How to Be President of Manufacturing - Job Description, Skills, and Interview Questions
The President of Manufacturing oversees the production of goods and services in a company, and is responsible for ensuring all operations are running efficiently and productively. This role is crucial in order to maintain customer satisfaction and a successful bottom line. As a result, the President of Manufacturing must have a deep understanding of the production process, knowledge of the latest technology, and expertise in the areas of production planning, cost control, and quality control.
In addition, they must possess strong leadership skills to ensure that all employees are working together as a team and that all production goals are met on time and within budget. In turn, this will lead to improved customer satisfaction, increased profitability, and a positive overall business outlook.
Steps How to Become
- Obtain a relevant college degree. An undergraduate degree in business, engineering, or finance is recommended. Some employers may require a master's degree.
- Gain experience in the manufacturing industry. Many employers prefer to hire experienced professionals with a strong knowledge of the manufacturing industry. Consider internships, apprenticeships, and entry-level jobs to gain experience in the field.
- Develop a strong leadership skillset. Manufacturing presidents must possess strong leadership abilities in order to manage teams and drive innovation. Take lead positions in your current role and look for opportunities to hone your leadership skills.
- Network with industry professionals. Get to know the key players in the industry and stay informed about the latest trends and developments.
- Demonstrate your expertise. Present your knowledge and experience to potential employers through a well-crafted resume and portfolio.
- Pursue open positions. Look for available president positions in the manufacturing industry and apply for them directly. You may also want to contact recruiters or agencies that specialize in executive placements.
- Prepare for the interview process. Research the company and be prepared to discuss your experience and qualifications during the hiring process.
- Make sure you have the right qualifications and certifications. Many positions require certain licensing or certifications, such as a Certified Manufacturing Executive (CME) or Certified Production and Inventory Manager (CPIM). Make sure you have the necessary qualifications before applying for a position.
The success of a manufacturing president is strongly dependent on their ability to identify and implement ideal and competent solutions. The president must possess a comprehensive understanding of all aspects of the manufacturing process, from production to distribution, as well as a deep knowledge of the latest technologies and trends. they must possess excellent leadership qualities, enabling them to inspire their team and create an environment that fosters collaboration and innovation.
In order to ensure optimal performance and output, the president must be able to plan strategically, set clear objectives, and delegate tasks effectively. Finally, they must be able to effectively manage their team by providing guidance, feedback, and recognition for a job well done. By leveraging these qualities and skills, a manufacturing president can ensure that their organization remains competitive in the industry and achieves its goals.
You may want to check President and CEO, President of the Board of Directors, and President of Human Resources for alternative.
Job Description
- Oversee the daily operations of the manufacturing facility
- Develop and implement production strategies to meet customer and company requirements
- Monitor and analyze plant performance and identify areas for improvement
- Lead and manage the manufacturing team to ensure objectives are achieved
- Monitor and manage inventory levels to ensure timely delivery of products
- Establish and maintain product quality standards
- Develop and implement cost reduction initiatives
- Establish safety standards and procedures and ensure compliance
- Negotiate contracts and purchase orders with suppliers
- Develop long-term relationships with key stakeholders and partners
- Manage capital projects and investments to ensure successful completion on time and within budget
- Analyze production data and trends to identify opportunities for improvement and cost savings
- Develop and present annual budget and business plans for approval
- Monitor regulatory compliance with applicable laws and regulations
Skills and Competencies to Have
- Strategic Planning: Ability to develop and implement long-term plans for manufacturing operations.
- Leadership: Ability to lead and motivate a team of managers and employees.
- Financial Acumen: Ability to understand and interpret financial data, create budgets, and manage costs.
- Process Improvement: Ability to identify and streamline inefficient processes.
- Quality Control: Ability to ensure products meet quality standards.
- Problem Solving: Ability to identify and solve problems in a timely manner.
- Communication: Excellent communication skills, both verbal and written.
- Risk Management: Ability to identify and mitigate potential risks associated with manufacturing operations.
