How to Be Rock Crushing Operator - Job Description, Skills, and Interview Questions
The job of a rock crushing operator is an important role in the mining industry as it involves operating heavy machinery to break down large rocks into smaller and more manageable pieces. This process is essential to extracting valuable minerals and materials from the earth, which can then be used in the production of a variety of products. The operator must have a high level of skill and understanding of the machinerys operation and safety protocols.
In addition to their technical abilities, they must also be able to think critically and problem solve on the spot as issues may arise during the process. Failure to properly operate the machinery can lead to serious injury or even death, so it is essential that operators are well-trained and follow all safety procedures. Furthermore, if the operator does not produce the desired end result, it can result in significant financial losses for the mining company.
Steps How to Become
- Obtain a high school diploma or equivalent. Prospective rock crushing operators should begin their career path by obtaining a high school diploma or equivalent. This will help to ensure success in a postsecondary education or training program.
- Complete a postsecondary degree or certificate program. Many employers prefer to hire rock crushing operators with a postsecondary degree or certificate in a related field. Programs may offer courses in mathematics, physics, chemistry, geology, and other related sciences.
- Pursue on-the-job training. Many employers may provide on-the-job training for prospective rock crushing operators. This may include instruction on how to safely and effectively operate the equipment used in rock crushing operations.
- Obtain certification. Depending on the state, some employers may require prospective rock crushing operators to obtain certification from a professional organization. Obtaining certification can demonstrate dedication and competence to potential employers.
- Obtain a drivers license. Prospective rock crushing operators will likely need to possess a valid drivers license in order to transport the equipment needed for their job.
You may want to check Rock Painter, Rock Excavator Operator, and Rock Blasting Supervisor for alternative.
Job Description
- Rock Crusher Operator: Operates and maintains rock crushing equipment, including but not limited to: jaw and cone crushers, vibrating screens, conveyors, and other related rock crushing machinery.
- Rock Blasting Operator: Responsible for setting up and detonating explosives in order to break up rock formations for the purpose of extracting minerals or other materials.
- Loader Operator: Operates a loader or other heavy equipment to load blasted material into trucks or other transportation vehicles.
- Heavy Hauler Operator: Responsible for hauling large quantities of blasted material from the work site.
- Crusher Maintenance Technician: Performs maintenance and repairs on crushers and related rock crushing machinery to ensure safe and efficient operation.
- Quarry Manager: Supervises the daily activities of the quarry operations, including drilling, blasting, loading, hauling, and processing of materials.
Skills and Competencies to Have
- Knowledge of rock crushing and screening equipment
- Ability to read and interpret blueprints and technical manuals
- Knowledge of workplace safety rules and regulations
- Ability to follow instructions and work independently
- Ability to troubleshoot and perform minor repairs
- Good physical strength and endurance
- Good communication and interpersonal skills
- Ability to work in a fast-paced environment
- Ability to lift heavy loads safely
- Knowledge of local, state, and federal regulations regarding safety and environmental protection
The ability to operate rock crushing machinery is an essential skill for any operator in the quarry and mining industry. This skill requires experience, patience and safety awareness. The consequence of failing to have this expertise can be costly, including expensive damage to the machinery, potential injury to the operator, and decreased productivity.
Furthermore, operating rock crushing machines requires the operator to understand how to set up the machine, adjust the settings, and ensure that it is running efficiently and safely. If an operator fails to understand these concepts, they may not be able to maximize the production output or operate the machine safely. As a result, they could also put themselves and their colleagues in danger.
To ensure a successful operation, it is essential that all operators possess the right skills and knowledge.
Rock Engineer, Rock Driller, and Rock Crusher Maintenance Technician are related jobs you may like.
Frequent Interview Questions
- What experience do you have operating a rock crusher?
- What safety measures do you take when operating a rock crusher?
- How do you ensure the accuracy of the output materials?
- How do you troubleshoot a problem with a rock crusher?
- What do you consider to be the important characteristics of a rock crushing operator?
- Describe a situation where you had to make a difficult decision while operating a rock crusher.
- What challenges have you faced while operating a rock crusher?
- What quality control measures do you take when operating a rock crusher?
- What have been the biggest successes in your past experience with operating a rock crusher?
- How have you kept up to date with the latest technologies in rock crushing?
Common Tools in Industry
- Jackhammer. A handheld tool used to break up hard materials such as rocks and concrete (eg: using it to break up a large rock).
- Shovel. A tool with a long handle and a wide blade used for digging (eg: using it to move the broken rock pieces from one place to another).
- Pneumatic Hammer. A tool powered by compressed air that is used to break up hard materials such as rocks and concrete (eg: using it to chip away at larger rocks).
- Excavator. A large machine with a long arm used to move and dig large amounts of earth and rocks (eg: using it to excavate an area where rocks need to be broken up).
- Sledgehammer. A heavy hammer with a long handle used for breaking up hard materials such as rocks and concrete (eg: using it to break up a large rock into smaller pieces).
- Rock Crusher. A machine with a rotating drum that breaks up rocks into smaller pieces (eg: using it to reduce large rocks into smaller, manageable pieces).
Professional Organizations to Know
- National Stone, Sand & Gravel Association (NSSGA)
- Association of Equipment Manufacturers (AEM)
- Mine Safety and Health Administration (MSHA)
- United States Mine Rescue Association (USMRA)
- National Mining Association (NMA)
- National Association of Rock Crushing Operators (NARCO)
- International Society of Explosives Engineers (ISEE)
- American Rock Mechanics Association (ARMA)
- Aggregates & Roadbuilding Magazine
- International Union of Operating Engineers (IUOE)
We also have Rock Quarry Manager, Rock Grinder Operator, and Rock Truck Driver jobs reports.
