How to Be Logistics Manager - Job Description, Skills, and Interview Questions
Steps How to Become
- Earn a Bachelor's Degree. Pursuing a bachelors degree in logistics, supply chain management, business, or a related field is the first step to becoming a logistics manager. This four-year degree will provide students with the necessary knowledge and skills to work in the logistics industry.
- Gain Experience. It is important for potential logistics managers to have some experience in the field. Most employers prefer candidates who have three or more years of experience in logistics or a related field.
- Earn a Certification. Earning a professional certification may help a candidate stand out in the job market. The American Society of Transportation and Logistics offers its Certified Logistics Professional certification to individuals with at least three years of logistics experience.
- Get a Job. Logistics managers typically need to have at least a bachelors degree and some experience in the field in order to get a job. Logistics manager positions can be found in fields such as manufacturing, retail, and the government.
- Continue Education. Many logistics managers choose to continue their education by pursuing a masters degree or other advanced education in logistics. This can help them stay up to date with changes in the industry and gain additional skills that may give them an edge in the job market.
The success of a logistics manager depends on their ability to be reliable and competent. This requires careful planning and organization, as well as an understanding of the industry and stakeholders involved. An effective logistics manager needs to be able to anticipate delays, coordinate shipments, and ensure that goods are delivered on time and in good condition.
They also need to be able to identify potential problems quickly and resolve them in a timely manner. Furthermore, they must have excellent communication skills in order to stay in contact with customers, suppliers, and other stakeholders. Finally, they must have the ability to think critically and make sound decisions under pressure in order to ensure that the entire operation runs smoothly.
All of these skills combined make for a reliable and competent logistics manager.
You may want to check Facilities Manager, Inventory Manager, and Security Manager for alternative.
Job Description
- Develop, implement, and manage logistics plans and strategies that are cost-efficient and compliant with company policies.
- Plan, direct, and coordinate the storage, distribution, and delivery of goods.
- Negotiate contracts with suppliers and vendors to ensure timely delivery of goods at the best possible cost.
- Monitor inventory levels and oversee the ordering of necessary items to maintain appropriate stock levels.
- Oversee all customs clearance activities, ensuring compliance with applicable laws and regulations.
- Research and develop cost-saving measures for transportation, materials, and other related logistics operations.
- Maintain records of all transactions and activities related to the shipment of goods.
- Collaborate with other departments to ensure that customer service objectives are met in a timely manner.
- Develop performance standards and metrics to measure the efficiency of the logistics operations.
- Establish and maintain relationships with key stakeholders, such as suppliers and vendors.
Skills and Competencies to Have
- Knowledge of transportation and freight regulations.
- Ability to coordinate and manage multiple projects simultaneously.
- Proficiency in inventory management and product ordering.
- Excellent problem-solving and decision-making skills.
- Knowledge of customer service best practices.
- Ability to manage budgeting and cost analysis.
- Strong communication and interpersonal skills.
- Proficiency in the use of logistics software and other related technologies.
- Understanding of supply chain principles and practices.
- Ability to work under pressure and meet tight deadlines.
Logistics managers must possess a wide range of skills in order to be successful. Chief among these is the ability to effectively manage people and resources. A successful logistics manager must possess strong organizational skills, excellent communication skills, and the ability to effectively delegate tasks.
they must have a good understanding of the industry, be knowledgeable about regulations and have a keen eye for detail. The ability to think strategically and plan ahead is also essential as it allows them to anticipate potential problems and develop effective solutions. Good problem-solving skills are also essential as they enable logistics managers to quickly and efficiently respond to changing circumstances.
All these skills work in tandem to ensure that goods and services are delivered on time and within budget, which is crucial for any business.
Maintenance Manager, Network Manager, and Health and Safety Manager are related jobs you may like.
Frequent Interview Questions
- What experience do you have in logistics management?
- How have you utilized technology and software to improve logistics operations?
- What strategies have you employed to reduce costs in the logistics process?
- How do you work with other departments to ensure quick and efficient deliveries?
- What is your approach to resolving customer complaints?
- What experience do you have in developing and implementing logistics policies?
- How do you stay informed of changing regulations and industry trends?
- What strategies have you used to increase productivity and efficiency in the supply chain?
- How do you ensure safety in the workplace and in the transportation of goods?
- What systems have you implemented to monitor performance and track inventory?
Common Tools in Industry
- Warehouse Management System (WMS). A computer system used to store, manage and track inventory, shipments, and other logistics operations. Example: SAP Extended Warehouse Management.
- Transportation Management System (TMS). A software system used to plan, execute and monitor the shipment of goods. Example: LogiNext Mile.
- Supply Chain Management Software (SCM). A software system used to coordinate and optimize the flow of goods and information between different parts of a supply chain. Example: Oracle Supply Chain Management Cloud.
- Route Optimization Software. A software system used to calculate the most efficient route for a shipment or series of shipments based on cost, delivery time, weight, and other factors. Example: OptimoRoute.
- Freight Billing and Auditing Software. A software system used to manage freight invoices, analyze freight expenses, and find cost savings opportunities. Example: FreightAudit.
- Order Management System (OMS). A software system used to manage customer orders, including order entry, tracking, and fulfillment. Example: Oracle Order Management Cloud.
