How to Be Life Cycle Cost Engineer - Job Description, Skills, and Interview Questions
The life cycle cost engineer plays an important role in the overall cost-efficiency of a project. They are responsible for evaluating the costs associated with the development, acquisition, operation, and disposal of a project over its entire life cycle. This includes the costs of materials, labor, and other resources.
By accurately forecasting the costs associated with each stage of the project, the life cycle cost engineer helps to ensure that projects are completed on-time and within budget. This can lead to significant savings for the organization and its stakeholders in the long run, as well as ensure the successful completion of the project.
Steps How to Become
- Earn a Bachelor's Degree. Begin by earning a bachelor's degree in engineering, architecture, or economics. Relevant courses include accounting, statistics, and mathematics.
- Obtain a Master's Degree. Consider obtaining a master's degree in engineering, architecture, or economics to further enhance your career prospects.
- Get Certified. Consider becoming a certified life cycle cost engineer. The Association for the Advancement of Cost Engineering (AACE) offers a certification program for life cycle cost engineers.
- Participate in Professional Organizations. Participate in professional organizations such as the American Society of Civil Engineers (ASCE) or the American Institute of Architects (AIA) to stay up to date on the latest trends and technologies.
- Obtain Professional Experience. Obtain professional experience through internships or part-time work with engineering or architecture firms.
- Develop Expertise. Develop expertise in software such as Microsoft Excel and other computer aided design programs to help you perform your duties as a life cycle cost engineer.
- Stay Current. Stay current on industry trends and technologies by attending conferences and workshops.
Cycle Cost Engineers are highly skilled and competent professionals who are responsible for analyzing the entire life cycle cost of a project. They analyze the financial impact of the project, from initial development costs to end-of-life disposal costs. They use a variety of techniques, such as cost-benefit analysis, cost estimation, and risk assessment, to identify the most cost-effective solutions for a given project.
By understanding the full cost of a project, Cycle Cost Engineers can help organizations make informed decisions on how to best allocate their resources. This helps to ensure that projects are completed on time and within budget, while still meeting all applicable regulations and standards. Cycle Cost Engineers help organizations maximize their return on investment and ensure successful project completion.
You may want to check Life Sciences Product Manager, Life Science Regulatory Affairs Specialist, and Life Sciences Quality Assurance Auditor for alternative.
Job Description
- Develop and maintain life cycle cost models and databases.
- Utilize data analysis techniques, such as regression analysis, to assess the cost of ownership for various equipment and systems.
- Research and analyze capital and operational costs associated with acquiring, owning, and operating systems.
- Analyze the financial impact of system design changes and recommend solutions to reduce cost.
- Prepare cost benefit analyses and life cycle cost reports.
- Develop methods to track and analyze cost trends over time.
- Evaluate contracts and proposals to identify cost savings opportunities.
- Coordinate with vendors to ensure that pricing is fair and reasonable.
- Develop and maintain cost estimating tools and models.
- Consult with project managers to ensure that costs are identified in the project plans and tracked throughout the life cycle.
Skills and Competencies to Have
- Knowledge of engineering principles, methods, and practices.
- Ability to interpret financial statements, budgets and cost data.
- Knowledge of the principles and practices of life cycle cost analysis.
- Ability to develop and analyze cost models to assess life cycle costs.
- Ability to effectively communicate complex financial information.
- Ability to work collaboratively with other engineers, financial professionals, and project stakeholders.
- Knowledge of the principles of project management and scheduling.
- Knowledge of engineering design processes, project management techniques, and technical writing skills.
- Knowledge of computer software programs such as MS Excel and MS Project.
- Ability to effectively manage multiple projects and prioritize tasks.
The life cycle cost engineer is a vital role in any engineering project. They are responsible for analyzing the financial impact of an engineering system or product over its entire life cycle. The life cycle cost engineer must possess an extensive knowledge of engineering principles and processes, economic principles, and cost-benefit analysis.
they must be highly proficient in risk assessment and management, as well as data analysis and modeling. Through their expertise, life cycle cost engineers are able to identify potential issues and risks, recommend solutions and best practices, and provide guidance to team members to ensure project success. By using their skills and knowledge, life cycle cost engineers help reduce costs, improve efficiency, and maximize return on investment for the organization.
their expertise is essential to the success of any engineering project.
Life Science Researcher, Life Skills Trainer, and Life Science Technician are related jobs you may like.
Frequent Interview Questions
- What experience do you have with life cycle cost engineering?
- How familiar are you with the different life cycle cost models?
- What strategies do you use to accurately assess life cycle costs?
- How do you prioritize cost-effectiveness when evaluating life cycle cost options?
- How do you identify and mitigate risk associated with life cycle cost decisions?
- What techniques do you use to maximize return on investment when evaluating life cycle costs?
- How do you effectively communicate and collaborate with stakeholders on life cycle cost evaluations?
- Can you describe a situation where you successfully identified and implemented cost savings through a life cycle cost analysis?
