How to Be Quality Control Supervisor - Job Description, Skills, and Interview Questions
Poor quality control can have a serious effect on businesses, resulting in lost profits, dissatisfied customers, and a damaged reputation. To prevent this, it is essential for companies to have a Quality Control Supervisor in place. The Quality Control Supervisor is responsible for monitoring the process of creating products, ensuring that all products meet the highest quality standards.
With their guidance and expertise, they can ensure that all products are correctly manufactured and meet customer expectations. Furthermore, the Quality Control Supervisor is also responsible for monitoring the production process and providing feedback to the production team. This feedback helps the production team to improve efficiency and effectiveness and makes sure that products are consistently produced with the highest quality standards.
By having a Quality Control Supervisor in place, companies can significantly reduce the risk of producing poor quality products and ensure that customers receive superior quality products.
Steps How to Become
- Earn a Bachelor's Degree. Quality control supervisors should possess a bachelor's degree in engineering, business administration or a related field. A few positions may only require an associate's degree.
- Obtain Relevant Work Experience. Quality control supervisors often need to have several years of experience in quality control positions, such as an inspector or analyst. This experience will help supervisors understand the roles and responsibilities of the workers they will be supervising.
- Gain Leadership Experience. Quality control supervisors must be able to motivate and direct workers, so any experience in leadership positions should be highlighted on a resume.
- Develop Interpersonal Skills. Quality control supervisors should be able to communicate effectively with other supervisors, workers and customers. They must also be able to recognize and resolve conflicts in the workplace.
- Acquire Certification. Some employers may require supervisors to have certification from a professional organization, such as the American Society for Quality. Certification can demonstrate a supervisor's knowledge of the industry and commitment to excellence.
The key to staying ahead and qualified as a Quality Control Supervisor is to stay up-to-date on the latest industry standards, trends, and technologies. Investing in continuing education is a great way to stay ahead of the competition and ensure that your skills remain relevant. Keeping up with industry changes can be done by attending workshops and seminars, reading industry news and publications, and networking with other professionals.
taking online courses and participating in online discussion forums can be beneficial in expanding knowledge and keeping current. By staying informed and continually learning, Quality Control Supervisors can remain confident in their abilities and stay ahead of the curve.
You may want to check Inventory Control Associate, Water Control Technician, and Traffic Control Officer for alternative.
Job Description
- Develop and implement quality control systems and processes to ensure product quality.
- Monitor and analyze product performance and customer feedback.
- Develop and maintain quality standards and test procedures.
- Lead root cause analysis of customer complaints, non-conformance issues, and process defects.
- Prepare and initiate corrective and preventive actions.
- Ensure all products meet established quality standards.
- Inspect incoming and outgoing materials for compliance to specifications.
- Train production staff on quality control policies and procedures.
- Monitor and track the implementation of quality systems and procedures.
- Maintain all relevant documentation, such as quality records, reports, logs, etc.
- Liaise with suppliers to ensure the quality of raw materials used in production.
- Collaborate with other departments to ensure the quality of finished products.
- Prepare and deliver quality control reports to management.
- Suggest improvements to production processes and QC systems.
- Ensure compliance with applicable regulations and industry standards.
Skills and Competencies to Have
- Knowledge of quality control principles and techniques
- Ability to inspect and evaluate product quality
- Knowledge of relevant government regulations and standards
- Ability to identify problems and use problem-solving skills
- Ability to plan, organize, and prioritize workloads
- Excellent communication and interpersonal skills
- Attention to detail and accuracy
- Ability to lead a team and delegate responsibilities
- Computer literate with experience in Microsoft Office applications
- Ability to read and interpret technical documents
Effective communication is a key skill for any Quality Control Supervisor. In order to ensure that all quality standards are met in a timely manner, supervisors need to be able to clearly explain quality guidelines and expectations to their team members. By providing clear instructions and feedback, supervisors can help their team members to understand what is expected of them and how to properly complete their tasks.
strong communication skills will allow supervisors to properly assess the progress of their team and identify any areas that need improvement. This, in turn, helps ensure that quality control standards are met and that product consistency is maintained. Furthermore, effective communication also helps build trust and camaraderie amongst team members, which leads to an overall better working environment and improved team performance.
Process Control Engineer, Inventory Control Clerk, and Document Control Coordinator are related jobs you may like.
Frequent Interview Questions
- What experience do you have in quality control and assurance?
- Describe a time where you encountered a challenge in quality control and how you overcame it.
- How would you go about developing and implementing quality control policies and procedures?
- What techniques do you use to measure and evaluate quality performance?
- How do you motivate your team to stay focused on quality control goals?
- What experience do you have with process improvement initiatives?
- What experience do you have with data analysis to identify trends and anomalies in quality performance?
- How do you ensure consistency in quality control across multiple production lines?
- How do you keep up with the latest advancements in quality control technology?
- How do you handle customer complaints related to product quality?
Common Tools in Industry
- Quality Assurance Software. This software helps Quality Control Supervisors to manage, track and report on a variety of quality control processes, such as inspecting products and identifying problems. (eg. X-Ray inspection software)
- Statistical Process Control software. This software helps Quality Control Supervisors to detect and analyze outliers in a process, identify sources of variation and monitor process performance. (eg. Six Sigma software)
- Document Control Software. This software helps Quality Control Supervisors to organize, store, and track documents related to quality control processes. (eg. Electronic Document Management System)
- Quality Checklists. These checklists are used to ensure that quality control processes are followed correctly, and that any problems are identified and addressed. (eg. ISO 9000 compliance checklist)
- Quality Auditing Software. This software helps Quality Control Supervisors to audit processes to ensure that standard operating procedures are being followed and that any potential problems are identified and addressed. (eg. Lean Six Sigma auditing software)
Professional Organizations to Know
- American Society for Quality (ASQ)
- Institute for Supply Management (ISM)
- International Quality Federation (IQF)
- American Production and Inventory Control Society (APICS)
- Institute of Industrial and Systems Engineers (IISE)
- Association for Manufacturing Excellence (AME)
- International Organization for Standardization (ISO)
- National Association of Quality Assurance Professionals (NAQAP)
- Global Association for Quality Management (GAQM)
- International Association for Six Sigma Certification (IASSC)
We also have Inventory Control Manager, Environmental Control Officer, and Security Control Officer jobs reports.
