How to Be Operational Excellence Strategist - Job Description, Skills, and Interview Questions
Steps How to Become
- Obtain a Bachelor's Degree. A bachelor's degree in a related field such as business administration, operations management, or industrial engineering is typically required to become an operational excellence strategist.
- Gain Relevant Work Experience. In addition to the educational requirements, most employers will also require several years of relevant work experience in operations, management, or consulting.
- Participate in Professional Development Opportunities. Professional development can include attending conferences and workshops, enrolling in online courses, or simply reading relevant books and articles.
- Become Certified. Many employers may prefer to hire an operational excellence strategist who is certified by a professional organization such as the American Society for Quality (ASQ) or the Institute of Industrial and Systems Engineers (IISE).
- Develop Your Skills. It is important to stay up-to-date on industry trends and best practices to ensure that you are providing the best advice to your clients.
- Build Your Network. Building relationships with other operational excellence professionals can help you stay informed and keep up with the industry. Networking can also help you find job opportunities and expand your client base.
Operational excellence is a strategic approach to improving the delivery of products and services by focusing on optimizing processes, improving efficiency, and reducing costs. To achieve operational excellence, organizations must develop an effective strategy that involves skilled and efficient personnel. Skilled personnel are essential to ensuring that processes are operating at optimal levels and that resources are being used efficiently to produce desired results.
efficient personnel help to reduce costs by streamlining processes and identifying areas for improvement. By investing in training and providing employees with the knowledge and tools necessary to work effectively, companies can ensure that their operational excellence strategy is successful and that their personnel are both skilled and efficient.
You may want to check Product Strategist, Corporate Strategist, and Innovation Strategist for alternative.
Job Description
- Develop and implement operational excellence strategies, plans, and objectives.
- Work with business and IT stakeholders to identify and prioritize areas for improvement.
- Lead and facilitate process improvement workshops to define, prioritize, and design operational excellence initiatives.
- Analyze data and metrics to identify opportunities for improvement.
- Develop processes, tools and systems that enable business teams to efficiently and effectively execute their operations.
- Create performance dashboards to monitor performance, identify trends, and identify areas for improvement.
- Develop best practices and standards for operational excellence.
- Design and implement continuous improvement initiatives.
- Educate and train team members on operational excellence tools, techniques, and methodologies.
- Monitor process performance to evaluate the effectiveness of improvements.
Skills and Competencies to Have
- Strategic Thinking: Ability to identify, analyze and evaluate complex situations, synthesize trends and develop innovative strategies.
- Leadership: Ability to inspire, motivate and lead others to achieve organizational goals.
- Communication: Ability to communicate clearly, effectively and persuasively in both written and verbal form.
- Problem-Solving: Ability to identify, analyze and resolve complex issues in a timely manner.
- Process Improvement: Ability to identify, analyze, develop and implement process improvements.
- Change Management: Ability to manage change initiatives in an organization.
- Project Management: Ability to define, plan, execute and manage projects to successful completion.
- Technology: Knowledge of the latest technologies and their applications in business operations.
- Analytical Skills: Ability to collect and analyze data, draw meaningful conclusions and make sound decisions.
- Business Acumen: Understanding of organizational goals, strategies and current business trends.
Operational excellence is essential for any organization to achieve its goals. As an Operational Excellence Strategist, having the ability to identify, develop and implement solutions that improve business processes, reduce costs and boost productivity is essential. To do this effectively, one must have strong analytical skills, be able to develop an effective strategy, have excellent communication and organizational skills and be able to work collaboratively with various stakeholders.
it is important to understand the changing trends in the business environment and have the ability to think outside of the box and come up with innovative solutions. Having the right toolset, such as data analysis, process mapping and change management, will also help the Operational Excellence Strategist to bring about meaningful change within an organization. Having a thorough understanding of the organizations vision and objectives, as well as its processes and operations, will also help the Operational Excellence Strategist to develop solutions that will help the organization reach its goals.
