How to Be Process Control Coordinator - Job Description, Skills, and Interview Questions
Poor process control can lead to a variety of negative outcomes, such as decreased production efficiency, higher production costs, and reduced quality assurance. A Process Control Coordinator is a critical role in the production process, ensuring that the right processes are in place and that they are correctly executed. They are responsible for planning, scheduling and monitoring the progress of production processes, as well as analyzing and optimizing their performance.
They also provide feedback to management teams on process performance and suggest improvements where needed. With the right Process Control Coordinator in place, companies can increase their efficiency, reduce costs, and ensure quality assurance.
Steps How to Become
- Earn a Bachelor's Degree. To become a Process Control Coordinator, you will first need to earn a Bachelor's degree in a relevant field. This could include engineering, computer science, or industrial technology.
- Gain Relevant Work Experience. It is important to gain relevant work experience before becoming a Process Control Coordinator. You can do this by working as an intern or even as a volunteer in a related field.
- Develop Knowledge and Skills. You will need to develop knowledge and skills related to process control. This includes learning about automation systems, software, and control systems.
- Obtain Certification. Obtaining certification in a related field can be beneficial for your career prospects. This could include becoming certified in Programmable Logic Controllers (PLCs) or industrial control systems.
- Apply for Jobs. Once you have the necessary qualifications and experience, you can start applying for jobs as a Process Control Coordinator. You can search for job openings online or in your local area.
- Continue to Learn and Grow. Once you have secured a job as a Process Control Coordinator, it is important to continue to learn and grow in your field. This could include attending trainings or seminars, reading industry-related publications, or joining professional associations.
The role of a Process Control Coordinator is essential for ensuring reliable and capable operations within a company. As the coordinator, one is responsible for the overall control and management of the process, from defining the requirements for process control to monitoring the performance of the system. To be successful in this role, it is important to have a comprehensive knowledge of the process and its related components.
This includes understanding how the process works and what factors can impact its performance. A Process Control Coordinator also needs to be able to identify potential problems before they arise, so they can be addressed quickly and efficiently. Furthermore, they must be able to establish and monitor effective communication between all parties involved in the process.
By doing so, they can ensure that all areas of the process are operating as expected and that any issues are resolved in a timely manner. the Process Control Coordinator is critical for a company to maintain reliable and capable operations.
You may want to check Process Control Engineer, Control Systems Technician, and Quality Control Supervisor for alternative.
Job Description
- Develop and implement process control strategies to meet the production goals of the organization.
- Monitor and analyze process performance and make necessary adjustments to ensure operational efficiency.
- Diagnose and troubleshoot process issues and recommend corrective actions to improve process results.
- Create and maintain process documentation, including flowcharts, standard operating procedures, and training materials.
- Coordinate with other departments for process improvement initiatives.
- Develop and manage process control-related budgets, including capital expenditures and labor resources.
- Gather, analyze, and report process performance data.
- Provide technical direction and support to team members on process-related topics.
- Analyze process control data to identify trends and develop strategies to optimize process performance.
- Identify potential process improvement opportunities and lead the development of new processes or systems.
Skills and Competencies to Have
- Knowledge of process control systems, automation, and operations
- Expertise in instrumentation and control systems
- Understanding of regulatory requirements related to process control
- Ability to maintain process control system documentation
- Proficiency in troubleshooting process control issues
- Excellent communication skills
- Strong analytical and problem-solving abilities
- Capacity to work independently with minimal supervision
- Good organizational and time management skills
- Working knowledge of industry-related software programs
- Ability to collaborate with stakeholders
- Ability to work in a team environment
- Familiarity with safety protocols and procedures
The ability to effectively coordinate process control is an essential skill for any successful production operation. Good process control management involves the efficient and effective coordination of multiple related entities, including personnel, resources, processes, and equipment. Process control coordinators must possess strong problem-solving and communication skills to ensure the efficient functioning of all related entities.