Common Important Terms
- Quality Assurance (QA). A set of activities performed to ensure that a product or service meets the requirements and specifications intended by the customer or user.
- Quality Control (QC). The process of inspection and testing performed to ensure that a product or service meets the required standards of quality.
- Process Improvement. The actions taken to improve the efficiency or effectiveness of a process, usually through changes to the process, procedures, or tools.
- Root Cause Analysis (RCA). A method used to identify and address the underlying causes of a problem in order to prevent similar problems from occurring in the future.
- Auditing. A systematic review of a process or product to ensure compliance with applicable standards and regulations.
- Non-conformance. An instance where a product or service does not meet the required specifications or standards.
- Corrective Action. Actions taken to address non-conformance and prevent similar occurrences in the future.
Frequently Asked Questions
What is the primary responsibility of a Quality Control Supervisor?
The primary responsibility of a Quality Control Supervisor is to oversee quality control operations and ensure compliance with quality assurance standards.
What qualifications are needed for a Quality Control Supervisor position?
Qualifications for a Quality Control Supervisor position typically include a bachelor's degree in engineering, quality assurance, or a related field, along with at least 5 years of experience in a quality assurance or control role.
What are the key performance indicators for a Quality Control Supervisor?
Key performance indicators for a Quality Control Supervisor include the accuracy and efficiency of quality control processes, the number of defects identified and corrected, and customer satisfaction with the quality of products.
What metrics should be tracked to measure the effectiveness of a Quality Control Supervisor?
To measure the effectiveness of a Quality Control Supervisor, metrics such as on-time delivery, failure rates, and customer feedback should be tracked.
What is the average salary for a Quality Control Supervisor?
The average salary for a Quality Control Supervisor is $58,000 per year, according to PayScale.com.
What are jobs related with Quality Control Supervisor?
- Cost Control Analyst
- Traffic Control Supervisor
- Production Control Analyst
- Cost Control Manager
- Traffic Control Technician
- Process Control Coordinator
- Control Systems Technician
- Process Control Inspector
Web Resources
- Quality Control Manager | NC State Online and Distance Education online-distance.ncsu.edu
- Quality Assurance Supervisor | NC State Online and Distance ¦ online-distance.ncsu.edu
- Quality Control Northwestern State University - nsula.edu www.nsula.edu
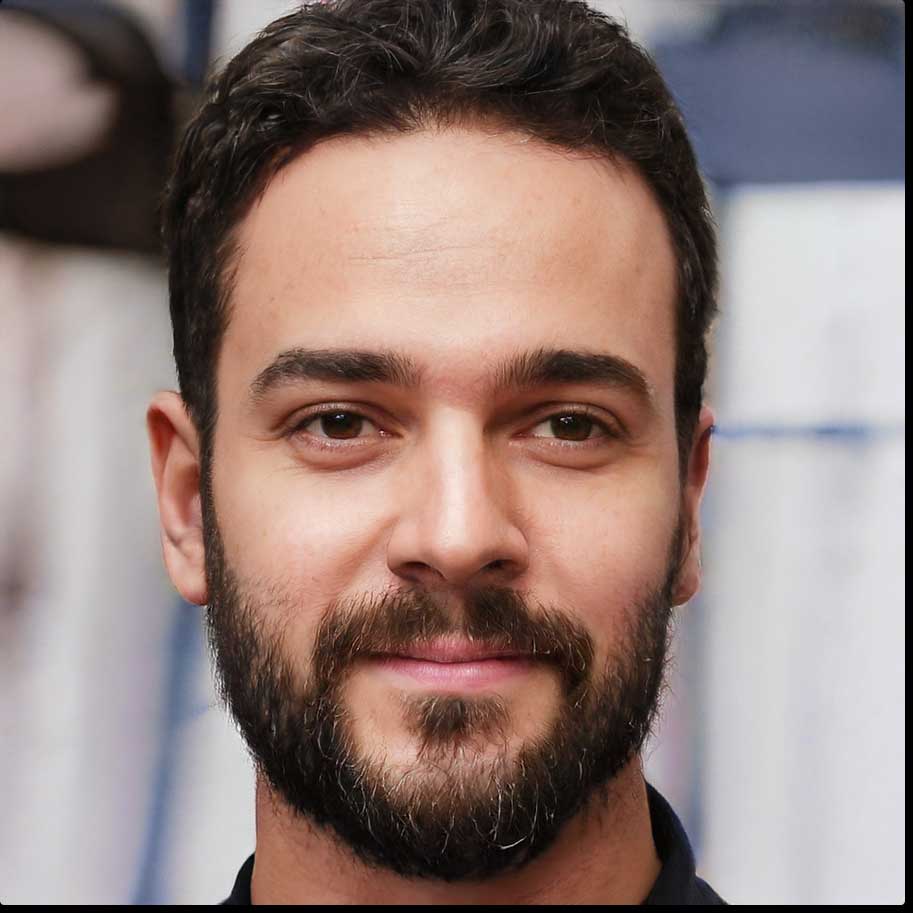