Business Development Strategist, Digital Transformation Strategist, and Sales and Distribution Strategist are related jobs you may like.
Frequent Interview Questions
- What have been your greatest successes in developing an operational excellence strategy?
- Describe your experience with leading a cross-functional team to develop and execute an operational excellence strategy.
- What process improvements have you implemented that have had the most significant positive impact?
- How do you stay up-to-date on the latest developments in operational excellence strategies?
- Describe a situation where you had to lead a project with tight timelines.
- How do you prioritize tasks when working on an operational excellence strategy?
- What challenges have you encountered while developing and implementing an operational excellence strategy?
- How do you ensure that the operational excellence strategy you've developed is adhered to?
- What metrics do you use to measure the success of an operational excellence strategy?
- What experience do you have with developing and implementing automated processes?
Common Tools in Industry
- Kaizen. Kaizen is a Japanese term that refers to continuous improvement. Kaizen is a process that involves everyone in a company to improve their processes and systems. (eg: Toyota uses Kaizen to reduce waste and streamline their production process).
- Lean Six Sigma. Lean Six Sigma is a methodology that combines Lean and Six Sigma to improve quality and reduce waste. It focuses on identifying and eliminating any unnecessary steps in the process. (eg: Amazon uses Lean Six Sigma to reduce time spent on order fulfillment).
- Process Mapping. Process mapping is a visual representation of processes that clearly shows the steps involved in getting from the start of a process to the end. (eg: Starbucks uses process mapping to understand the steps involved in making each drink order).
- Root Cause Analysis. Root cause analysis is a process used to identify the root cause of a problem so that it can be addressed and eliminated. (eg: Apple uses root cause analysis to find the root cause of an issue with their products and develop solutions to fix it).
- Continuous Improvement. Continuous improvement is an ongoing effort to improve products, processes, and services. It focuses on small, incremental changes that add up over time to create large improvements. (eg: Microsoft uses continuous improvement to make small changes in their software that lead to better performance over time).
Professional Organizations to Know
- Lean Enterprise Institute
- American Society for Quality
- International Association for Six Sigma Certification
- Operational Excellence Society
- Project Management Institute
- Society of Manufacturing Engineers
- Institute of Industrial and Systems Engineers
- International Society of Automation
- International Quality Federation
- Association for Manufacturing Excellence
We also have Human Resources Strategist, Retail Strategist, and Supply Chain Management Strategist jobs reports.
Common Important Terms
- Kaizen. A Japanese business philosophy of continuous improvement. It emphasizes small, incremental changes that lead to a larger transformation over time.
- Lean Thinking. A management philosophy focused on eliminating waste and increasing efficiency. It encourages organizations to focus on delivering value to customers by streamlining processes and reducing costs.
- Process Improvement. The practice of systematically analyzing, evaluating, and optimizing a process to increase its effectiveness and efficiency.
- Root Cause Analysis. A problem-solving method used to identify the underlying cause of an issue. It involves breaking down a problem into smaller components to better understand what is causing it.
- Change Management. The practice of managing and implementing change in an organization. It involves understanding the impact of change on people, processes, and technology, and developing strategies to manage the transition.
- Project Management. The practice of planning, organizing, motivating, and controlling resources to achieve specific goals. It is focused on successfully completing a project on time and within budget.
- Quality Assurance. The practice of ensuring that products and services meet quality standards. It involves developing and maintaining quality systems, auditing processes, and implementing corrective actions when necessary.
- Performance Management. The practice of monitoring, evaluating, and improving individual and team performance in an organization. It involves setting goals, measuring progress, and providing feedback and coaching.
