How to Be Process Improvement Consultant - Job Description, Skills, and Interview Questions
Steps How to Become
- Earn a Bachelor's Degree. The first step to becoming a process improvement consultant is to earn a bachelor's degree in a related field, such as business administration, industrial engineering, or operations management. This will provide you with the necessary skills and knowledge to understand the fundamentals of process improvement.
- Gain Work Experience. After graduating from college, it is important to gain work experience in the field of process improvement. Working in an entry-level position in a related field can provide valuable insight into the process improvement industry.
- Get Certified. To become a process improvement consultant, it is essential to obtain certifications from industry-recognized organizations. The American Society for Quality (ASQ) and International Quality Federation (IQF) both offer certifications that demonstrate proficiency in process improvement techniques.
- Become an Expert. As a process improvement consultant, it is important to stay up-to-date on the latest trends and techniques in the field. Consider taking additional courses and attending industry conferences to stay ahead of the curve.
- Create a Network. Building relationships with other process improvement professionals can be beneficial for staying informed on the latest industry trends and for finding potential consulting opportunities. Consider joining professional organizations, such as the Association for Quality (AQ) and International Association for Six Sigma Certification (IASSC).
- Market Yourself. Promoting yourself as a process improvement consultant is essential for finding consulting opportunities. Consider creating a website, developing marketing materials, and leveraging social media platforms to reach potential clients.
Maintaining competency and staying up to date as a Process Improvement Consultant is essential in order to effectively advise businesses on how to improve their operations. To do this, it is important to stay abreast of the latest industry trends, technological advances, and best practice standards. Staying informed requires regular reading of industry publications, attending conferences to discuss new developments and networking with colleagues, which can be accomplished through joining professional associations or online forums.
individuals should continually develop their skillset, by taking courses and certifications that can help them become more knowledgeable in their field. Taking the time to invest in oneself will not only help keep one's skills sharp but also demonstrate a commitment to professional development and help one stand out from the competition.
You may want to check Data Consultant, Quality Consultant, and Management Consultant for alternative.
Job Description
- Analyze existing business processes and recommend areas of improvement
- Develop and implement process improvement plans
- Identify opportunities to reduce costs, increase efficiencies, and improve customer service
- Create metrics and dashboards to measure process performance
- Facilitate meetings with stakeholders to discuss process improvement initiatives
- Leverage process engineering tools and techniques (such as Lean Six Sigma) to optimize existing processes
- Develop training materials and provide guidance on process improvement best practices
- Develop and maintain relationships with internal and external stakeholders
- Conduct process reviews and audits to ensure compliance with established standards
- Present process improvement plans to stakeholders for acceptance and implementation
Skills and Competencies to Have
- Analytical and Problem Solving Skills
- Strategic Thinking
- Project Management
- Change Management
- Communication and Presentation Skills
- Consulting Skills
- Relationship Building
- Business Acumen
- Process Mapping
- Quality Assurance Methodologies
- Data Analysis and Reporting
- Facilitation and Training
- Process Engineering
- Six Sigma Certification
- Lean Manufacturing Principles
Having strong problem-solving skills is essential for a Process Improvement Consultant. Knowing how to effectively analyze data, identify and prioritize problems, develop and implement solutions, and measure the impact of changes are all key components for making improvements to a process. By being able to effectively communicate with stakeholders, a Process Improvement Consultant can also ensure that the process changes are understood and accepted by all parties involved.
having strong interpersonal skills is important in order to build relationships and trust with the stakeholders, which will lead to more successful process improvements. All these skills are essential for a Process Improvement Consultant in order to be successful in their role.
IT Consultant, Risk Consultant, and Consultancy Services Manager are related jobs you may like.
Frequent Interview Questions
- What experience do you have in process improvement consulting?
- What is your understanding of the current state of process improvement in our industry?
- What methods do you use to analyze existing processes and identify areas of improvement?
- How do you go about creating a plan for implementing process improvements?
- How do you ensure that improvements to processes are sustainable and well-maintained?
- Describe a successful process improvement project you have led or contributed to in the past.
- What techniques do you use to engage stakeholders in the process improvement process?
- How do you handle resistance from stakeholders when implementing process improvements?
- How do you measure the success of a process improvement project?
- What is your approach to problem solving when faced with complex challenges related to process improvement?
Common Tools in Industry
- Lean Six Sigma. Lean Six Sigma is a methodology used to improve processes and eliminate waste. It is used to identify and remove the causes of defects and minimize variations in business processes. (eg: A Lean Six Sigma consultant may help a business reduce lead time on a product by streamlining production processes).
- Process Mapping. Process Mapping is a visual tool used to document processes, identify process improvement opportunities, and track changes over time. (eg: A Process Improvement Consultant may use process mapping to identify areas of inefficiency in an existing process).
- Statistical Analysis. Statistical Analysis is a tool used to analyze data and identify trends. It can be used to determine the cause of variation and make predictions about future performance. (eg: A Process Improvement Consultant may use statistical analysis to determine the root cause of quality issues in a manufacturing process).
- Root Cause Analysis. Root Cause Analysis is a structured problem-solving process used to identify the underlying cause of a problem. It is used to identify the root cause of an issue and develop solutions that prevent it from happening in the future. (eg: A Process Improvement Consultant may use Root Cause Analysis to identify the cause of customer complaints about a service).
- Business Process Reengineering. Business Process Reengineering (BPR) is a methodology used to redesign processes in order to achieve significant improvements in performance. (eg: A Process Improvement Consultant may use BPR to redesign an inefficient process in order to save time and resources).
