How to Be Quality Consultant - Job Description, Skills, and Interview Questions
The lack of quality control in a business can have grave consequences. Poorly made products can lead to customer dissatisfaction, which can result in decreased sales and a tarnished reputation. if the process is not monitored carefully, it can result in financial losses due to the need for refunds and replacements.
In order to properly maintain quality, businesses must invest in knowledgeable quality consultants who can inspect products and processes and develop strategies to ensure that quality standards are met. Quality consultants are essential to the success of any business, as they can help to ensure customer satisfaction and build trust with consumers.
Steps How to Become
- Obtain a Bachelor's Degree. The first step to becoming a quality consultant is to earn a bachelor's degree in a related field, such as industrial engineering, industrial quality management or quality assurance.
- Acquire Work Experience. It is important for aspiring quality consultants to gain some relevant work experience. Working in a quality control or quality assurance role in a manufacturing or production environment can provide the necessary experience and knowledge to be successful in the consulting role.
- Consider Certification. Quality consultants may choose to pursue certification as a way to demonstrate their expertise. Certification can also be helpful when applying for jobs or consulting opportunities.
- Develop a Network. Quality consultants need to develop a network of contacts in the industry in order to be successful. Networking with other professionals and attending industry events can be helpful in finding job opportunities and gaining new clients.
- Stay Up-to-Date. It is important for quality consultants to stay up-to-date on emerging trends and technologies in the industry. This can be done through reading industry publications, attending conferences and seminars, and engaging in online forums and discussions.
The quality of a product or service is determined by its level of efficiency, reliability, and usability. To keep up with the ever-changing market, companies must stay updated with the latest trends and technologies. One way to ensure that a company remains efficient is to invest in quality consulting services.
Quality consultants can provide valuable insights into the latest industry standards, identify areas of improvement, and suggest strategies to increase productivity and efficiency. By implementing quality assurance plans, companies can reduce costs, improve customer satisfaction, and increase profitability. by investing in quality consulting services, companies can gain access to resources and training, allowing them to stay up-to-date with the latest trends and technologies.
You may want to check IT Consultant, Organizational Development Consultant, and Project Management Consultant for alternative.
Job Description
- Quality Assurance Consultant: Responsible for developing and implementing quality assurance processes and procedures to ensure high standards of product quality.
- Quality Management Consultant: Responsible for designing and implementing quality management systems and strategies to improve the overall quality of products and services.
- Quality Improvement Consultant: Responsible for identifying opportunities to improve quality, developing strategies and plans to address these issues, and monitoring progress to ensure successful implementation.
- Quality Control Consultant: Responsible for performing inspections, testing, and analysis of products to ensure that they meet specified standards of quality.
- Quality Auditing Consultant: Responsible for auditing the quality management system and processes to identify any gaps or areas of improvement.
- Quality Standards Consultant: Responsible for developing and maintaining quality standards and criteria for products, services, and processes.
Skills and Competencies to Have
- Knowledge of Quality Management Principles
- Knowledge of Quality Assurance and Control Procedures
- Ability to Analyze Data and Create Reports
- Strong Attention to Detail
- Ability to Interpret and Follow Regulations and Standards
- Excellent Communication Skills
- Outstanding Problem-Solving Abilities
- Ability to Develop and Monitor Quality Systems
- Experience with Industry Standards and Specifications
- Strong Interpersonal and Leadership Skills
The ability to think critically is an essential skill for any Quality Consultant. A Quality Consultant must be able to assess a situation, analyze the data, and evaluate the results. By doing so, they can identify problems, come up with solutions, and develop strategies to improve a processes or product.
Critical thinking also helps a Quality Consultant to make informed decisions that are based on facts and evidence, rather than opinions and biases. The ability to think critically can positively impact the quality of a product, as well as the customer experience. Furthermore, it can lead to improved productivity and efficiency, which can ultimately lead to increased profits.
critical thinking is a key component of any successful Quality Consultant role.
Process Improvement Consultant, Legal Consultant, and Risk Consultant are related jobs you may like.
Frequent Interview Questions
- What experience do you have in Quality Consulting?
- What specific quality assurance processes have you implemented in the past?
- How do you ensure that quality standards are met within a project or organization?
- What strategies have you used to ensure customer satisfaction?
- Describe a time when you identified potential problems in a project and how did you address them?
- What challenges have you faced while implementing quality programs and how did you overcome them?
- How do you define and measure the success of quality improvement initiatives?
- What methods do you use to identify root causes of quality issues?
- How would you ensure that a team or organization is compliant with necessary regulations and standards?
- Describe a situation where you had to persuade management to adopt a quality control system.
Common Tools in Industry
- Quality Assurance Tools. These tools help ensure the quality of products and services through testing, validation, and verification. Examples include HP QuickTest Professional, Selenium, and Cucumber.
- Process Improvement Tools. These tools help businesses identify and improve processes to improve efficiency and reduce costs. Examples include Lean Six Sigma, Kaizen, and Agile.
- Risk Management Tools. These tools help identify, quantify, monitor, and manage risks. Examples include RiskRegister, RiskLens, and RiskyProject.
- Quality Metrics Tools. These tools help measure the quality of products and services. Examples include Six Sigma, ISO 9001, and Total Quality Management (TQM).
- Quality Control Tools. These tools help ensure that products and services meet required standards. Examples include Statistical Process Control (SPC), Design of Experiments (DOE), and Failure Mode and Effects Analysis (FMEA).