Frequently Asked Questions
Q1: What is an Operational Excellence Strategist? A1: An Operational Excellence Strategist is a professional who specializes in the development and execution of strategies that improve the efficiency, effectiveness, and profitability of an organization. Q2: What strategies do Operational Excellence Strategists typically employ? A2: Operational Excellence Strategists typically employ Lean Six Sigma, Kaizen, and other process improvement strategies to identify and eliminate waste, optimize processes, and drive cost savings. Q3: What kind of results can an Operational Excellence Strategist typically deliver? A3: An Operational Excellence Strategist can typically deliver improved customer satisfaction, increased operational efficiency, reduced costs, improved quality, and greater profitability. Q4: How can an Operational Excellence Strategist be measured? A4: An Operational Excellence Strategist can be measured by the number of processes improved, the cost savings realized, and the overall satisfaction of customers. Q5: What qualifications are necessary to become an Operational Excellence Strategist? A5: To become an Operational Excellence Strategist, one must typically have a degree in a related field, such as business administration or industrial engineering, and possess a comprehensive understanding of process improvement strategies and tools.What are jobs related with Operational Excellence Strategist?
- CRM Strategist
- Community Strategist
- Financial Planning and Analysis Strategist
- Business Analytics Strategist
- Energy Strategist
- User Experience Strategist
- Management Consultant Strategist
- Growth Strategist
- Venture Capital Strategist
- Healthcare Strategist
Web Resources
- Operational Excellence operationalexcellence.unc.edu
- Operational Excellence Operational Excellence at Illinois operationalexcellence.illinois.edu
- Operational excellence | Strategic Plan: Loyola University Chicago www.luc.edu
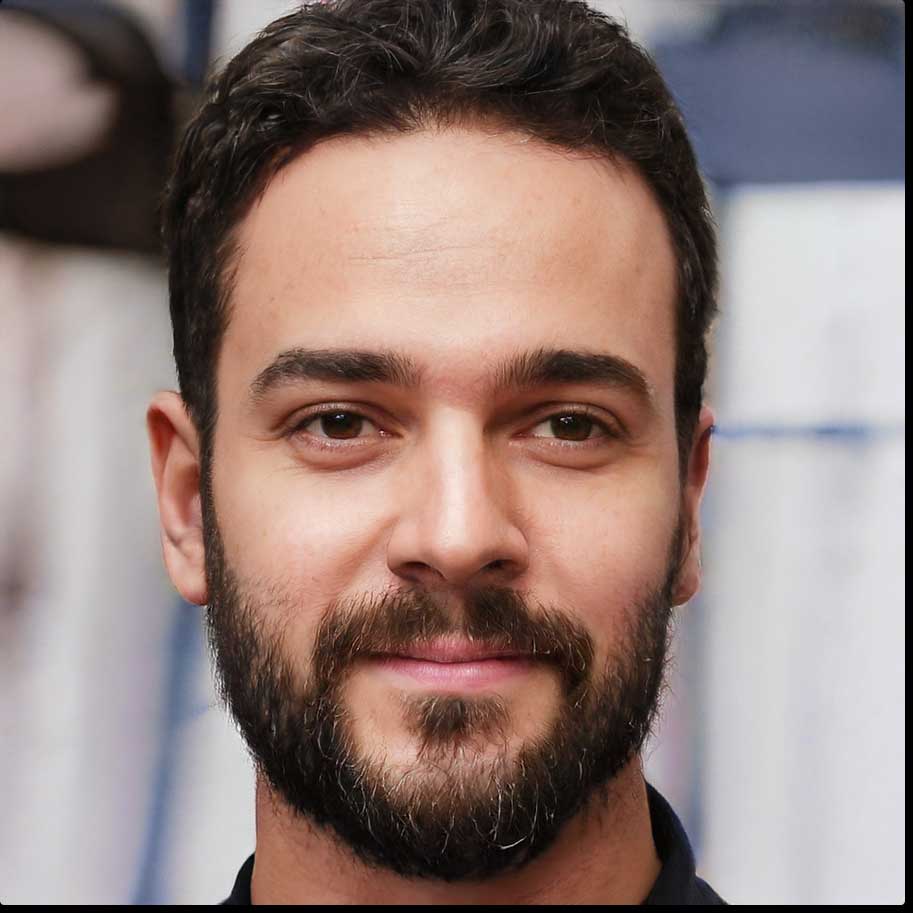