How to Be Fabric Welder - Job Description, Skills, and Interview Questions
The use of fabric welders has become increasingly popular in many industrial and commercial applications. As a result, there has been a rise in the demand for skilled fabric welders. Fabric welding is a process that uses heat to fuse two pieces of fabric together, creating a strong and permanent bond.
It is often used to create waterproof seals on outdoor gear and to join specialized fabrics used in the manufacture of medical devices and other products. Fabric welders need to be highly trained and skilled in order to properly operate the equipment, as incorrect use can damage the fabric and weaken the bond. they must have a thorough understanding of the type of material being welded, as each material requires different welding techniques and parameters to achieve optimal results.
Steps How to Become
- Earn a High School Diploma. Fabric welders typically need to have a high school diploma or equivalent. If you dont have one, consider taking classes at your local community college or online to help you get your diploma.
- Get Training. To become a fabric welder, you will need to complete training in welding and fabricating. This can be done through a trade school or apprenticeship program.
- Get Certified. Obtaining certification as a fabric welder is voluntary, but it can help you to stand out among other applicants when looking for work. You can obtain certification through organizations like the American Welding Society or the Fabricators and Manufacturers Association.
- Obtain Work Experience. Once you have completed your training, you should look for opportunities to gain work experience in fabric welding. This could include internships, apprenticeships, or even volunteer work.
- Apply for Jobs. Once you have the necessary qualifications, you can begin applying for jobs as a fabric welder. Look for job listings in your local area or online job boards.
- Continue Your Education. Fabric welding is a constantly evolving field, so continuing your education is key to staying abreast of the latest trends and technologies. Consider taking classes in welding or fabricating to keep up with the changing industry.
The ability to stay updated and capable as a fabric welder is paramount for success in the field. Keeping up to date with industry trends, technology advancements, and safety protocols is essential to staying competitive in the job market. Furthermore, investing in the right tools and equipment, as well as taking continuing education classes to expand ones skill set and knowledge base, can make all the difference in the quality of work produced.
staying abreast of ever-evolving welding processes and methods is critical for staying ahead of industry standards and best practices. an up-to-date and capable fabric welder is an invaluable asset to any team or organization.
You may want to check Fabric Sewer, Fabric Planner, and Fabric Cutter for alternative.
Job Description
- Read and interpret welding plans, sketches, and blueprints to determine the specific welding requirements.
- Operate welding equipment including arc welders, spot welders, gas welders and robotic welding systems.
- Set up and operate fabric welding machines to join or cut fabric pieces together.
- Monitor welding equipment to ensure proper operation, and make necessary adjustments as needed.
- Inspect welds for accuracy and make adjustments as needed.
- Maintain accurate records of welding production and machine maintenance.
- Follow safety protocols when operating welding equipment.
- Troubleshoot and repair fabric welding machines and associated equipment.
- Perform routine maintenance and cleaning of welding equipment.
- Work with a team of fabric welders to meet production goals.
Skills and Competencies to Have
- Ability to read and interpret blueprints and technical specifications to determine weld requirements.
- Knowledge of welding processes, including resistance welding, spot welding, and MIG welding.
- Ability to operate welding equipment and set up welding parameters.
- Understanding of welding safety procedures.
- Ability to select and use appropriate welding tools, such as clamps, jigs, and positioning tools.
- Knowledge of metallurgy principles and their application in welding processes.
- Ability to inspect own work for quality assurance.
- Proficiency in using basic hand tools and measuring instruments.
- Ability to work from verbal or written instructions.
- Good manual dexterity and hand-eye coordination.
Being a successful fabric welder requires a variety of skills, but the most important one is the ability to accurately read and interpret blueprints. Without this skill, fabric welders would not be able to execute the precise measurements and cuts needed to create and maintain quality products. In addition, fabric welders must understand how to use a variety of tools and equipment to ensure their welding meets industry standards.
They must also be able to use different types of welding techniques, including MIG and TIG welding, to properly join metal pieces together. Finally, fabric welders must have strong communication and problem-solving skills in order to work with other team members, clients, and supervisors. These skills are all essential to the success of any fabric welder and allow them to meet the demands of the job and produce high-quality results.
Fabric Inspector, Fabric Printer, and Fabric Designer are related jobs you may like.
Frequent Interview Questions
- What experience do you have working with fabric welding?
- How familiar are you with the welding tools and equipment used in fabric welding?
- What safety precautions do you take while fabric welding?
- How do you troubleshoot when fabric welding problems arise?
- How do you ensure accuracy when fabric welding?
- What challenges have you faced while fabric welding?
- Describe how you handle tight deadlines when fabric welding.
- What techniques do you use to minimize the risk of fire or injury while fabric welding?
- Describe your experience working with a variety of fabrics and materials for fabric welding.
- How would you go about teaching someone else how to fabric weld?
Common Tools in Industry
- Hot Air Welding Gun. A tool used to join two pieces of fabric together using heated air. (Example: A hot air welding gun is commonly used to create waterproof seams on raincoats. )
- Ultrasonic Welder. A tool that uses high-frequency sound waves to join two pieces of fabric together. (Example: An ultrasonic welder is often used to fuse together different types of synthetic fabrics. )
- Heat Sealer. A tool that uses pressure and heat to seal two pieces of fabric together. (Example: A heat sealer is often used to weld layers of plastic film together. )
- Sewing Machine. A tool that uses thread and a needle to stitch two pieces of fabric together. (Example: A sewing machine is used to create seams on clothing items. )
- Fusion Welder. A tool that uses heat, pressure, and chemicals to bond two pieces of fabric together. (Example: A fusion welder is often used to fuse fabrics that cannot be joined using hot air or ultrasonic welding techniques. )
Professional Organizations to Know
- American Welding Society (AWS)
- Fabricators & Manufacturers Association International (FMA)
- Association of Welding Distributors (AWD)
- Canadian Welding Association (CWA)
- British Institute of Non-Destructive Testing (BINDT)
- International Institute of Welding (IIW)
- International Welding Technologists (IWT)
- American Society of Mechanical Engineers (ASME)
- Canadian Institute of Welding (CIW)
- European Federation for Welding, Joining and Cutting (EWF)
We also have Fabric Engineer, Fabric Finisher, and Fabric Technician jobs reports.