They must also be able to identify potential risks and develop strategies to minimize them, as well as coordinate the actions of all related personnel. process control coordinators must possess excellent organizational and interpersonal skills in order to properly manage the various activities involved in the production process. Without these important skills, a production operation can suffer from decreased efficiency, increased costs, and other detrimental effects.
Environmental Control Officer, Control Technician, and Traffic Control Officer are related jobs you may like.
Frequent Interview Questions
- What experience do you have with process control systems and software?
- How have you successfully implemented process control strategies in the past?
- What challenges have you faced in coordinating process control systems?
- How would you handle an unexpected issue with the process control system?
- Describe a process control system improvement you have implemented in the past.
- How have you used data to identify and solve process control problems?
- What do you think are the most important characteristics of a successful process control coordinator?
- What methods have you used to ensure accuracy and consistency in process control systems?
- How would you manage multiple process control projects simultaneously?
- What safety measures do you take when managing process control systems?
Common Tools in Industry
- Process Mapping Software. Used to create diagrams of process flow. (eg: Visio)
- Process Automation Tools. Used to automate the execution of processes, such as scheduling tasks or sending emails. (eg: Microsoft Flow)
- Process Simulation Software. Used to simulate and analyze processes to improve efficiency. (eg: Witness)
- Process Monitoring Software. Used to track and monitor process performance, such as time and cost. (eg: Control Chart)
- Process Documentation Software. Used to create and store process documents and instructions. (eg: Process Street)
- Process Auditing Tools. Used to audit and review processes to ensure compliance and quality. (eg: Process Control)
- Process Improvement Software. Used to identify and implement process improvements. (eg: Lean Six Sigma)
Professional Organizations to Know
- International Society for Automation (ISA)
- Association for Process Control Professionals (APCP)
- American Society for Quality (ASQ)
- Instrumentation, Systems, and Automation Society (ISA)
- International Federation of Automatic Control (IFAC)
- International Council of Systems Engineers (INCOSE)
- Society of Manufacturing Engineers (SME)
- Institute of Industrial and Systems Engineers (IISE)
- Project Management Institute (PMI)
- American Society of Mechanical Engineers (ASME)
We also have Inventory Control Associate, Cost Control Analyst, and Process Control Inspector jobs reports.
Common Important Terms
- Process Analysis. The process of analyzing a given process to identify potential improvements or changes that would be beneficial.
- Process Improvement. The process of making a given process more efficient, effective, or reliable.
- Standard Operating Procedures (SOPs). A set of directions, rules, or guidelines that are established to ensure a consistent and orderly operation of a given process.
- Quality Control. The process of ensuring that products, services, and processes meet pre-determined standards.
- Risk Management. The process of identifying, assessing, and managing potential risks within a process or system.
- Documentation. The process of creating and maintaining records of a given process or system.
- Scheduling. The process of planning and organizing tasks to ensure the timely execution of a given process or system.
- Training. The process of providing instruction and direction to personnel to ensure they are capable of performing their duties properly and effectively.
Frequently Asked Questions
What is a Process Control Coordinator?
A Process Control Coordinator is a position responsible for the planning, coordination, and implementation of process control systems across an organization. This includes working with internal teams and external vendors to ensure that all process control systems are operating efficiently and in compliance with applicable regulations.
What responsibilities do Process Control Coordinators have?
Process Control Coordinators are responsible for overseeing the installation, maintenance, and operation of process control systems. This includes ensuring that all components of the system are operating correctly, troubleshooting any issues that arise, and providing technical support for users. They also develop and implement procedures for monitoring system performance and diagnosing malfunctions.
What qualifications are required for a Process Control Coordinator?
The qualifications required for a Process Control Coordinator typically include a Bachelors degree in engineering, computer science, or a related field, as well as extensive experience with process control systems. Strong communication, problem-solving, and organizational skills are also important for this position.
