How to Be Repair Manager - Job Description, Skills, and Interview Questions
The lack of a reliable repair manager can have a negative effect on a business. Without the help of a repair manager to coordinate and oversee repairs and maintenance, employees may struggle to keep up with the demands of their job. This can lead to a decrease in productivity, as well as an increase in the cost and time it takes to complete repairs.
customers may become frustrated with the slow response times, resulting in a decline in customer satisfaction. By hiring an experienced repair manager, businesses can ensure that repairs are completed quickly and efficiently, while also improving customer relations.
Steps How to Become
- Earn a Bachelor's Degree. A bachelor's degree in a related field such as engineering, business management, or a specialized degree in facility management or maintenance is usually required to become a repair manager. Coursework may include topics in electricity, electronics, facility maintenance, project management, and business administration.
- Obtain Relevant Work Experience. While some employers may hire a repair manager with a bachelor's degree in the field, most employers prefer to hire those with a few years of experience in a related repair or maintenance position. Experience in the installation and repair of mechanical, electrical, and electronic equipment is ideal for this type of position.
- Obtain Certification or Licensure. Many repair managers choose to become certified or licensed in either the field they specialize in or their state. Depending on the state, some repair managers may be required to obtain a license or certification in order to work.
- Pursue Management Training. Most repair managers receive on-the-job training, as well as additional training from their employers on management techniques. These techniques may include cost estimation and budgeting, scheduling, and personnel management.
- Stay Up-To-Date on Industry Trends. Repair managers should stay up-to-date on the latest industry trends and technologies in order to remain competitive in the field. This may include attending seminars, reading trade publications, and networking with other professionals in the field.
You may want to check Farm Equipment Repair Technician, Automotive Repair Technician, and Repair Electrician for alternative.
Job Description
- Hire and train technicians to ensure a knowledgeable and skilled maintenance staff.
- Estimate job costs and prepare estimates for customers.
- Develop and oversee preventative maintenance programs.
- Ensure that repairs are completed in a timely and cost effective manner.
- Monitor customer feedback and address any issues or complaints.
- Source, purchase and maintain repair parts inventory.
- Develop and implement safety policies and procedures.
- Analyze repair data to identify trends and develop strategies for improvement.
- Monitor and review repair costs to ensure budget compliance.
- Maintain a high level of customer service by responding to inquiries in a timely manner.
Skills and Competencies to Have
- Knowledge of repair and maintenance processes
- Familiarity with relevant industry standards and regulations
- Ability to troubleshoot and identify root causes of equipment failure
- Excellent communication and customer service skills
- Ability to work efficiently and manage multiple priorities
- Strong organizational and time management skills
- Ability to quickly assess and make decisions in a fast-paced environment
- Proficiency in utilizing computer software programs for tracking repairs and maintenance
- Ability to handle challenging situations in a professional manner
- Knowledge of safety practices and procedures
Good repair managers must possess a variety of skills in order to ensure that their team is running efficiently and providing quality service to customers. The most important skill for a repair manager to have is strong leadership. A good leader will be able to motivate their team and create a work environment that is both efficient and enjoyable.
They must also have excellent communication skills in order to be able to communicate clearly with their team and customers. they must have excellent problem-solving skills, as they will be responsible for finding solutions to customer issues and ensuring that the repair process runs smoothly. Lastly, repair managers must have good organizational skills in order to stay on top of all the paperwork involved in the repair process and ensure that customer orders are processed efficiently.
By having these skills, a repair manager can create an effective team that provides quality customer service.
Repair Installer, Fleet Maintenance and Repair Technician, and Repair Technician Apprentice are related jobs you may like.
Frequent Interview Questions
- What experience do you have in repair management?
- What have you done to stay up-to-date on new developments and trends in the repair industry?
- How do you prioritize conflicting repair requests?
- How do you ensure quality control when overseeing repairs?
- What strategies do you use to maintain customer satisfaction with repair services?
- How would you handle a difficult customer complaint regarding repairs?
- How do you manage staff to ensure repair deadlines are met?
- What experience do you have managing a budget for repair services?
- How do you handle situations where parts or tools need to be ordered for repairs?
- What safety protocols do you follow to ensure a safe work environment for repair staff?
Common Tools in Industry
- Hammer. Used to drive nails into materials, (eg: driving in nails to build a fence).
- Screwdriver. Used to drive screws, (eg: installing a door handle).
- Pliers. Used for gripping and cutting, (eg: gripping a pipe to cut it).
- Drill. Used to bore holes into materials, (eg: drilling a hole in a wall).
- Wrench. Used to tighten or loosen nuts and bolts, (eg: changing the wheels on a car).
- Socket Wrench. Used to turn nuts and bolts, (eg: tightening a bolt on a bike).
- Air Compressor. Used to power tools like nail guns, (eg: using a nail gun to build a deck).
- Saw. Used to cut through materials, (eg: cutting lumber for a framing project).
- Level. Used to make sure surfaces are even, (eg: leveling the foundation of a house).
- Tape Measure. Used to measure distances, (eg: measuring the area of a room).
