How to Be Health and Safety Manager - Job Description, Skills, and Interview Questions
The Health and Safety Manager plays an important role in ensuring the safety of employees and customers both in the workplace and out in the public. By developing policies, plans, and procedures to reduce risks, they help protect individuals from physical harm and potential legal liabilities. They also train staff on safety regulations and monitor ongoing compliance, conduct investigations into accidents and incidents, and identify areas for improvement.
In addition, they help companies develop emergency response plans and evaluate the effectiveness of existing safety protocols. The work of the Health and Safety Manager can have a major impact on everyone involved, helping to prevent accidents, injuries, and financial losses.
Steps How to Become
- Obtain a Bachelor's Degree. Most health and safety manager positions require a bachelor's degree in safety management, occupational safety, or a related field. Coursework typically includes safety engineering, industrial hygiene, legal requirements, and disaster management.
- Obtain Relevant Certifications. Obtaining certifications, such as the Certified Safety Professional (CSP) or the Certified Environmental, Health and Safety Trainer (CEHST), is beneficial for health and safety managers. Organizations, like the Board of Certified Safety Professionals, offer certifications for professionals in the safety field.
- Gain Work Experience. Employers typically prefer that candidates have at least four years of experience in safety management before becoming a health and safety manager. Working in roles such as a safety supervisor or coordinator can help aspiring health and safety managers gain the necessary experience.
- Obtain Licensure. Some states require health and safety managers to obtain licensure. Requirements may vary by state, but typically involve passing an exam, having a certain amount of work experience, and completing continuing education.
- Develop Interpersonal Skills. Health and safety managers must be able to communicate effectively with employees, administrators, and other professionals in order to ensure that safety protocols are followed. They must also be able to lead and motivate teams, evaluate risks, and adapt quickly to changing environments.
The role of a Health and Safety Manager is to ensure the safety of employees and customers in the workplace. This can be done through the implementation of effective safety procedures and policies that consider potential risks and hazards. When these policies are properly implemented, organizations are able to reduce the risk of accidents, injuries, or illnesses that can be caused by unsafe working conditions.
The effectiveness of these policies also depends on the capability of the Health and Safety Manager to identify potential risks and hazards and to create effective solutions for avoiding those risks. A successful Health and Safety Manager must be able to identify potential safety issues and address them in a timely manner. they must have the knowledge and experience to develop and implement effective safety policies, protocols, and procedures.
A capable Health and Safety Manager is essential for creating a safe and healthy working environment, as well as reducing the risk of accidents and illnesses in the workplace.
You may want to check Customer Service Manager, Resource Manager, and Product Manager for alternative.
Job Description
- Develop and implement health and safety policies, procedures, and programs to ensure a safe work environment for all employees.
- Monitor and audit compliance with safety legislation and regulations.
- Conduct risk assessments and analyze data to identify potential hazards and recommend solutions.
- Develop safety-related training programs and materials for staff.
- Prepare incident reports and investigate accidents, injuries, and occupational illnesses.
- Establish emergency procedures and coordinate emergency drills.
- Monitor the use of hazardous materials and advise on safe disposal methods.
- Monitor and enforce the use of protective equipment such as hard hats, safety glasses, and respirators.
- Liaise with external agencies such as the Health and Safety Executive to ensure compliance with laws.
- Liaise with insurance companies to ensure adequate coverage for employees.
- Provide advice on occupational health issues such as ergonomics and stress management.
- Maintain records of training, inspections, and other safety activities.
Skills and Competencies to Have
- Knowledge of relevant safety legislation and regulations.
- Ability to identify safety risks and hazards.
- Ability to develop and implement safety policies, procedures and programs.
- Knowledge of safety management systems.
- Strong organizational, communication and leadership skills.
- Ability to conduct safety audits and inspections.
- Ability to develop and deliver safety training programs.
- Ability to investigate accidents and incidents.
- Ability to analyze data and identify trends.
- Ability to develop and manage safety budgets.
- Knowledge of health and wellbeing issues and initiatives.
- Knowledge of risk assessment techniques.
