How to Be Safety Generalist - Job Description, Skills, and Interview Questions
The failure to comply with safety regulations can have a significant impact on an organization. If safety protocols are not followed, it can increase the risk of workplace accidents, resulting in costly medical expenses, legal liabilities, and even loss of life. Furthermore, an organization's reputation can be tarnished due to incidents resulting from negligence in following safety guidelines.
This can lead to a decrease in customer confidence and a negative impact on the organization's bottom line. To prevent these potential consequences, organizations must ensure that all staff are properly trained in safety policies, that safety protocols are followed, and that regular safety inspections are conducted. Taking these steps will create a safer environment for everyone and help to protect the business from liability.
Steps How to Become
- Obtain a bachelor's degree in safety, health, or engineering. Most employers prefer to hire Safety Generalists with a degree related to safety management, industrial hygiene, engineering, or risk management. Students should look for accredited programs that offer safety-specific courses and internships to gain experience.
- Get certified. Earning a professional certification can improve job prospects and demonstrate a commitment to safety. The Board of Certified Safety Professionals offers a Certified Safety Professional (CSP) credential that requires passing an exam and meeting experience requirements.
- Gain experience. Many employers require Safety Generalists to have at least two years of experience managing safety programs in an industrial or construction setting. Internships and volunteer positions provide excellent opportunities to gain experience and learn about safety management.
- Stay up-to-date on safety regulations. Safety Generalists must stay up-to-date on applicable safety regulations, including OSHA rules and local laws. They should also keep abreast of advances in safety technologies and trends in the industry.
- Develop strong communication and problem-solving skills. Safety Generalists must be able to communicate effectively with all levels of the organization and have strong problem-solving skills to identify and address safety hazards.
You may want to check Help Desk Generalist, Administrative Generalist, and Business Systems Analysis Generalist for alternative.
Job Description
- Develop and implement safety policies and procedures to ensure a safe work environment.
- Monitor and inspect workplace conditions to assess compliance with safety regulations.
- Investigate and analyze work-related accidents and incidents to identify causes and recommend corrective action.
- Prepare safety reports for management and government agencies.
- Educate employees on safety practices, policies, and procedures.
- Develop and deliver safety training programs and materials.
- Monitor operational activities for compliance with safety regulations.
- Coordinate emergency response plans and drills.
- Maintain records of safety inspections and equipment tests.
- Participate in and lead safety committee meetings.
- Evaluate contractor safety performance.
- Recommend safety equipment, supplies, and personal protective equipment (PPE).
- Assist with the development of emergency response plans and evacuation procedures.
- Implement safety processes to ensure compliance with OSHA regulations.
- Implement safety initiatives such as safety audits, incident tracking, and hazard identification/control.
Skills and Competencies to Have
- Knowledge of safety regulations, standards and codes
- Ability to analyze safety data, identify trends and recommend corrective actions
- Excellent communication, interpersonal and problem-solving skills
- Experience in conducting safety audits and inspections
- Proficient in the use of computers, software and other safety-related technology
- Knowledge of emergency response protocols
- Ability to develop and implement safety policies and procedures
- Knowledge of OSHA and other relevant safety regulations
- Ability to train personnel in safety procedures
- Familiarity with hazardous materials management
- Ability to investigate workplace accidents and recommend corrective actions
- Ability to develop workplace wellness programs
- Knowledge of ergonomics and workplace safety practices
- Ability to develop and implement safety incentive programs
- Experience in developing emergency preparedness plans
Safety generalists are essential for any business to ensure the safety of their employees and customers. Their role is to identify, assess, and control potential risks in the workplace that could lead to accidents, injuries, or illnesses. To be successful in this role, it is essential for safety generalists to have strong communication skills, problem-solving abilities, and a working knowledge of applicable laws, regulations, and standards.
By having these skills, they can effectively identify potential hazards and take steps to reduce the risk of harm. they should be able to create safety policies and procedures that employees can follow to ensure they are operating safely while on the job. The results of their efforts can lead to fewer workplace accidents, lower costs associated with workers' compensation claims, and improved morale among employees.