- Project Management: Excellent organizational skills and ability to manage multiple projects simultaneously.
- Regulatory Compliance: Knowledge of applicable laws, regulations, and standards related to manufacturing operations.
Successful presidents of manufacturing must possess a variety of skills in order to lead a team effectively. The most important skill for a president of manufacturing is the ability to think strategically. Strategic thinking involves analyzing data and developing effective short- and long-term plans to ensure the organization is optimizing resources and reaching its goals.
This skill also requires the president to stay abreast of industry trends and customer demands, as well as to develop competitive advantages. a president of manufacturing should have strong communication and interpersonal skills to effectively collaborate with colleagues and customers. Finally, they should have an understanding of financial principles and cost management to ensure the organization is operating cost-effectively and profitably.
With these skills, a president of manufacturing can effectively lead a team and reach organizational objectives.
President of Operations, President of Logistics, and President of Research and Development are related jobs you may like.
Frequent Interview Questions
- What experience do you have in managing a manufacturing organization?
- How would you go about developing and implementing a successful strategy for the manufacturing division?
- What would be your approach to ensuring quality control in the manufacturing process?
- How would you handle negotiations with suppliers and customers?
- What are your thoughts on automation and its impact on production?
- What strategies and techniques do you use to motivate and develop your team?
- How would you handle difficult situations and personnel issues?
- What is your policy on safety in the workplace?
- How do you stay up to date on the latest manufacturing technologies and industry trends?
- How would you ensure that the manufacturing division meets its goals and objectives?
Common Tools in Industry
- Quality Control System. A system used to collect and analyze data to ensure the quality of products (eg: Six Sigma).
- Manufacturing Execution System (MES). A system used to track and monitor the production process (eg: SAP ME).
- Automated Material Handling System. A system used to move and store materials and components efficiently (eg: Kuka Robotics).
- Production Planning Software. Software used to optimize and manage manufacturing operations (eg: Oracle Manufacturing Cloud).
- Industrial Internet of Things (IIoT). A network of connected machines and devices that collect and share data (eg: Predix).
- Advanced Analytics Solutions. Solutions used to analyze large sets of data to uncover insights that can drive operational improvements (eg: IBM Watson).
- Supply Chain Management Software. Software used for managing and optimizing the flow of materials and products (eg: SAP SCM).
- Enterprise Resource Planning (ERP) Software. Software used to integrate the different functions of a company into one system (eg: Oracle ERP).
- 3D Printing Solutions. Solutions used to quickly produce parts, components, and products with minimal waste (eg: Stratasys 3D Printers).
- Digital Twin Technology. Technology used to digitally replicate physical assets, processes, and systems (eg: Siemens Digital Twin).
Professional Organizations to Know
- American Society of Mechanical Engineers (ASME)
- Association for Manufacturing Technology (AMT)
- International Association of Machinists and Aerospace Workers (IAM)
- National Association of Manufacturers (NAM)
- Manufacturing Extension Partnership (MEP)
- Society of Manufacturing Engineers (SME)
- National Tooling and Machining Association (NTMA)
- International Manufacturing Technology Show (IMTS)
- Automation Federation
- International Federation of Robotics (IFR)
We also have President of Retail Operations, President of Product Development, and President of Sales jobs reports.
Common Important Terms
- Quality Assurance. The process of ensuring that products meet the established standards of quality.
- Production Planning. The process of organizing production tasks to efficiently meet customer demand.
- Inventory Management. The process of tracking and managing inventory levels to ensure stock availability and minimize costs.
- Lean Manufacturing. An approach to manufacturing that focuses on eliminating waste, increasing efficiency, and reducing costs.
- Supply Chain Management. The process of managing the flow of materials and goods within a company and its suppliers.
- Process Improvement. The process of making changes to existing processes in order to improve efficiency and reduce costs.
- Cost Reduction. The process of identifying and implementing cost-saving measures in order to reduce expenses.
- Quality Control. The process of monitoring and verifying that products meet quality standards.
Frequently Asked Questions
What experience does the President of Manufacturing need?
