How to Be Manufacturing/Project Manager - Job Description, Skills, and Interview Questions
The increasing demand for global manufacturing has led to a need for more Project Managers in the industry. Project Managers are responsible for overseeing the production, cost, and quality of projects from start to finish. As a result, they have the ability to greatly impact the success of a manufacturing company.
They can develop efficient processes, reduce costs, and ensure that deadlines are met. Project Managers also work with teams of engineers and technicians to ensure that the highest standards of safety, quality, and performance are maintained. By effectively utilizing their expertise in planning, scheduling, and problem-solving, they can help to ensure that all projects are completed on time and within budget.
Steps How to Become
- Earn a Bachelor's Degree. Most employers prefer to hire managers with a bachelor's degree in engineering, business, or a related field. This degree may include courses in engineering, project management, accounting, and finance.
- Consider Earning a Master's Degree. Some employers may require a master's degree in business administration (MBA), engineering management, industrial engineering, or a related field.
- Obtain Relevant Experience. Employers often prefer to hire manufacturing and project managers who have several years of experience working in the field. Consider taking on additional responsibilities at your current job to gain additional experience.
- Get Certified. Becoming certified as a project management professional (PMP) can demonstrate your expertise in the field to employers.
- Take Courses and Seminars. Many employers look for candidates who have taken courses or attended seminars related to project management or manufacturing. This can help you stay up-to-date on the latest developments in the field and demonstrate your commitment to professional development.
- Network. Networking is an important part of finding employment in any field. Consider attending professional conferences and joining professional organizations related to your field. This is an excellent way to create contacts and make yourself known to potential employers.
The Manufacturing/Project Manager must possess a combination of technical and managerial skills in order to be successful. They must have a good understanding of the production process, as well as excellent organizational, problem-solving, and communication abilities. They must also have the ability to plan and develop projects, anticipate potential problems, and find solutions quickly.
This combination of skills leads to improved efficiency and productivity, as well as better time management and cost control. Furthermore, a strong focus on customer satisfaction is essential for a successful Manufacturing/Project Manager, as they must be able to ensure that customer requirements are met within tight deadlines. having the right person in the position of Manufacturing/Project Manager is essential for the success of any organization.
You may want to check Project Technician, Telecommunications/Project Manager, and Project Consultant for alternative.
Job Description
- Manufacturing Manager: Responsible for overseeing the day-to-day operations of the manufacturing plant and ensuring that production is completed in a timely and efficient manner. Responsibilities include managing personnel, monitoring production processes, and controlling costs.
- Production Manager: Responsible for overseeing and managing production activities in a manufacturing setting. Responsibilities include planning, scheduling, coordinating, and directing the activities of production personnel.
- Quality Manager: Responsible for ensuring that all products meet the company's standards of quality before they are released to the market. Responsibilities include developing and implementing quality assurance processes and procedures, monitoring production processes, and conducting quality audits.
- Process Engineer: Responsible for developing and maintaining production processes in a manufacturing setting. Responsibilities include designing, testing, and optimizing manufacturing processes, troubleshooting process issues, and providing technical support to production personnel.
- Project Manager: Responsible for overseeing projects in a manufacturing setting. Responsibilities include managing resources, coordinating activities, ensuring project timelines are met, and providing status updates to stakeholders.
Skills and Competencies to Have
- Ability to create and implement effective project plans and schedules
- Strong communication and interpersonal skills
- Knowledge of manufacturing processes and procedures
- Expertise in problem solving and decision making
- Ability to lead and motivate teams
- Knowledge of safety regulations and standards
- Understanding of quality assurance and control
- Ability to manage multiple projects simultaneously
- Proficiency in financial management and budgeting
- Proficiency in computer software programs related to project management
Effective communication is one of the most important skills for a Manufacturing/Project Manager to have. A Manufacturing/Project Manager must be able to communicate effectively with the team, clients, and other stakeholders to ensure that the project is running smoothly. Without good communication, the project can face delays, increased costs, and other problems.