Facility Management Generalist, Public Relations Generalist, and Operations Generalist are related jobs you may like.
Frequent Interview Questions
- What experience do you have in safety generalist roles?
- Describe a safety incident you handled and the steps you took to prevent it from happening again.
- How would you handle a situation where an employee disregards safety protocols?
- What safety certifications do you possess?
- What methods do you use to keep employees informed of changes in safety protocols?
- How would you handle a situation where an employee is not following safety guidelines?
- What safety training have you conducted in the past?
- How do you stay up-to-date on new safety regulations?
- Describe a time when you had to confront a difficult situation related to safety.
- What strategies do you use to ensure that safety remains a priority in the workplace?
Common Tools in Industry
- Ergonomic Assessment Tool. A tool used to assess the ergonomic safety of a work environment and identify potential ergonomic issues. (e. g. REBA - Rapid Entire Body Assessment)
- Job Hazard Analysis Tool. A tool used to record and analyze potential hazards associated with a specific job or task. (e. g. JSA - Job Safety Analysis)
- Risk Assessment Tool. A tool used to identify, assess, and control workplace risks. (e. g. BowTie Risk Assessment)
- Incident Investigation Tool. A tool used to investigate and analyze workplace incidents or accidents in order to identify ways to prevent similar incidents from occurring in the future. (e. g. 5-Why Incident Investigation Method)
- Risk Management Tool. A tool used to identify, assess, and control risks and create a risk management plan. (e. g. Risk Matrix)
- Safety Audit Tool. A tool used to inspect a workplace and identify potential hazards, violations of safety regulations, and areas for improvement. (e. g. OSHA Safety Audit Checklist)
- Personal Protective Equipment (PPE) Tool. A tool used to assess the need for PPE in a workplace and ensure it is being used correctly. (e. g. PPE Selection Matrix)
- Training Tool. A tool used to provide employees with job-related safety training to ensure they are adequately prepared for their tasks. (e. g. Safety Training Video Library)
Professional Organizations to Know
- American Society of Safety Professionals (ASSP)
- Institute of Hazardous Materials Management (IHMM)
- National Fire Protection Association (NFPA)
- National Safety Council (NSC)
- American Industrial Hygiene Association (AIHA)
- Occupational Safety and Health Administration (OSHA)
- The Board of Certified Safety Professionals (BCSP)
- American Conference of Governmental Industrial Hygienists (ACGIH)
- The International Safety Equipment Association (ISEA)
- The International Institute of Risk and Safety Management (IIRSM)
We also have Security Generalist, Maintenance Generalist, and Real Estate Management Generalist jobs reports.
Common Important Terms
- Safety Management System. A set of laws, practices, and procedures intended to protect people and property from potential harm.
- Risk Assessment. The process of identifying potential hazards and evaluating the risks associated with them.
- Hazard Analysis. A systematic evaluation of the potential risks posed by a particular situation or activity.
- Incident Investigation. A process of gathering and analyzing facts to determine the root cause of an incident.
- Incident Reporting. The process of documenting an incident for the purpose of understanding why it happened and how to prevent it from occurring again.
- Emergency Response Plan. A plan outlining how to respond to an emergency situation.
- Regulatory Compliance. Meeting all applicable health and safety regulations.
- Training and Education. Providing employees with the necessary knowledge and skills to do their jobs safely.
- Occupational Health and Safety. The practice of protecting workers from physical, mental, and emotional harm.
- Ergonomics. The science of designing workstations and tools that minimize the risk of injury or illness.
