How to Be Process Improvement Strategist - Job Description, Skills, and Interview Questions
The implementation of quality improvement strategies has proven to be an effective tool in driving greater efficiency, improved customer satisfaction, and increased profitability. When organizations invest in process improvement methods, they gain better insight into their operations, enabling them to identify and address problems more quickly and effectively. This often leads to the development of more efficient systems and processes, which can reduce costs and improve customer service.
process improvement initiatives can also result in improved employee morale and productivity, as employees become more confident in their ability to do their jobs and are motivated to work more efficiently. Thus, the process improvement strategy is a key factor in helping businesses to remain competitive in today's market and achieve greater success.
Steps How to Become
- Earn a Bachelor's Degree. To become a Process Improvement Strategist, you'll need to have at least a bachelor's degree in a field such as business administration, operations management, or industrial engineering.
- Gain Work Experience. After completing your degree, it's important to gain experience in the field. This could include internships or entry-level positions in business operations, process improvement, quality control, or project management.
- Obtain Professional Certification. Professional certifications can help demonstrate a commitment to the profession and give you the edge when competing for jobs. Certifications such as Lean Six Sigma Green Belt or Black Belt are highly sought after.
- Develop Leadership and Communication Skills. As a Process Improvement Strategist, you'll need strong communication and leadership skills to be successful. Take courses or workshops to develop your management and problem-solving skills.
- Network with Professionals. A great way to learn more about the profession and find job opportunities is to network with other professionals in the field. Attend conferences and events, join professional organizations, and read industry publications.
- Apply for Jobs. Once you have the necessary qualifications and experience, you can start applying for jobs as a Process Improvement Strategist. Look for positions at consulting firms, technology companies, manufacturing companies, and more.
The success of an organization relies heavily on the quality of its processes and how efficiently they are carried out. To ensure that these processes are effective, Process Improvement Strategists are essential. They are experts in analyzing current processes and finding ways to improve them.
By identifying inefficiencies and potential opportunities, they are able to provide the organization with practical solutions that will save time, money, and resources. This increased efficiency not only benefits the organization, but also improves customer satisfaction, reduces waste, and increases profits. Therefore, organizations need to make sure they hire skilled and qualified Process Improvement Strategists to maximize their productivity.
You may want to check Financial Strategist, Healthcare Strategist, and Innovation Strategist for alternative.
Job Description
- Process Improvement Manager: Responsible for developing and implementing strategies to streamline and optimize business processes. Analyzes current processes, identifies areas for improvement, designs new processes, and implements changes.
- Process Improvement Consultant: Provides expertise and advice to organizations on process improvement initiatives. Analyzes current processes, identifies areas for improvement, and suggests solutions.
- Process Improvement Analyst: Conducts in-depth research and analysis of current processes and identifies areas for improvement. Designs and tests new processes, and makes recommendations for implementation.
- Process Improvement Engineer: Drives process improvement initiatives by designing and implementing new systems and processes. Identifies areas for improvement, creates plans, and implements changes.
- Process Improvement Project Manager: Manages process improvement initiatives from conception to completion. Identifies opportunities for improvement, develops plans and timelines, and oversees the implementation of changes.
Skills and Competencies to Have
- Project Management
- Process Analysis and Design
- Change Management
- Quality Assurance
- Strategic Planning
- Business Analysis
- Risk Assessment
- Problem Solving
- Continuous Improvement Methodologies
- Data Analysis
- Communication and Interpersonal Skills
- Leadership and Team Building
The ability to think strategically and improve processes is essential for any business to remain successful. A Process Improvement Strategist is the key person responsible for leading the charge to analyze current processes, identify areas of improvement, and implement new strategies that can optimize the efficiency of the organization. This involves working with different stakeholders to understand their needs, analyzing existing data, and finding creative solutions that will increase productivity, reduce costs, and improve customer satisfaction.
To be successful in this role, it is important to have strong problem solving skills, excellent communication and collaboration abilities, and a deep understanding of process optimization principles and best practices. having an in-depth knowledge of the latest trends in technology, process automation, and analytics can help a Process Improvement Strategist stay ahead of the competition.
Business Development Strategist, Creative Strategist, and Corporate Strategist are related jobs you may like.
Frequent Interview Questions
- What experience do you have in process improvement strategy?
- What techniques and tools do you use to analyze and optimize processes?
- Describe a complex process improvement project that you managed from start to finish.
- How do you identify areas for process improvement?
- What strategies do you use to ensure that changes are implemented successfully?
- How do you collaborate with stakeholders to gain consensus for process improvement initiatives?
- What methods do you use to measure the success of process improvement efforts?
- What challenges have you encountered when improving processes and how did you address them?
- How do you stay up-to-date on best practices and industry trends related to process improvement?
- How do you ensure that process improvement projects are completed on time and within budget?
Common Tools in Industry
- Lean Six Sigma. An improvement methodology that combines Lean and Six Sigma philosophies to reduce waste, streamline processes and improve customer satisfaction. (eg: Using Lean Six Sigma to reduce lead time on order fulfillment)
- Kaizen. A continual improvement process that encourages employees to make small, incremental changes to their processes over time. (eg: Using Kaizen to reduce defects in a manufacturing process)
- Process Mapping. The visual representation of a process to understand how different activities interact and identify areas that need improvement. (eg: Mapping customer service processes to improve response times)
- Root Cause Analysis. A structured method used to identify the underlying cause of an issue or problem. (eg: Using Root Cause Analysis to identify why customer complaints are on the rise)
- Quality Circles. A collaborative team approach to identifying, analyzing and solving problems in the workplace. (eg: Establishing Quality Circles to improve productivity)
Professional Organizations to Know
- Association for Process Improvement (A4PI)
- Institute of Industrial and Systems Engineers (IISE)
- International Institute of Business Analysis (IIBA)
- International Quality Federation (IQF)
- American Society for Quality (ASQ)
- International Project Management Association (IPMA)
- International Six Sigma Institute (ISSI)
- Lean Enterprise Institute (LEI)
- National Association of Productivity and Organizing Professionals (NAPO)
- Project Management Institute (PMI)
We also have Sales and Distribution Strategist, Retail Strategist, and Digital Transformation Strategist jobs reports.