Professional Organizations to Know
- Council of Supply Chain Management Professionals (CSCMP)
- International Warehouse Logistics Association (IWLA)
- American Society of Transportation & Logistics (AST&L)
- Transportation Intermediaries Association (TIA)
- National Industrial Transportation League (NITL)
- National Retail Federation (NRF)
- International Air Transport Association (IATA)
- International Road Transport Union (IRU)
- Air Cargo Association of America (ACAA)
- Port Logistics Group (PLG)
We also have Design Manager, Vendor Management Manager, and Supply Chain Manager jobs reports.
Common Important Terms
- Supply Chain Management (SCM) The coordination of the storage, movement, and delivery of materials, parts, and finished goods from raw materials to the end customer.
- Logistics The process of planning, implementing, and controlling the efficient and effective storage and movement of goods and services from point of origin to point of consumption.
- Distribution Network A system of interconnected entities that is responsible for the delivery of goods and services from the point of origin to the desired destination.
- Freight Forwarding The process of arranging for the transportation of goods from one place to another.
- Warehousing The process of storing goods in a warehouse for future use or sale.
- Inventory Management The process of tracking, ordering, storing, and controlling inventory to ensure that there is enough stock to meet customer needs while avoiding overstocking or stock-outs.
- Transportation Planning The process of planning, organizing, and controlling the movement of goods from one place to another.
- Procurement The process of acquiring goods or services from external sources in order to meet an organizations needs.
Frequently Asked Questions
What qualifications are required to become a Logistics Manager?
Logistics Managers typically require a degree in supply chain management, logistics, business, or a related field. Other qualifications may include experience in inventory control, warehousing, and transportation.
What responsibilities does a Logistics Manager have?
Logistics Managers are responsible for overseeing the entire logistics process, including planning and organizing the distribution of goods, coordinating with transportation providers, and ensuring the timely delivery of goods to customers. They also manage inventory and oversee the storage and warehousing of goods.
How much do Logistics Managers make annually?
According to PayScale, the average annual salary for a Logistics Manager is $59,831.
What skills are necessary for a Logistics Manager?
Logistics Managers must have strong organizational and communication skills, as well as knowledge of processes and regulations related to transportation, inventory management, and warehousing. They must also be able to multitask and work well under pressure.
What is the job outlook for Logistics Managers?
According to the Bureau of Labor Statistics, the job outlook for Logistics Managers is expected to grow 5% through 2029. This growth is faster than the average for all occupations.
What are jobs related with Logistics Manager?
- Sales Operations Manager
- Quality Assurance Manager
- Retail Manager
- Product Manager
- Transportation Manager
- Business Development Manager
- IT Manager
- Hospitality Manager
- IT Support Manager
- Environmental Manager
Web Resources
- What Is a Logistics Manager and How to Become One www.wgu.edu
- What Is a Logistics Manager? | GCU Blog www.gcu.edu
- Logistics Manager | NC State Online and Distance Education online-distance.ncsu.edu
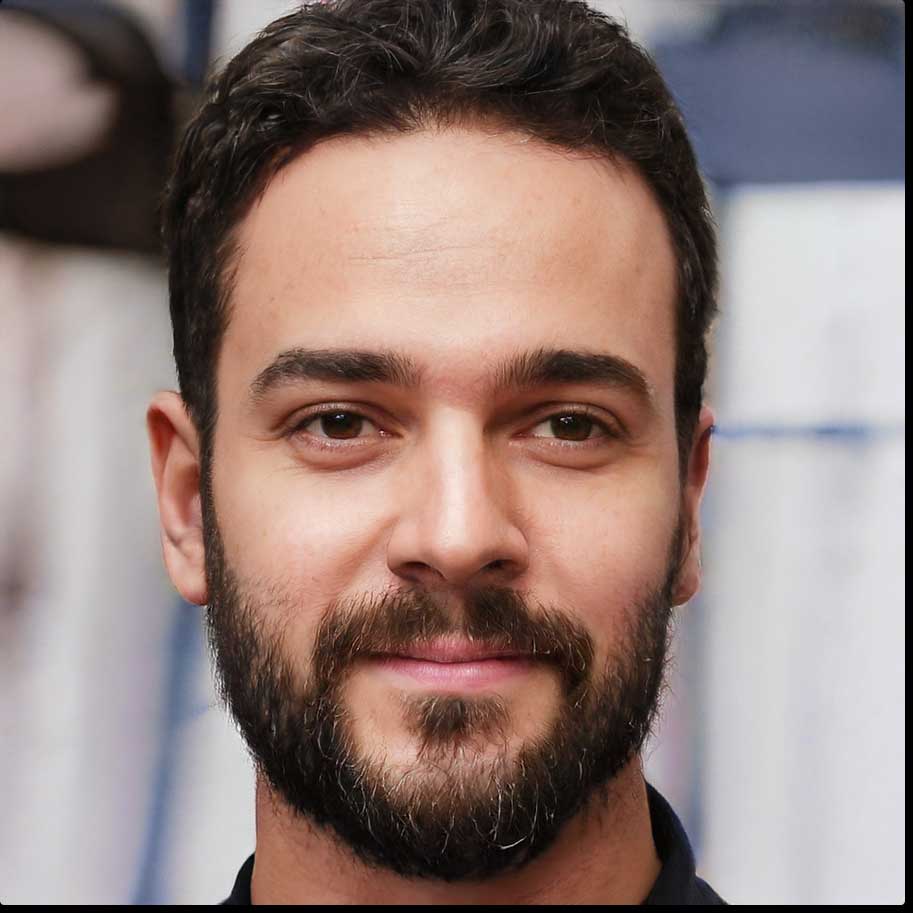