Frequently Asked Questions
Q1: What is a Safety Generalist? A1: A Safety Generalist is a professional who is responsible for developing, implementing, and overseeing safety protocols and procedures in the workplace. Q2: What qualifications are required for a Safety Generalist? A2: Most employers require Safety Generalists to have a bachelor's degree in occupational safety, industrial hygiene, or a related field, as well as several years of experience in the industry. Q3: What duties does a Safety Generalist perform? A3: A Safety Generalist is responsible for identifying and assessing workplace hazards, creating and enforcing safety policies and procedures, conducting training sessions, and investigating accidents. Q4: How much does a Safety Generalist earn? A4: On average, Safety Generalists earn an annual salary of around $70,000. Q5: What types of organizations hire Safety Generalists? A5: Safety Generalists are employed by a variety of organizations, such as manufacturing companies, construction companies, healthcare facilities, and government agencies.What are jobs related with Safety Generalist?
- Logistics Generalist
- Business Intelligence Generalist
- Database Administration Generalist
- Legal Generalist
- Financial Generalist
- Accounting Generalist
- Project Management Generalist
- Quality Assurance Generalist
- Quality Control Generalist
- Social Media Generalist
Web Resources
- Environmental Health & Safety Staff Listing | Safety Services safetyservices.ucdavis.edu
- Environmental Health & Safety Generalist Certificate catalog.cccneb.edu
- EH&S Generalist | Learning Center - UC Santa Barbara www.learningcenter.ucsb.edu
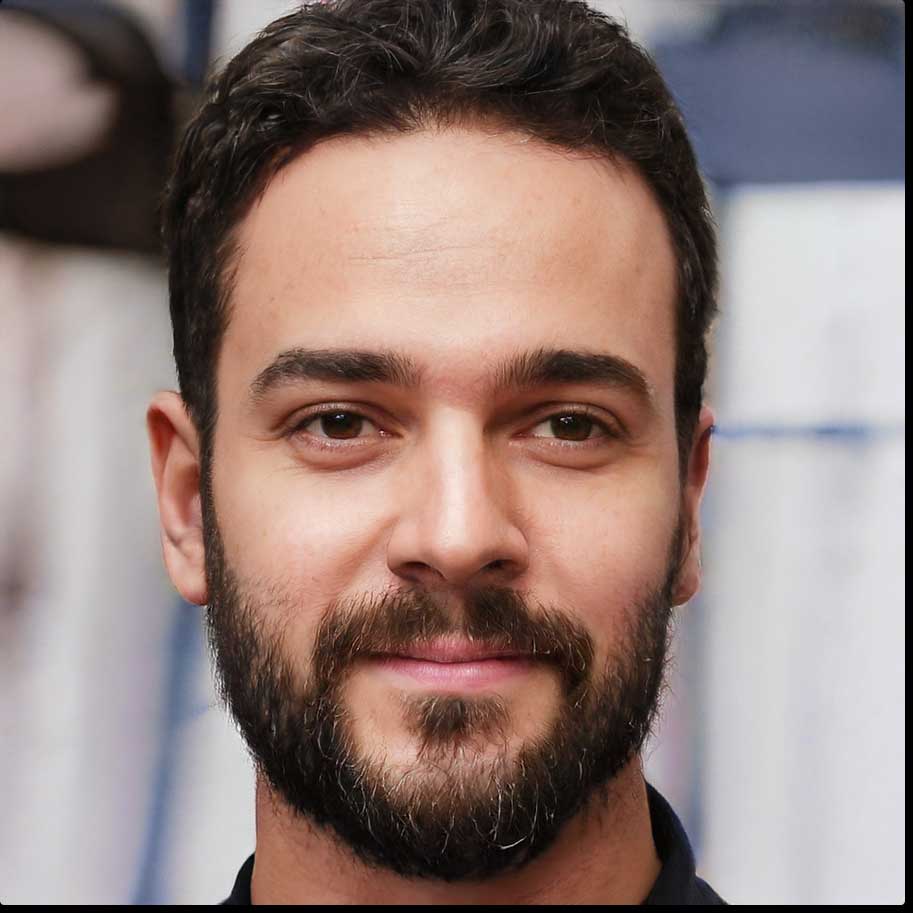