How to Be Quality Control Generalist - Job Description, Skills, and Interview Questions
Steps How to Become
- Earn a Bachelors Degree. A bachelors degree in a field related to quality control is the minimum educational requirement for most quality control generalist positions. A degree in industrial or mechanical engineering, business administration, or quality assurance is common for quality control generalists.
- Gain Work Experience. Quality control generalists typically gain work experience in quality control, engineering, or production roles. Working as a production technician, quality assurance technician, or quality control engineer are all good ways to gain experience in quality control.
- Obtain Professional Certification. Many employers prefer to hire candidates who have professional certification in quality control. The American Society for Quality offers several certifications in the field of quality control.
- Network with Industry Professionals. Networking with industry professionals can help aspiring quality control generalists stay up to date on the latest developments in the field and learn about job openings. Attending professional conferences, joining industry associations, and connecting with contacts on LinkedIn can all help quality control generalists build their networks.
- Develop Technical Skills. Quality control generalists need to be proficient in use of computers and other technical equipment, such as thermometers and microscopes. They must also be knowledgeable about the industry regulations and standards that apply to their organizations products and services.
The quality control generalist must stay up to date and competent in their field to ensure that operational processes remain efficient and effective. To do this, they must stay informed of the latest industry trends, technology, and regulations. They must also possess strong problem-solving and analytical skills, as well as a thorough understanding of quality control principles and practices.
they must have excellent communication skills to effectively collaborate with team members, customers, vendors, and other stakeholders. Finally, they must be detail-oriented and organized to ensure that tasks are completed accurately and on time. By taking these steps, the quality control generalist can maintain the highest standards of excellence in their work and help ensure that their organization meets all of its operational goals.
You may want to check Public Relations Generalist, Leadership Development Generalist, and Accounting Generalist for alternative.
Job Description
- Ensure accuracy and quality of all products produced
- Monitor production line for any defects and errors
- Monitor compliance with ISO and other relevant regulations
- Execute quality tests and inspections to ensure product meets standards
- Develop and maintain quality control systems
- Create and implement corrective action plans
- Investigate customer complaints and feedback
- Document quality assurance activities and results
- Maintain a safe and organized work environment
- Train and supervise other quality control personnel
Skills and Competencies to Have
- Understanding of quality control processes
- Knowledge of relevant quality control standards
- Ability to interpret technical documents
- Proficiency in data analysis
- Excellent problem-solving skills
- Strong verbal and written communication
- Ability to work independently and collaboratively
- Attention to detail and accuracy
- Ability to use quality control tools and equipment
- Good organizational skills and time management
Quality control generalists are essential to any business, as they are responsible for ensuring that all products and services meet the highest standards of quality. Without a quality control generalist, companies would be unable to provide their customers with a consistent and reliable product. Quality control generalists must possess strong technical skills to identify problems, fault tolerance to withstand pressure, and excellent communication skills to effectively convey issues to management.
they must be able to work well under pressure, think logically and analytically, and be proficient in problem solving and decision making. Quality control generalists must also have an eye for detail and be able to determine whether a product or service meets the necessary specifications. As quality control is an integral part of a companys success, the quality control generalist plays a crucial role in ensuring the companys success by providing quality assurance and customer satisfaction.
Business Development Generalist, Compliance Generalist, and Network Administration Generalist are related jobs you may like.
Frequent Interview Questions
- What experience do you have in quality control?
- How do you ensure that quality standards are met?
- How do you handle difficult customer feedback?
- What steps do you take to ensure accuracy and reliability in data collection?
- What methods do you use to evaluate quality control processes?
- How do you stay current with industry standards and trends?
- How have you successfully identified and solved quality problems?
- Describe a time when you faced a difficult challenge in a quality control role.
- What processes do you use to review and test new products or services?
- How do you work with others to ensure quality assurance?
Common Tools in Industry
- Quality Control Checklist. A checklist that outlines the criteria for quality control, and is used to track the progress of a product or service. (eg: Product Quality Control Checklist)
- Statistical Process Control (SPC). A method of quality control that uses statistical methods to monitor and control the quality of a product or process. (eg: SPC Charting)
- Root Cause Analysis. A structured approach to investigating and identifying the root cause of an issue. (eg: Fishbone Diagram)
- Process Mapping. A technique that uses diagrams to visually represent a process, and can be used to identify areas for improvement. (eg: Value Stream Mapping)
- Audits and Assessments. A systematic review of a process, product, or service to identify any areas for improvement. (eg: Quality System Audit)
- Quality Management Software. A software application used to track, analyze, and report on quality control data. (eg: Quality Management System)
Professional Organizations to Know
- American Society for Quality (ASQ)
- International Quality Federation (IQF)
- International Organization for Standardization (ISO)
- American National Standards Institute (ANSI)
- National Institute of Standards and Technology (NIST)
- Institute of Electrical and Electronics Engineers (IEEE)
- The International Accreditation Forum (IAF)
- International Register of Certificated Auditors (IRCA)
- Association for Quality and Participation (AQP)
- Malcolm Baldrige National Quality Award (MBNQA)
We also have Tax Accounting Generalist, Operations Generalist, and Customer Service Generalist jobs reports.
Common Important Terms
- Quality Assurance. The process of ensuring that products and services meet customer expectations and industry standards.
