How to Be Metal Worker - Job Description, Skills, and Interview Questions
The demand for metal workers has increased significantly in recent years, due in part to the growth of new industries and the expansion of existing ones. This rise in demand has had a direct effect on the wages of metal workers, which have gone up as employers compete for skilled labor. As a result of higher wages, more people are choosing to pursue metalworking as a profession, leading to a shortage of experienced metal workers in certain areas.
This shortage has caused businesses to invest more in training and education for metal workers in order to ensure they have the necessary skills to meet their needs. As a result, employers are now offering higher wages, better benefits, and better job security for metal workers, making it a more attractive career choice than ever before.
Steps How to Become
- Obtain a High School Diploma or GED. Most employers require metal workers to have a high school diploma or GED.
- Complete a Certificate Program or Apprenticeship. Metal workers may complete a certificate program or apprenticeship to learn the necessary skills involved in welding and metal fabrication.
- Gain Experience. Gaining experience in the field is essential to becoming a successful metal worker.
- Obtain Licensure or Certification. Depending on the type of job, some metal workers may need to obtain licensure or certification to demonstrate their expertise in their field.
- Apply for Jobs. After obtaining the necessary education and experience, metal workers can begin searching for jobs in the field.
Proper planning and efficiency are key components to becoming an ideal metal worker. Planning involves organizing the tasks that need to be completed, developing a timeline, and mapping out the resources needed. Efficiency involves performing the tasks in an organized and timely manner.
Being an ideal metal worker also requires an understanding of the tools and techniques used in metalworking, such as welding, cutting, and grinding. Having a good knowledge base of the various materials used in metalworking is also essential. Furthermore, safety procedures must be strictly followed to avoid accidents.
By following these steps, a metal worker can become an ideal and efficient professional in their craft.
You may want to check Site Engineer, Painter & Decorator, and Trim Carpenter for alternative.
Job Description
- Fabricator Responsible for cutting, bending, and shaping metal pieces to create products according to customer specifications.
- Welder Joins metal pieces together by using a variety of welding techniques.
- Machinist Operates machinery to produce metal parts or products.
- Metal Finisher Uses various techniques to finish metal products, including grinding, polishing, and buffing.
- Sheet Metal Worker Cuts and forms sheet metal pieces to create products such as ducts, roofing, and siding.
- Extrusion Operator Operates an extrusion machine to form metal into shapes.
- Casting Operator Operates a casting machine to shape molten metal into specific shapes.
- Metal Shaping Technician Uses hand tools such as hammers and files to shape metal into desired shapes.
- Metal Assembly Technician Assembles metal parts into finished products.
- Quality Control Inspector Inspects finished products for accuracy and quality.
Skills and Competencies to Have
- Ability to read and interpret blueprints, schematics, and technical drawings
- Proficient in the use of hand tools, such as hammers, chisels, saws, and drill presses
- Skilled in welding processes such as arc, gas, and MIG welding
- Knowledge of metallurgy concepts and principles
- Ability to fabricate and assemble components and structures
- Familiarity with occupational safety and health regulations
- Ability to work independently or in a team environment
- Excellent problem-solving skills
- Strong attention to detail
- Ability to follow instructions and take direction
Having a strong background in metalworking is essential for success in the field. Knowledge of welding and forming techniques, as well as an understanding of the properties and characteristics of different metals, are all important skills for metalworkers. good problem-solving skills and an eye for detail are critical to ensure that components are produced to the highest standard.
The ability to read and interpret blueprints is also an important skill for metalworkers to have, as it enables them to accurately create components according to specifications. With these skills, metalworkers can ensure that the products they produce are of the highest quality and meet the expectations of the customer.
Drywall Installer, Millwork Installer, and Scaffolder are related jobs you may like.
Frequent Interview Questions
- What experience do you have working with different types of metal?
- How would you go about fabricating a complex metal structure?
- What methods do you use to ensure accuracy when cutting metal?
- Describe a difficult metal project you have completed.
- What safety precautions do you take while working with metal?
- How do you troubleshoot problems with machinery used to fabricate metal?
- Are you familiar with welding materials?
- Describe the process you use when welding metals.
- What type of maintenance do you perform on your tools and machinery?
- How would you go about training a new team member for metal fabrication?
Common Tools in Industry
- Hammer. A hand tool used to strike or drive nails, pins, and other fasteners. (eg: Hammering in nails to hang pictures)
- Drill. A tool used to make a cylindrical hole. (eg: Drilling a hole for a screw)
- Grinder. A power tool used to grind and shape metal. (eg: Grinding down welds to make them flush against the surface)
- Welder. A device used to join two metal pieces together. (eg: Welding two metal plates together to form a frame)
- Saw. A tool used to cut through metal, wood, and other materials. (eg: Sawing through a sheet of metal to create a desired shape)
- Screwdriver. A tool used to turn screws and bolts. (eg: Screwing in bolts to secure a frame)
- Pliers. A tool used to grip, twist, and bend objects. (eg: Using pliers to bend a metal piece into the desired shape)
- Files. A tool used to smooth and sharpen edges. (eg: Filing down sharp edges on a metal piece)
Professional Organizations to Know
- American Welding Society
- National Institute of Metalworking Skills
- Metal Fabricators Association
- International Iron and Steel Institute
- Steel Structures Painting Council
- Sheet Metal and Air Conditioning Contractors' National Association
- American Foundry Society
- Association for Iron & Steel Technology
- American Society of Mechanical Engineers
- American Society for Metals
We also have Carpenter, Tile Setter, and Foundry Worker jobs reports.