Common Important Terms
- Continuous Improvement. A process of ongoing improvement by making small incremental changes and improvements over time.
- Process Mapping. A diagram or flowchart of a business process, showing the sequence of steps and tasks that must be completed to achieve a desired outcome.
- Lean Principles. A set of fundamental principles used to reduce waste and maximize value while improving efficiency in a business process.
- Root Cause Analysis. A systematic process used to identify the underlying causes of a problem and develop solutions to prevent it from occurring again.
- Six Sigma. An organized and structured approach to identify and eliminate defects in a business process.
- Quality Control. A process used to ensure that products, services, or processes meet specific quality standards.
- Process Change Management. A systematic approach to managing the transition from an existing process to a new one.
- Risk Management. A process of identifying and mitigating risks associated with a business process or activity.
Frequently Asked Questions
What is the role of a Process Improvement Strategist?
A Process Improvement Strategist is responsible for identifying opportunities for process optimization within an organization. They analyze existing processes, identify areas of improvement, and design strategies to maximize efficiency and productivity.
What skills are needed to be a Process Improvement Strategist?
Successful Process Improvement Strategists possess strong analytical, problem-solving, and communication skills. They need to be able to identify inefficiencies and develop creative solutions. Additionally, they should have an understanding of relevant software, industry trends, and best practices.
How is process improvement implemented?
Process improvement is usually implemented in steps, starting with an analysis of the current process. A strategist will then develop a plan to optimize the process, which may involve revising existing procedures, introducing new technology, or training staff on improved techniques. The strategist will then monitor the implementation of the new process to ensure that it is effective.
What metrics are used to measure the success of a process improvement strategy?
Metrics that are used to measure the success of a process improvement strategy include time saved, cost savings, increased customer satisfaction, and higher quality output.
What is Kaizen?
Kaizen is a Japanese term for continuous improvement. It is an approach that focuses on making small, incremental changes to processes, rather than trying to make drastic changes all at once. Kaizen is often used in combination with other process improvement strategies such as Lean or Six Sigma.
What are jobs related with Process Improvement Strategist?
- Supply Chain Management Strategist
- Pricing Strategist
- Human Resources Strategist
- Management Consultant Strategist
- Consumer Insights Strategist
- Community Strategist
- Financial Planning and Analysis Strategist
- E-commerce Strategist
- Technology Strategist
- Media Strategist
Web Resources
- Strategic Planning and Process Improvement commed.umassmed.edu
- Process Improvement | Emory University | Atlanta GA sot.emory.edu
- Process Improvement | Corporate Training and Professional corporatetraining.usf.edu
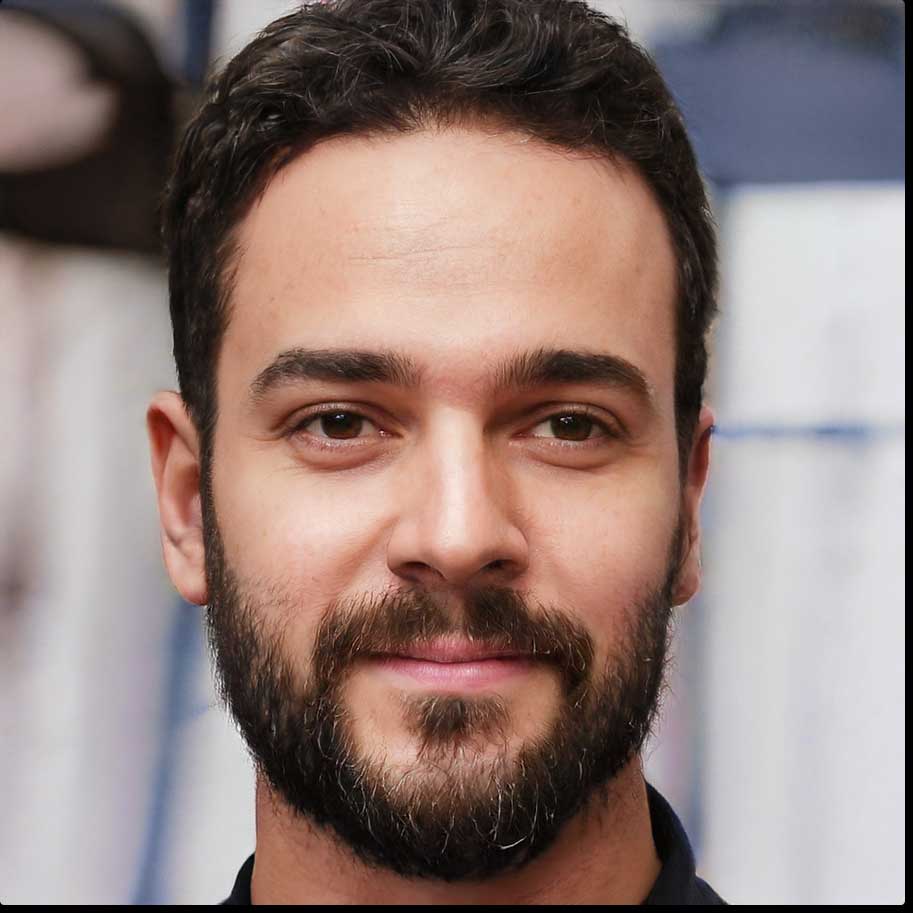