Having a Health and Safety Manager is essential for any organization as it helps to ensure the safety of all employees and customers. Without a Health and Safety Manager, organizations are at risk of experiencing numerous safety issues, including workplace injuries, health concerns, and even fatalities. A Health and Safety Manager is responsible for establishing and maintaining a safe environment by implementing policies, procedures and protocols, as well as by providing training to employees on how to work safely.
The most important skill for a Health and Safety Manager to possess is the ability to identify potential safety hazards, analyze risk factors, and develop strategies for eliminating or mitigating them. A successful Health and Safety Manager also must have strong communication and organizational skills, as well as an understanding of relevant health and safety laws, regulations, and standards. By having a Health and Safety Manager, organizations can ensure that all employees, customers, and other stakeholders are protected from any potential harm.
Supply Chain Manager, Creative Director/Manager, and Project Manager are related jobs you may like.
Frequent Interview Questions
- What experience do you have in health and safety management?
- What strategies do you use to ensure the safety of workers?
- How do you ensure that safety protocols are followed in the workplace?
- How do you implement and measure the effectiveness of safety training programs?
- How do you ensure that health and safety policies are up-to-date and in compliance with relevant regulations?
- How do you investigate and report on accidents or incidents in the workplace?
- How do you manage hazardous materials and hazardous waste in the workplace?
- What methods do you use to identify potential risks in the workplace?
- How do you involve workers in health and safety decisions?
- How do you ensure that safety equipment is maintained and functioning properly?
Common Tools in Industry
- Safe Work Procedure. A document outlining the instructions and procedures for how to safely perform a specific job activity, with an example of a Lock Out/Tag Out procedure.
- Risk Assessment. A process that helps identify, assess and control any potential health and safety risks in the workplace, with an example of a fire risk assessment.
- Accident Investigation. A review of an incident to identify the underlying causes and to make recommendations to prevent similar incidents in the future, with an example of a forklift accident investigation.
- Training Plan. A plan outlining the training needs of all employees, with an example of a hazard communication training plan.
- Personal Protective Equipment (PPE). A document outlining the types of protective gear that employees should wear while performing hazardous tasks, with an example of a fall protection PPE plan.
- Emergency Response Plan. A plan outlining the steps to be taken in the event of an emergency, with an example of a chemical spill response plan.
- Hazard Communication. A system for informing workers about hazardous materials in the workplace, with an example of a hazard communication program.
- Inspection Checklist. A document outlining all aspects of the workplace that must be inspected regularly, with an example of a machine guard inspection checklist.
- Ergonomic Assessment. An evaluation of workplace conditions to ensure safety and comfort for employees, with an example of an office workstation ergonomic assessment.
- Safety Data Sheets (SDS). A document outlining the physical and chemical properties of a hazardous material, with an example of a SDS for a corrosive chemical.
Professional Organizations to Know
- American Society of Safety Professionals
- National Safety Council
- National Institute for Occupational Safety and Health
- American Industrial Hygiene Association
- Institute of Risk Management
- International Safety Management Council
- American Association of Safety Engineers
- Society for Human Resource Management
- International Ergonomics Association
- American Board of Industrial Hygiene
We also have Training Manager, Office Manager, and Brand Manager jobs reports.
Common Important Terms
- Accident Prevention Plan. A written plan that outlines the steps an organization will take to prevent accidents.
- Hazard Analysis. The process of identifying potential hazards in the workplace and determining how to minimize or eliminate them.
- Risk Assessment. The systematic examination of a workplace to identify and evaluate risks to personnel, property, and the environment.
- Emergency Response Plan. A written plan outlining how a business should respond to an emergency situation.
- Occupational Health and Safety. The practice of protecting workers from physical and psychological harm caused by hazardous working conditions.
- Personal Protective Equipment (PPE). Clothing or equipment worn by workers to protect themselves from potential hazards in the workplace.
- Workplace Inspection. A systematic inspection of a workplace to identify hazards, assess risks, and make recommendations for improvement.
Frequently Asked Questions
What qualifications are needed to work as a Health and Safety Manager?