- Quality Control. The process of identifying and correcting errors and defects in products or services to ensure that they meet quality requirements.
- Quality Management. The overall process of managing and improving the quality of products and services.
- Risk Management. The process of identifying, assessing, and controlling risks associated with activities, processes, and operations to ensure that they are managed effectively.
- ISO 9001. An international standard for quality management systems that specifies requirements for an organizations processes and procedures.
- Six Sigma. A set of strategies and tools for improving the quality of products and services by focusing on reducing variation and eliminating defects.
- Kaizen. A Japanese philosophy of continuous improvement focusing on small, incremental changes that can make a big difference over time.
- Root Cause Analysis. A problem-solving technique used to identify the underlying causes of problems so that corrective action can be taken to prevent future occurrences.
Frequently Asked Questions
What is the role of a Quality Control Generalist?
A Quality Control Generalist is responsible for ensuring the quality of products and services by conducting inspections and testing, analyzing data and results, and recommending corrective actions. The Generalist is also responsible for developing and implementing quality control systems and processes to ensure compliance with industry standards.
What skillset is required to be a Quality Control Generalist?
Quality Control Generalists must possess strong technical, analytical, problem-solving, and communication skills. They should also be familiar with quality control systems and processes, have a good understanding of statistical principles and methods, and experience in data analysis and interpretation.
How often is Quality Control testing conducted?
Quality Control testing is typically conducted on a regular basis, depending on the type of product or service being tested. Generally, testing is conducted at least once a month or at any time when new products are introduced or changes are made to existing products or services.
What is the purpose of Quality Control testing?
The purpose of Quality Control testing is to ensure that all products and services meet the standards established by the organization or industry. Quality Control testing helps identify any potential defects or issues, as well as areas where improvements can be made.
What are some common Quality Control tools and techniques?
Common Quality Control tools and techniques include visual inspection, sampling, dimensional checks, gauges and measurement devices, statistical process control (SPC), root cause analysis, benchmarking, and failure mode and effects analysis (FMEA).
What are jobs related with Quality Control Generalist?
- Financial Generalist
- Help Desk Generalist
- Software Engineering Generalist
- Retail Operations Generalist
- Education Generalist
- Real Estate Management Generalist
- Business Systems Analysis Generalist
- Database Administration Generalist
- Marketing Generalist
- Facility Management Generalist
Web Resources
- What Does a Quality Control Inspector Do? | Goodwin University www.goodwin.edu
- Quality Control Course | Engineering Courses | Purdue Online engineering.purdue.edu
- What is a Manufacturing Quality Controller? | Goodwin University www.goodwin.edu
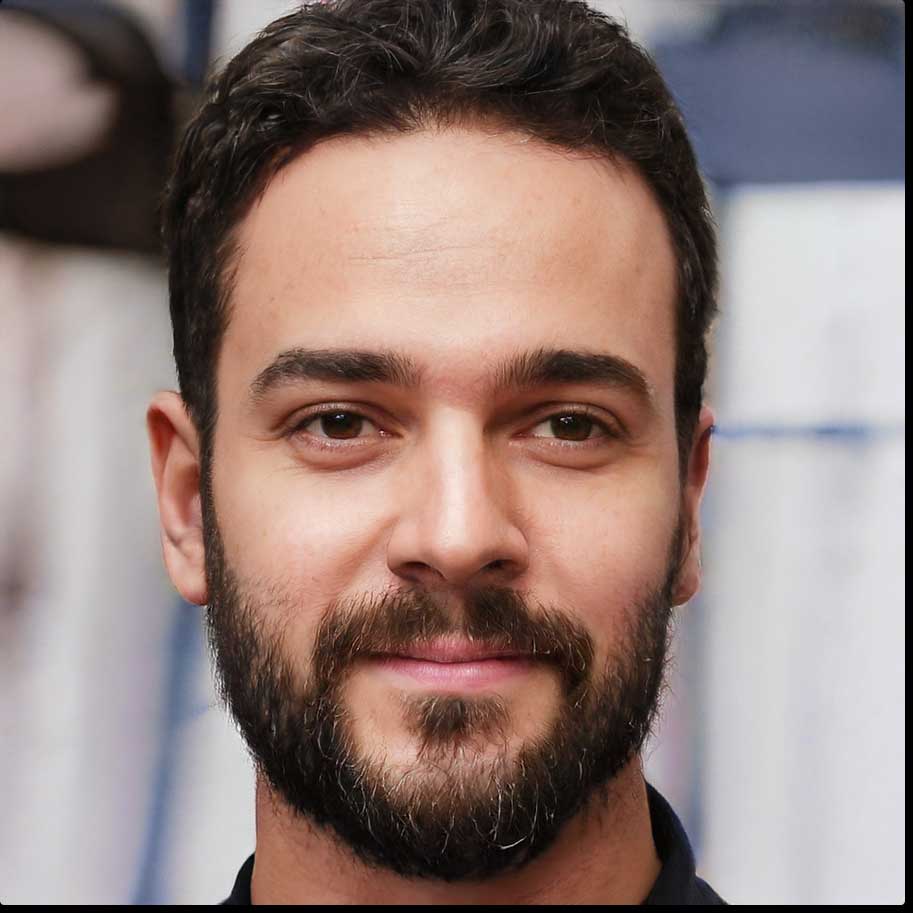