Good communication also ensures that everyone is on the same page, helping to solve any conflicts that may arise. effective communication can help with problem solving, as it allows for open dialogue about the project and any issues that may be encountered. Good communication also helps to build trust with clients and team members, allowing for better collaboration and a smoother workflow.
having strong communication skills can help a Manufacturing/Project Manager to be successful in their job.
Junior Project Manager, Project Scheduler, and Automotive/Project Manager are related jobs you may like.
Frequent Interview Questions
- What experience do you have managing projects within a manufacturing environment?
- How do you ensure that cost and time constraints are met while working on a project?
- How do you stay organized when dealing with multiple projects at the same time?
- How do you handle difficult situations or personnel conflicts related to a project?
- Describe a successful project you have managed in the past.
- What techniques do you use to monitor progress on projects?
- How do you ensure that your team works together effectively?
- What strategies do you employ to keep up-to-date with new manufacturing technologies and trends?
- How do you handle unexpected changes to a project timeline or budget?
- What metrics do you use to measure the success of a project?
Common Tools in Industry
- Kanban Board. A visual management tool used to visualize and manage workflows, typically used in manufacturing and project management. (e. g. Trello)
- Enterprise Resource Planning (ERP) Software. A system used to manage the entire enterprise, from supply chain to finance and sales. (e. g. SAP)
- Project Management Software. A tool used to plan, assign, track, and report tasks related to a project. (e. g. Microsoft Project)
- Quality Management System (QMS). A system used to ensure that products meet customer requirements and industry standards. (e. g. ISO 9001)
- Manufacturing Execution System (MES). A system used to manage the manufacturing process, from production planning to shop floor execution. (e. g. FactoryTalk Manufacturing Execution System)
- Computer-Aided Design (CAD). A software used to create digital models of products and components for manufacturing. (e. g. SolidWorks)
- Computer-Aided Manufacturing (CAM). A software used to generate instructions for machines to produce parts from a digital model. (e. g. Mastercam)
- Manufacturing Process Management (MPM). A system used to monitor and control production processes in real time. (e. g. Siemens Digital Factory)
Professional Organizations to Know
- American Management Association (AMA)
- Association for Manufacturing Excellence (AME)
- Institute of Industrial and Systems Engineers (IISE)
- International Quality Federation (IQF)
- International Society of Automation (ISA)
- National Association of Manufacturers (NAM)
- Project Management Institute (PMI)
- Society of Manufacturing Engineers (SME)
- The Association for Operations Management (APICS)
- The Manufacturing Institute (MI)
We also have Project Developer, Project Manager Assistant, and Project Architect jobs reports.
Common Important Terms
- Product Development. The process of creating a new product or improving an existing one in order to meet customer needs.
- Quality Management. The practice of managing quality in order to meet customer requirements and company standards.
- Cost Control. The process of keeping expenses within a predetermined budget.
- Supply Chain Management. The management of the flow of goods and services from the point of origin to the point of consumption.
- Lean Manufacturing. A manufacturing methodology that focuses on eliminating waste and optimizing efficiency.
- Production Planning. The process of setting goals, objectives, and schedules for the production of goods and services.
- Risk Management. The practice of minimizing and mitigating risk associated with operations.
- Scheduling. The process of organizing resources and tasks to ensure projects are completed in a timely manner.
- Quality Assurance. The practice of monitoring and verifying that products meet quality standards.
- Continuous Improvement. The practice of making small but continual improvements to processes in order to increase efficiency and reduce costs.