A Health and Safety Manager typically requires a degree in a safety-related field, such as occupational health and safety, environmental health and safety, or engineering, plus professional certification in health and safety.
What tasks are associated with a Health and Safety Manager role?
Responsibilities of a Health and Safety Manager include developing, implementing, and monitoring health and safety programs, conducting risk assessments, providing safety training and education, ensuring compliance with safety regulations, and investigating accidents and incidents.
What is the average salary for a Health and Safety Manager?
The median annual wage for a Health and Safety Manager is $104,590.
What type of work environment does a Health and Safety Manager operate in?
Health and Safety Managers typically work in industrial plants, construction sites, offices, or laboratories.
What duties are expected of a Health and Safety Manager?
Duties typically include developing safety procedures, conducting safety training, enforcing safety regulations, investigating accidents and injuries, creating safety awareness programs, preparing reports, and monitoring safety performance.
What are jobs related with Health and Safety Manager?
- Media Manager
- Maintenance Manager
- Security Manager
- Retail Manager
- Facilities Manager
- Sales Manager
- Marketing Manager
- IT Support Manager
- Data Management Manager
- Business Manager
Web Resources
- Environmental Health & Safety Manager - Unity College unity.edu
- Occupational Health and Safety (OHS) Manager online-distance.ncsu.edu
- Environmental Health and Safety Manager: Job Description and ¦ publichealth.tulane.edu
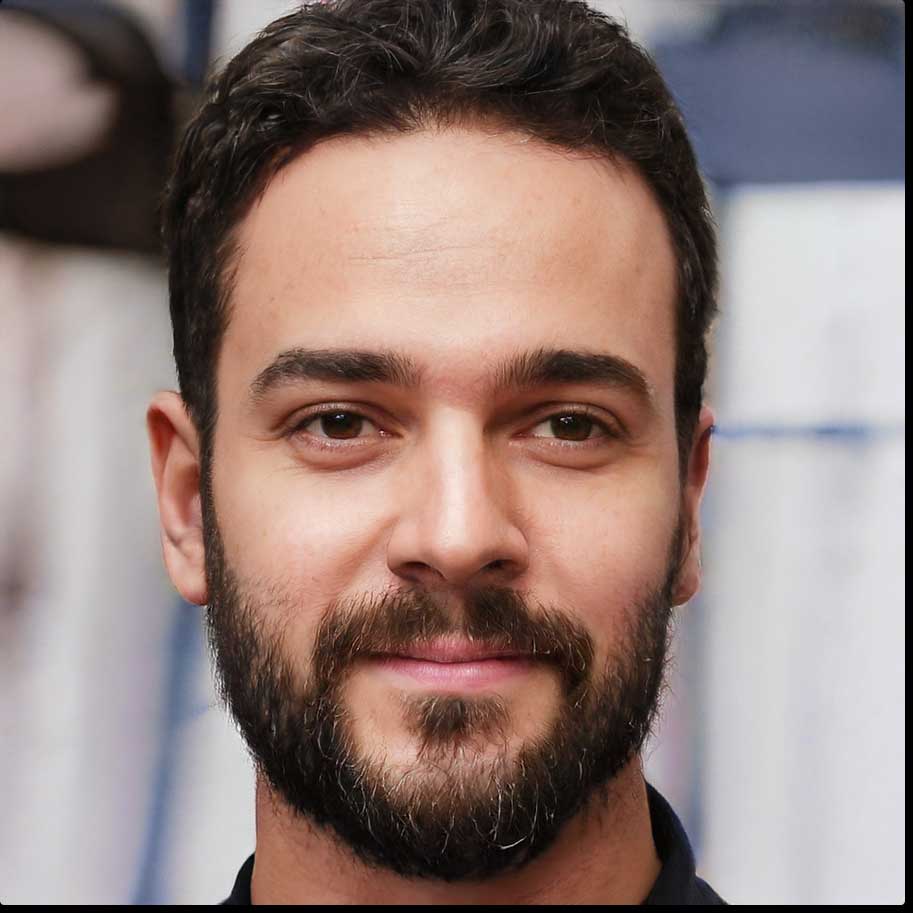