Professional Organizations to Know
- Air Conditioning Contractors of America (ACCA)
- American Institute of Architects (AIA)
- American Society of Heating, Refrigerating, and Air Conditioning Engineers (ASHRAE)
- Building Performance Institute (BPI)
- National Association of Home Builders (NAHB)
- National Electrical Contractors Association (NECA)
- Plumbing-Heating-Cooling Contractors Association (PHCC)
- Sheet Metal and Air Conditioning ContractorsÂ’ National Association (SMACNA)
- Refrigeration Service Engineers Society (RSES)
- American Society of Plumbing Engineers (ASPE)
We also have Auto Body and Paint Repair Technician, Appliance Repair Technician, and Military Aircraft Repairer jobs reports.
Common Important Terms
- Diagnosis. The process of identifying the cause of a problem or malfunction.
- Troubleshooting. A systematic process of finding and fixing issues or problems.
- Maintenance. The act of regularly inspecting and servicing equipment or systems to ensure they continue to operate properly.
- Spare Parts. Replacement components that are kept in stock for use in the event of a breakdown.
- Quality Assurance. A system of activities designed to ensure that products or services meet a certain level of quality.
- Safety Regulations. Legal requirements that must be met when using certain types of equipment or performing certain types of work.
- Warranty. A guarantee that a product or service will meet certain standards or be replaced if it fails to do so.
Frequently Asked Questions
What is the purpose of Repair Manager?
Repair Manager is a software solution designed to help businesses manage the repair and maintenance of their products and assets. It provides tools and features such as tracking repair orders, scheduling maintenance activities, and tracking repair costs.
What features does Repair Manager offer?
Repair Manager offers features such as tracking repair orders, scheduling maintenance activities, and tracking repair costs. It also provides tools for creating custom reports, tracking inventory levels, and generating quotes for repair services.
How much does Repair Manager cost?
The cost of Repair Manager varies depending on the size of your business. Generally, plans start at $50/month and can go up to $200/month for larger businesses.
What platforms does Repair Manager support?
Repair Manager is available as a web-based application that can be accessed from any computer or mobile device with an internet connection. It also supports iOS and Android devices.
What types of businesses use Repair Manager?
Repair Manager is used by a variety of businesses, including automotive repair shops, appliance stores, electronics retailers, and home improvement stores.
What are jobs related with Repair Manager?
- HVAC Repair Technician
- Marine Motor and Equipment Repair Technician
- Repair Process Technician
- Repair Administrator
- Motorcycle and Power Equipment Repair Technician
- Small Engine Repair Technician
- Repair Specialist
- Automotive Paint and Body Repair Technician
- Repair Technician Lead
- Plumbing Repair Technician
Web Resources
- Pathway | Repair Shop Manager | Victor Valley College www.vvc.edu
- Repair and Maintenance | Central Washington University www.cwu.edu
- What Is an Automotive Service Manager? | UTI www.uti.edu
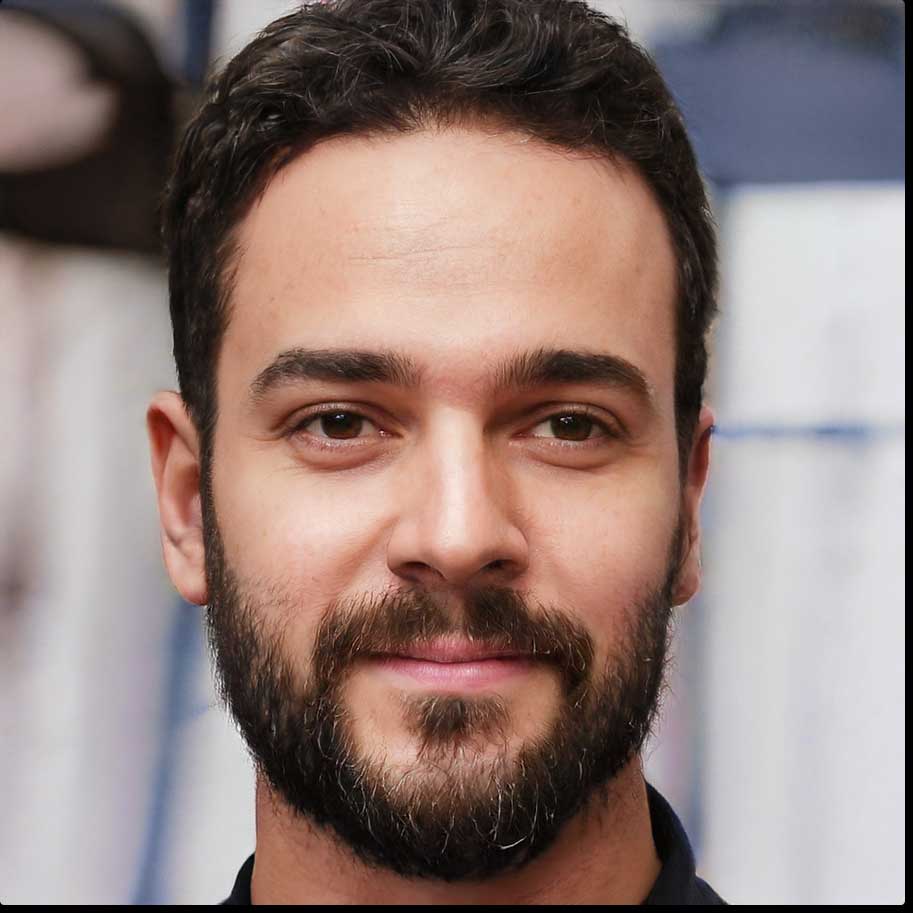