Professional Organizations to Know
- Association for Process Improvement (ASPI)
- Project Management Institute (PMI)
- International Association for Six Sigma Certification (IASSC)
- Lean Enterprise Institute (LEI)
- Institute of Industrial and Systems Engineers (IISE)
- Institute of Management Consultants USA (IMC USA)
- International Association for Management Consulting (IAMC)
- American Quality Association (AQA)
- Society for Organizational Learning (SOL)
- National Association of Professional Process Improvement Consultants (NAPPC)
We also have Legal Consultant, Marketing Consultant, and Project Management Consultant jobs reports.
Common Important Terms
- Process Analysis. The process of studying and evaluating existing processes to identify areas of improvement, with the goal of streamlining operations and improving efficiency.
- Process Mapping. The process of visually documenting a process flow by using symbols and arrows to represent each step or activity.
- Root Cause Analysis. A problem-solving technique used to identify the underlying cause of an issue or problem.
- Lean Six Sigma. A business management strategy that combines two approacheslean manufacturing and Six Sigmato reduce waste and inefficiency in business processes.
- Business Process Reengineering. The process of examining existing processes within an organization and redesigning them to increase efficiency and effectiveness.
- Quality Management. A systematic approach to managing the quality of products or services by controlling processes, improving customer satisfaction, and reducing costs.
- Quality Assurance. A process used to ensure that products or services meet established quality standards before they are released.
Frequently Asked Questions
What is a Process Improvement Consultant?
A Process Improvement Consultant is a professional who specializes in helping organizations improve their operations, processes and systems. They can provide analysis and guidance on how to increase efficiency and effectiveness, as well as identify areas of opportunity for cost savings and improved customer satisfaction.
What skills are required of a Process Improvement Consultant?
Process Improvement Consultants should have strong analytical and problem-solving skills, as well as an understanding of best practices in process improvement and quality assurance. In addition, they need to have excellent communication and organizational skills, be able to work collaboratively with team members, and have a deep understanding of the business processes and systems.
What type of qualifications do Process Improvement Consultants need?
Process Improvement Consultants should possess a bachelor's degree in business, engineering, or a related field. In addition, they should have experience in process improvement, quality assurance, and/or business analysis, as well as certifications such as Six Sigma or Lean.
What are the benefits of hiring a Process Improvement Consultant?
By working with a Process Improvement Consultant, organizations can benefit from improved efficiency, cost savings, and customer satisfaction. In addition, consultants can provide valuable insight into the organization's operations and processes, helping to identify areas for improvement and opportunities for growth.
How long does a typical engagement with a Process Improvement Consultant last?
The length of engagements with Process Improvement Consultants vary depending on the scope of the project and the desired outcomes. Engagements can last anywhere from a few months to over a year.
What are jobs related with Process Improvement Consultant?
Web Resources
- Advisory Services Process Improvement Consultant careers.kelley.iu.edu
- Process Improvement Services | Business Process Management ¦ bpm.berkeley.edu
- Process Improvement - Workforce - Sinclair workforce.sinclair.edu
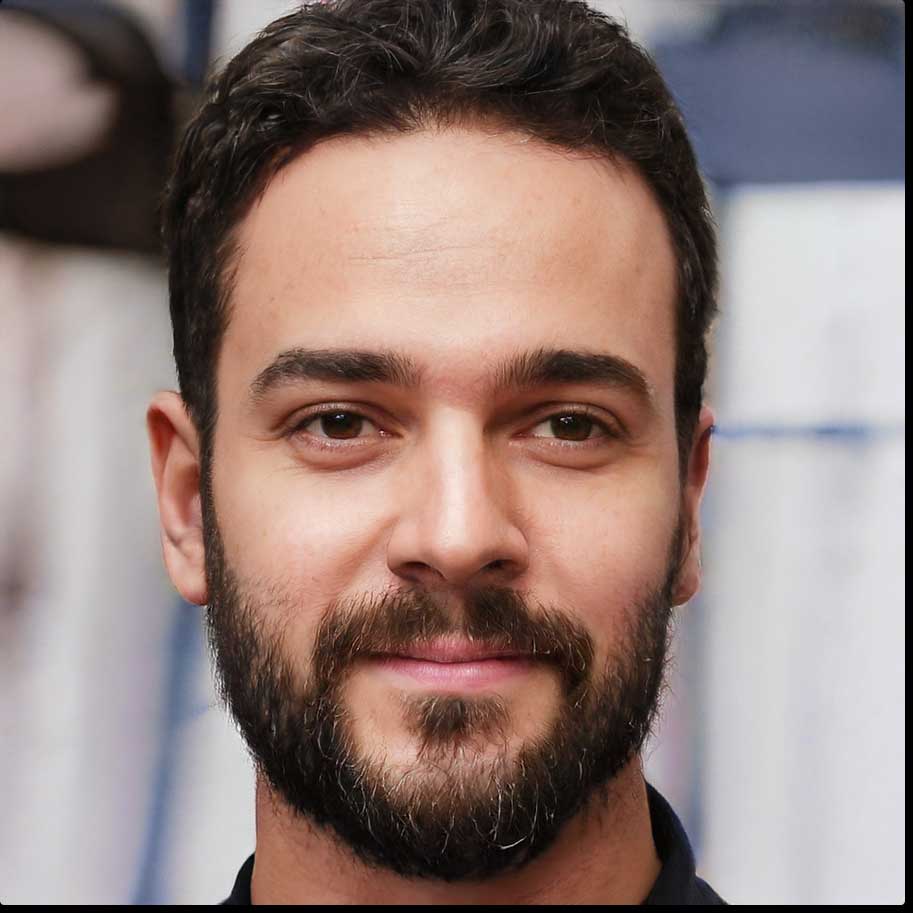