupational Hygiene or a related field, plus significant work experience in occupational health and safety. Q3: What kind of work does an Occupational Hygienist do? A3: An Occupational Hygienists job involves assessing and controlling workplace health hazards, such as physical, chemical, biological, and ergonomic hazards, in order to protect the health of workers and the public. Q4: How can an Occupational Hygienist help protect workers and the public? A4: An Occupational Hygienist can help protect workers and the public by identifying workplace health hazards and then assessing and controlling them to ensure they are being managed safely and effectively. Q5: What is the average salary of an Occupational Hygienist? A5: According to data from PayScale.com, the average salary for an Occupational Hygienist is around $76,000 per year.What are jobs related with Occupational Hygienist?
- Clinical Dental Hygienist
- School Hygienist
- Laser Hygienist
- Industrial Hygienist
- Clinical Hygienist
- Radiological Hygienist
- Water Hygienist
- Chemical Hygienist
Web Resources
- Occupational Hygiene Harvard Education and Research Center www.hsph.harvard.edu
- Occupational Hygiene/Exposure Science | Environmental deohs.washington.edu
- Occupational Hygiene and Safety | Ohio University www.ohio.edu
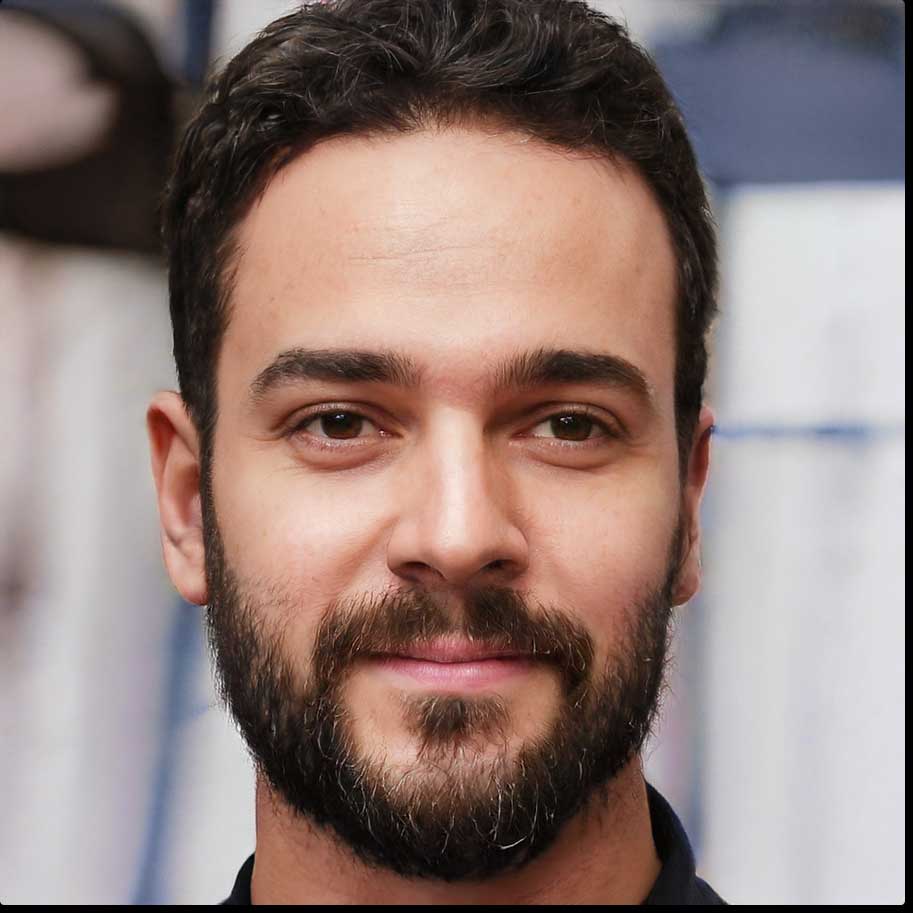