Common Important Terms
- Excavation. The process of removing earth from a given area in order to create a space for construction or other activities.
- Aggregates. Small pieces of crushed rock used to create concrete and asphalt surfaces.
- Blasting. A process of using explosives to break up large chunks of rock into smaller pieces.
- Rock Crusher. A machine used to crush rocks into smaller pieces.
- Screener. A device used to separate rocks of different sizes and shapes.
- Loader. A machine used to transport materials such as aggregate or dirt.
- Hauling. The process of transporting rock, aggregate, or dirt by truck.
- Drilling. The process of creating holes in the ground for blasting, excavation, or other activities.
Frequently Asked Questions
What does a Rock Crushing Operator do?
A Rock Crushing Operator is responsible for operating and maintaining a rock crushing plant to produce aggregate materials. This includes monitoring the operation of the plant, adjusting the settings to produce the desired material, inspecting and maintaining the equipment, and keeping accurate records of production.
What qualifications are needed for a Rock Crushing Operator?
To become a Rock Crushing Operator, you will typically need a high school diploma or GED, and prior experience in an industrial setting operating heavy machinery. Additionally, knowledge of safety protocols, mechanical aptitude, and attention to detail are important skills.
What safety procedures must be followed while operating the rock crusher?
Rock Crushing Operators must ensure that all safety protocols are followed while operating the rock crusher. This includes wearing the appropriate personal protective equipment (PPE) at all times, adhering to lockout-tagout procedures, and following all safety and operational guidelines provided by the manufacturer.
How often should a Rock Crushing Operator inspect the equipment?
Rock Crushing Operators should inspect the equipment at least daily, paying close attention to any wear or damage that may occur. Additionally, more thorough inspections should be performed on a regular basis in accordance with manufacturer guidelines.
What type of records must a Rock Crushing Operator keep?
Rock Crushing Operators must keep accurate records of their production and any maintenance performed on the equipment. These records should include daily production amounts, machine settings, and maintenance log entries.
What are jobs related with Rock Crushing Operator?
- Rock Reclamation Specialist
- Rock Quarry Supervisor
- Rock Mining Supervisor
- Rock Blaster
- Rock Hauler
- Rock Geologist
- Rock Climbing Instructor
- Rock Structure Analyst
- Rock Splitter
Web Resources
- Rock crushing operation in Florida, 1955 | ArchivesSpace Public archives.library.rice.edu
- Rock Preparation and Mineral Separation Facilities www.geol.umd.edu
- Uganda Rock Crusher | HYdrogen Properties for Energy Research (HYP hydrogen.wsu.edu
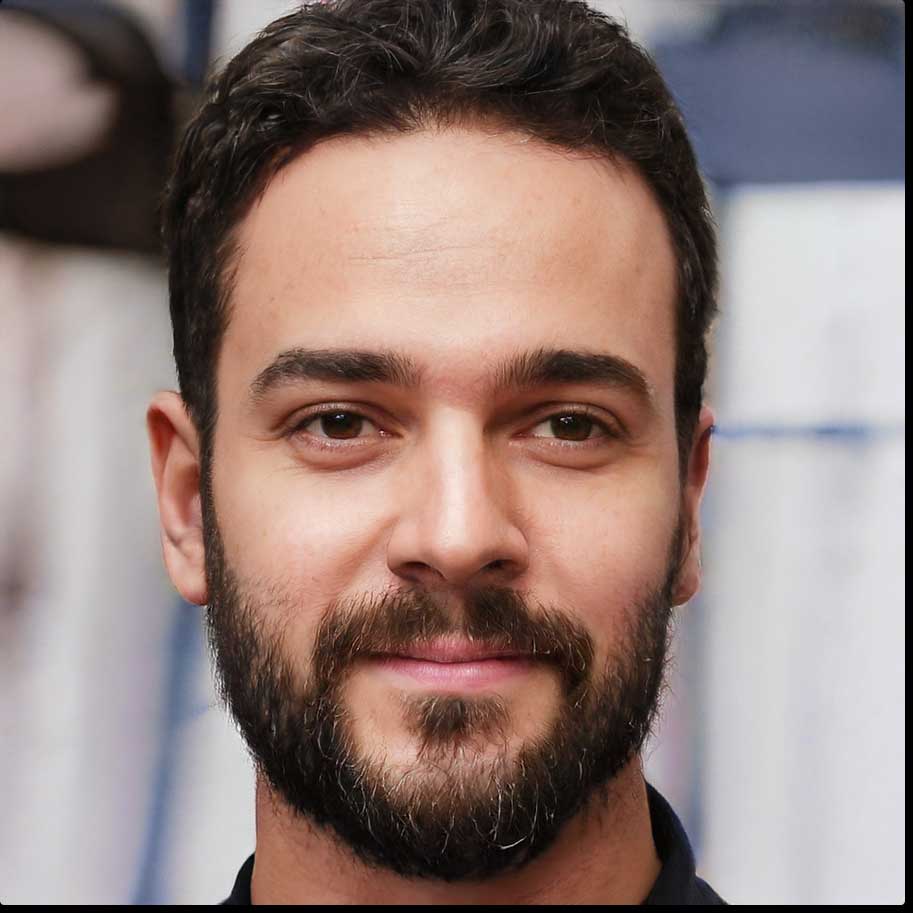