Professional Organizations to Know
- American Society for Quality (ASQ)
- International Organization for Standardization (ISO)
- Project Management Institute (PMI)
- Institute of Quality Assurance (IQA)
- American Productivity & Quality Center (APQC)
- International Association for Six Sigma Certification (IASSC)
- Association for Quality and Participation (AQP)
- Association for Quality and Performance Excellence (AQPE)
- Malcolm Baldrige National Quality Award (MBNQA)
- International Institute of Business Analysis (IIBA)
We also have Management Consultant, Data Consultant, and Consultancy Services Manager jobs reports.
Common Important Terms
- Quality Assurance. A systematic approach to planning, implementing and evaluating activities to ensure quality standards are met.
- Quality Control. The process of ensuring the quality of a product or service is maintained at a desired level.
- Quality Management System. A set of policies and procedures developed to ensure that products and services meet the highest quality standards.
- Quality Improvement. The process of continually striving to improve the quality of products, services, and processes.
- ISO 9001. The international standard for quality management systems, which provides a framework for businesses to achieve consistent, high-quality performance.
- Six Sigma. A business strategy aimed at reducing variability and eliminating defects in products and services.
- Kaizen. A Japanese term meaning continuous improvement, Kaizen is a business philosophy focused on making small, incremental changes to improve efficiency and productivity.
Frequently Asked Questions
What qualifications are needed to become a Quality Consultant?
Generally, Quality Consultants need a minimum of a bachelors degree in a related field such as business, engineering, or quality management. Additionally, certifications in Six Sigma, Lean Manufacturing, or Quality Management Systems may be beneficial.
What are the major responsibilities of a Quality Consultant?
Quality Consultants are responsible for developing, implementing, and maintaining quality management systems and processes. They may analyze customer requirements and data to identify areas for improvement, develop corrective and preventive actions, and evaluate the effectiveness of changes to the systems.
How much does a Quality Consultant typically earn?
According to PayScale, the median annual salary for Quality Consultants is $70,945. The salary range typically falls between $62,271 and $83,552.
What skills are important for Quality Consultants?
Quality Consultants should have strong problem-solving and analytical skills, as well as excellent communication and interpersonal skills. They need to be able to identify trends and root causes of quality issues and be comfortable with data analysis and report writing.
What industries hire Quality Consultants?
Quality Consultants are employed in a variety of industries including aerospace, automotive, construction, and manufacturing. They may also work in healthcare, finance, and professional services.
What are jobs related with Quality Consultant?
Web Resources
- What is a Quality Consultant? - Goodwin University www.goodwin.edu
- Edu Quality Consultants India, Indore - Service Provider of ISO ... www.indiamart.com
- Quality Services | UT Center for Industrial Services www.cis.tennessee.edu
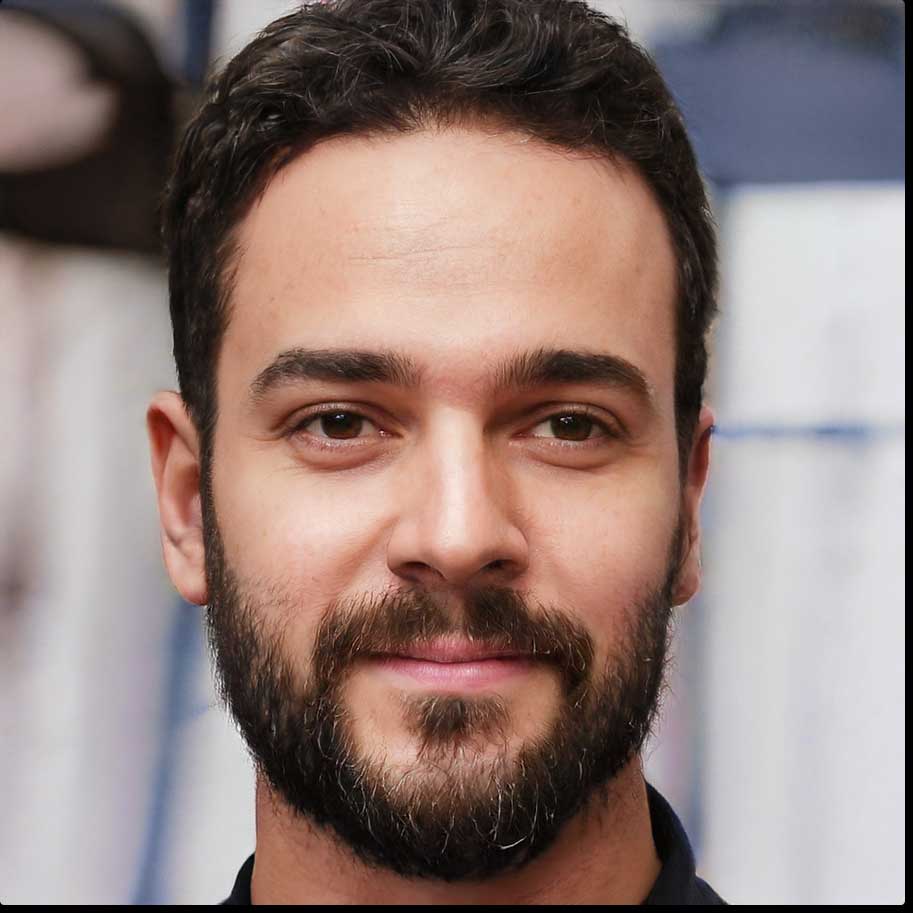