The President of Manufacturing typically needs extensive experience in manufacturing and operations management, as well as strategic planning, budgeting, and team leadership.
How many years of experience is necessary for the President of Manufacturing?
Generally, the President of Manufacturing should have at least 10 years of experience in a manufacturing environment.
What responsibilities does the President of Manufacturing have?
The President of Manufacturing is responsible for developing and executing strategies to ensure operational excellence, optimize production processes and resources, and meet safety and quality standards.
What types of teams does the President of Manufacturing oversee?
The President of Manufacturing typically oversees teams such as production, engineering, supply chain, quality assurance, and health and safety.
What qualifications are required for the President of Manufacturing?
The President of Manufacturing typically needs a Bachelor's degree in a related field such as manufacturing engineering, business administration, or operations management. A Master's degree may also be preferred.
What are jobs related with President of Manufacturing?
- President of Marketing
- President of Business Development
- President of Student Government
- President of Engineering
- President of Technology
- President of Strategic Planning
- President of Finance
- President of the Board
Web Resources
- ICYMI: President Biden Brings Back Manufacturing Jobs www.presidency.ucsb.edu
- About UCI Manufacturing - University of California, Irvine manufacturing.uci.edu
- President Richard McCullough - Office of the President president.fsu.edu
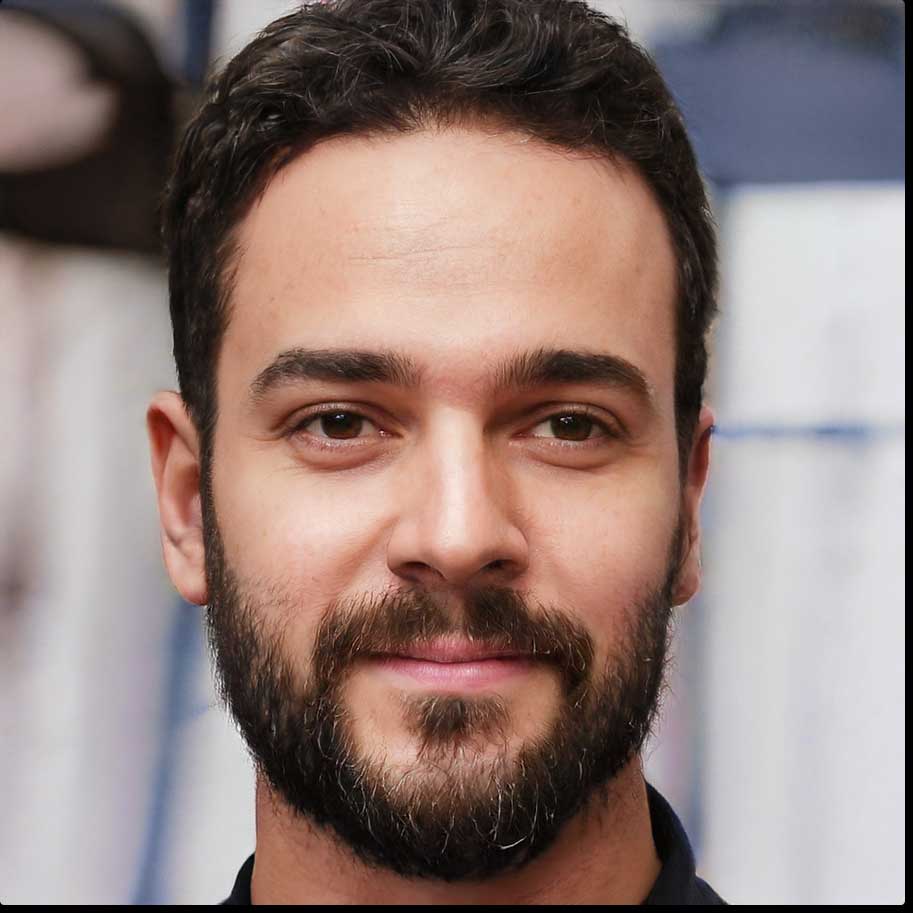