Common Important Terms
- Fabrication. The process of creating objects and structures by cutting, shaping, and assembling materials.
- Welding. A process that joins materials, usually metals or thermoplastics, by causing coalescence.
- Brazing. A metal-joining process that uses a non-ferrous filler metal to join two pieces of metal together.
- Soldering. A metal-joining process that creates a permanent bond between two pieces of metal by using a relatively low melting point alloy.
- Tooling. The use of a variety of tools to shape and form metal into the desired shape.
- Heat Treating. A process used to change the physical and chemical properties of a metal through the application of heat.
- Forging. A metalworking process that involves shaping metal using localized compressive forces.
- Casting. A process in which a liquid material is poured into a mold and allowed to solidify into the desired shape.
- Machining. A process that uses cutting tools to remove material from a workpiece in order to create a desired shape or finish.
- Sheet Metal Working. A metalworking process involving the forming of sheet metal into desired shapes and sizes.
Frequently Asked Questions
What is metalworking?
Metalworking is the process of shaping and fabricating metal parts and components by cutting, bending, and assembling processes. It includes a range of activities such as cutting, forming, welding, and machining.
What tools are used in metalworking?
Common tools used in metalworking include drills, saws, lathes, milling machines, grinding machines, presses, and shears.
What materials are used in metalworking?
Materials used in metalworking include ferrous metals such as steel and iron, as well as non-ferrous metals such as aluminum, brass, copper, and stainless steel.
What safety precautions should be taken when performing metalworking?
When performing metalworking it is important to use the proper protective equipment such as eye protection, gloves, and long sleeves. It is also important to be aware of potential hazards such as flying debris, hot pieces of metal, and sparks.
What types of products can be created through metalworking?
Products that can be created through metalworking include vehicles, tools, furniture, appliances, artwork, and jewelry.
What are jobs related with Metal Worker?
- Wood Turner
- Form Carpenter
- Finish Carpenter
- Doormaker
- Masonry Worker
- Wood Carver
- Boat Builder
- Structural Steel Worker
- Cabinet Maker
- Stair Builder
Web Resources
- Sheet Metal Worker - The Apprentice School www.as.edu
- Metalform EDU | Precision Metalforming Association www.pma.org
- Tri-C Sheet Metal Worker Program: Cleveland - Cuyahoga ¦ www.tri-c.edu
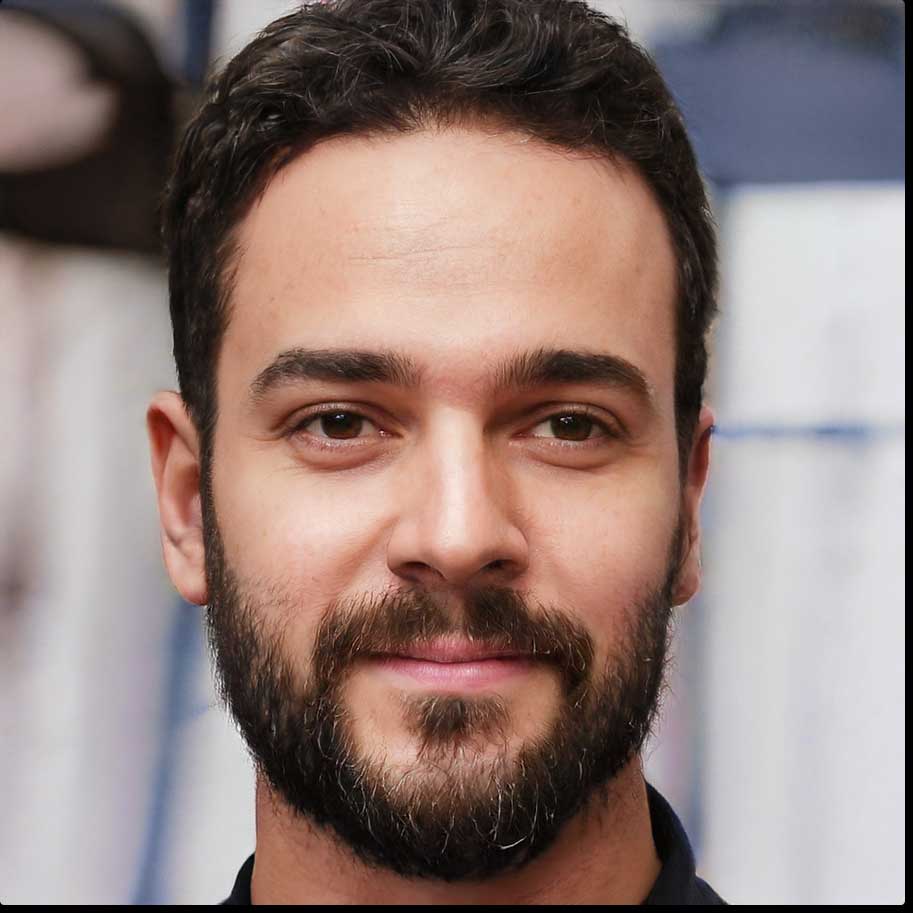