Frequently Asked Questions
Q1: What is a Manufacturing/Project Manager? A1: A Manufacturing/Project Manager is responsible for planning, organizing, and directing the operations of a manufacturing or project environment. They are responsible for ensuring that projects are completed on time, within budget and to the required quality standards. Q2: What are the duties of a Manufacturing/Project Manager? A2: A Manufacturing/Project Manager's duties include setting production schedules, monitoring production processes, overseeing inventory levels, managing staff, and ensuring quality control standards are met. They also supervise project teams, create project plans, and manage budgets. Q3: What qualifications do you need to become a Manufacturing/Project Manager? A3: To become a Manufacturing/Project Manager, you typically need a bachelor's degree in engineering, business management or related field. Relevant work experience in a manufacturing or project-focused environment is also required. Q4: What challenges does a Manufacturing/Project Manager face? A4: Some challenges that a Manufacturing/Project Manager may face include meeting production deadlines, managing competing priorities, keeping costs down, dealing with unexpected delays or changes in plans, and ensuring quality control standards are met. Q5: What skills are necessary to succeed as a Manufacturing/Project Manager? A5: To succeed as a Manufacturing/Project Manager, you must have strong analytical and problem-solving skills, excellent communication and interpersonal skills, attention to detail, and the ability to multitask and work under pressure. You must also be able to work independently and as part of a team.What are jobs related with Manufacturing/Project Manager?
- Project Management Intern
- IT Project Manager
- Project Manager Trainee
- Project Leader
- Senior Project Architect
- Senior Project Analyst
- Project Maintenance Technician
- Senior Project Manager
- Project Scientist
- Project Engineer
Web Resources
- Manufacturing Manager Job Description and Duties - Goodwin ¦ www.goodwin.edu
- Manufacturing Management - Tiffin University www.tiffin.edu
- What is Manufacturing Management? | Goodwin University www.goodwin.edu
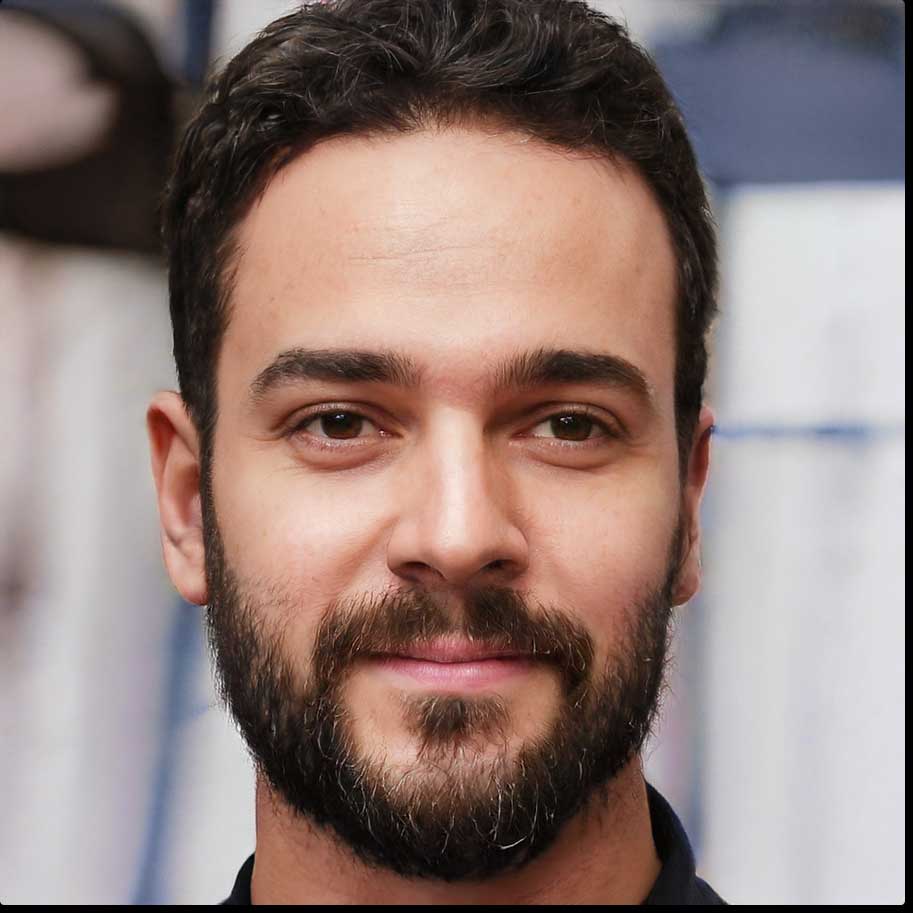