Common Important Terms
- Hot Air Welder. A hot air welder is a device used to heat and bond pieces of material together using hot air. It is commonly used in the fabrication of fabrics and textiles.
- Ultrasonic Welding. Ultrasonic welding is a process by which two pieces of material are joined together by applying ultrasonic energy to the joint between them. It is often used in the production of clothing and other similar items.
- Heat Sealing. Heat sealing is a process by which two pieces of material are joined together by heat generated from an electric heating element. It is commonly used in the manufacturing of bags and other packaging materials.
- Radio Frequency Welding. Radio frequency welding is a process by which two pieces of material are joined together by radio waves. It is used in the production of many types of products, including medical devices, automotive parts, and consumer products.
- High Frequency Welding. High frequency welding is a process by which two pieces of material are joined together using high-frequency alternating current. This type of welding is often used in the production of plastics and other materials that require high-strength bonds.
Frequently Asked Questions
What is Fabric Welder?
Fabric Welder is a professional-grade fabric bonding solution that permanently bonds fabrics together. It is a lightweight, non-toxic and odorless adhesive that is ideal for use in a variety of applications, including clothing, handbags, upholstery, and more.
What types of fabrics can be bonded with Fabric Welder?
Fabric Welder can be used to bond a wide variety of fabrics, including cotton, wool, canvas, denim, faux leather, vinyl, and more.
How long does Fabric Welder take to dry?
Fabric Welder dries quickly and typically takes about 10 minutes to achieve a permanent bond.
Is Fabric Welder toxic?
No, Fabric Welder is non-toxic and odorless. It does not contain any hazardous chemicals or solvents.
Does Fabric Welder require any special equipment?
No, Fabric Welder can be applied by hand with no special equipment needed.
What are jobs related with Fabric Welder?
- Fabric Buyer
- Fabric Handler
- Fabric Analyst
- Fabric Joiner
- Fabricator
- Fabric Dyer
- Fabric Supervisor
- Fabric Maker
- Fabric Coordinator
Web Resources
- (PDF) Fabricator & Welder [Cur] | Nabeeha Ali - Academia.edu www.academia.edu
- Fabricator/Welder | Degree Search | ASU degrees.apps.asu.edu
- How to Become a Welder? (Complete Guide) | UEI College www.uei.edu
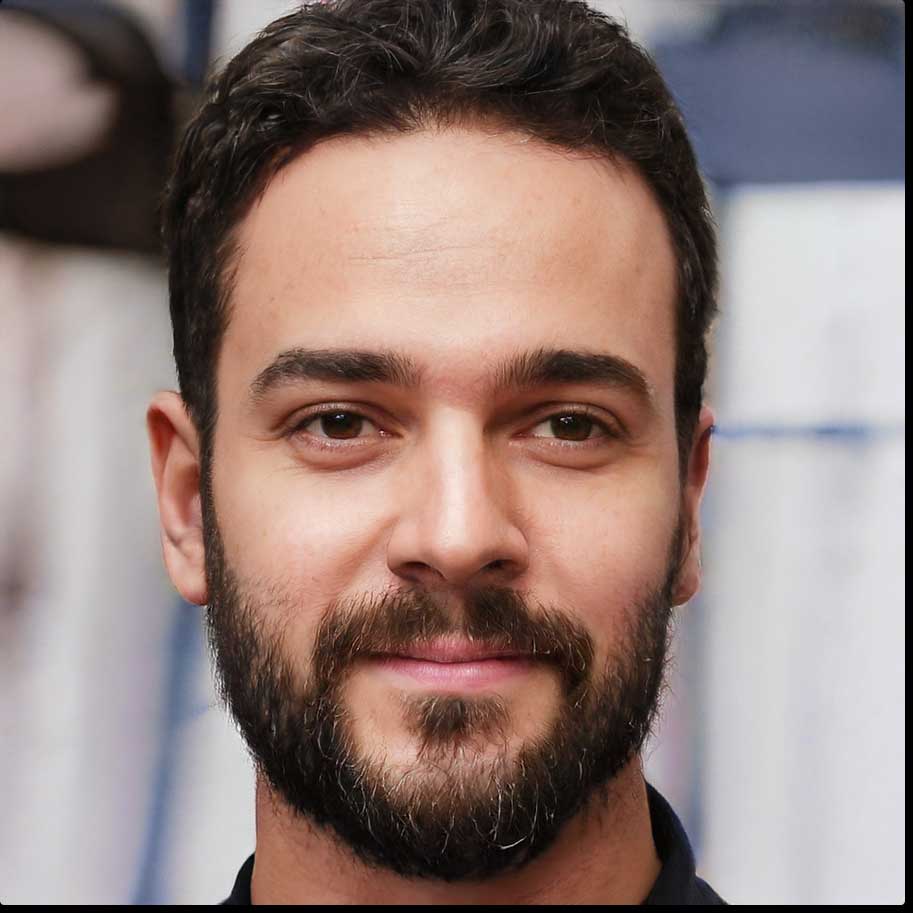