How does a Process Control Coordinator ensure that systems are compliant with regulations?
Process Control Coordinators are responsible for ensuring that all process control systems are compliant with applicable regulations. This involves researching applicable laws and regulations and developing procedures to ensure that all systems meet the necessary requirements. They also keep up to date with changes in regulations and implement any necessary changes to the system.
What are the benefits of having a Process Control Coordinator?
Having a Process Control Coordinator on staff ensures that process control systems run smoothly and efficiently and remain compliant with applicable regulations. This reduces the risk of costly errors or regulatory violations, and helps the organization save time and money by avoiding costly repairs or shutdowns due to malfunctions.
What are jobs related with Process Control Coordinator?
- Security Control Officer
- Cost Control Manager
- Inventory Control Clerk
- Water Control Technician
- Production Control Analyst
- Traffic Control Technician
- Traffic Control Supervisor
- Inventory Control Manager
Web Resources
- Process Coordinator | IT@Cornell it.cornell.edu
- Control of Processes Visual Encyclopedia of Chemical encyclopedia.che.engin.umich.edu
- (PDF) Statistical Process Control Manual - Academia.edu www.academia.edu
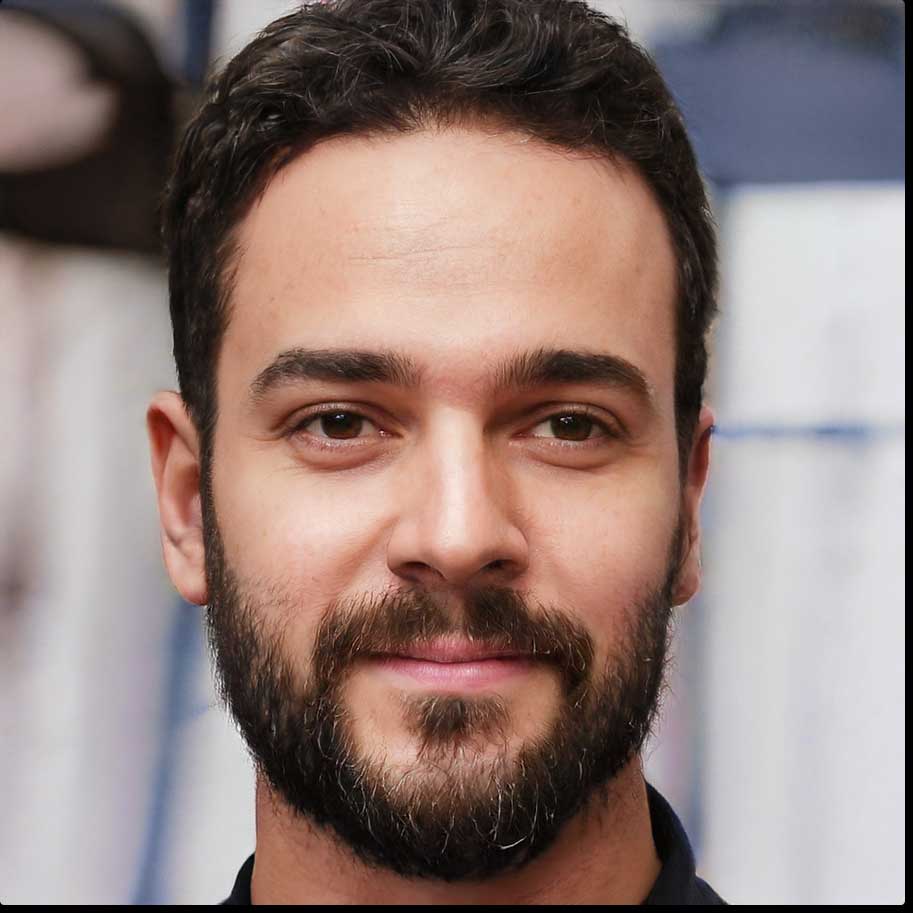