- How do you ensure that life cycle cost analyses are comprehensive and accurate?
- What processes do you have in place to track and report the progress of a life cycle cost analysis?
Common Tools in Industry
- Life Cycle Cost Analysis Software. Used to analyze the total cost of ownership for products, services, and projects. (Example: Life Cycle Cost Analyzer)
- Life Cycle Cost Estimating Tool. Used to estimate future costs and identify cost savings opportunities. (Example: Life Cycle Cost Estimator)
- Financial Modeling Software. Used to develop financial models to help analyze and manage investments. (Example: Microsoft Excel)
- Risk Assessment Software. Used to identify potential risks and develop strategies to mitigate them. (Example: Risk Management Tool)
- Cost Estimation Software. Used to create cost estimates for specific projects or products. (Example: Cost Estimation Tool)
- Life Cycle Assessment Software. Used to evaluate the environmental impact of products, services, and projects. (Example: Life Cycle Assessment Tool)
- Project Management Software. Used to plan, execute, and manage projects. (Example: Microsoft Project)
- Decision Support Software. Used to analyze large amounts of data and provide insight into complex decisions. (Example: IBM Watson Analytics)
Professional Organizations to Know
- Institute of Asset Management (IAM)
- International Cost Engineering Council (ICEC)
- Society of Cost Estimating and Analysis (SCEA)
- International Risk Management Institute (IRMI)
- Project Management Institute (PMI)
- Association for the Advancement of Cost Engineering International (AACEI)
- American Society of Professional Estimators (ASPE)
- Association for the Advancement of Cost Engineering (AACE)
- International Association of Engineering and Construction Cost Managers (IAECCM)
- National Institute of Standards and Technology (NIST)
We also have Life Management Counselor, Life Support Technician, and Life Scientist jobs reports.
Common Important Terms
- Life Cycle Cost Analysis (LCCA). The process of analyzing the total cost of ownership over the entire life of an asset or system. It takes into account the initial cost, operation and maintenance costs, disposal costs, and any other relevant cost factors.
- Life Cycle Cost Model (LCCM). A structured mathematical model designed to calculate the total cost of ownership over the entire life of an asset or system.
- Cost-Benefit Analysis (CBA). A technique used to compare the total expected costs of a project with its expected benefits to determine its value for investment.
- Risk Analysis. A systematic process of evaluating potential risks and their potential impacts to identify and prioritize risks for management attention.
- Reliability Engineering. The practice of designing and managing systems so that they are more reliable and less likely to fail.
- Value Engineering. The practice of examining a system or product to determine its value to the customer in order to reduce cost and/or improve quality.
- Total Cost of Ownership (TCO). The total cost of purchasing, using, and disposing of an asset or system over its lifetime.
- Cost Estimation. The process of predicting the cost of a project or system based on information available at the time of estimation.
Frequently Asked Questions
What is Life Cycle Cost Engineering?
Life Cycle Cost Engineering is a form of engineering that considers the total cost of ownership of a product or system over its entire life cycle, from initial construction to end-of-life disposal. It takes into account not only the cost of producing, operating, and maintaining the product or system, but also the social and environmental impacts.
What are the key components of Life Cycle Cost Engineering?
The key components of Life Cycle Cost Engineering are cost analysis, life cycle assessment, and risk analysis. Cost analysis includes estimating the initial cost of materials and labor to produce the product or system, as well as ongoing costs such as energy usage, maintenance and operations. Life cycle assessment involves understanding the environmental impacts of the product or system throughout its life cycle. Risk analysis evaluates the probability and potential consequences of any risks associated with the product or system.
What are the benefits of Life Cycle Cost Engineering?
The benefits of Life Cycle Cost Engineering are numerous. It can help reduce costs by considering all potential costs associated with a product or system over its lifespan, and can help identify potential savings from more efficient design or operation. It can also help identify potential environmental impacts, allowing for better informed decisions about product or system design. Finally, it can help reduce risk by assessing potential risks associated with a product or system.
What qualifications do Life Cycle Cost Engineers need?
Life Cycle Cost Engineers need a degree in engineering, economics, or a related field, as well as experience in cost analysis, life cycle assessment, and risk analysis. They must also have strong analytical skills and be able to interpret complex data.
What is the average salary for a Life Cycle Cost Engineer?
The average salary for a Life Cycle Cost Engineer ranges from $60,000 to $90,000 per year, depending on experience and qualifications.
What are jobs related with Life Cycle Cost Engineer?
- Life Safety Code Consultant
- Life Skills Trainer and Facilitator
- Lifeguard
- Life Cycle Logistics Specialist
- Life Sciences Patent Attorney
- Life Scientist, Senior
- Life Skills Manager
- Life Cycle Engineer
- Life Skills Instructor
- Life Sciences Regulatory Affairs Manager
Web Resources
- Life Cycle Costing for Engineers - academia.edu www.academia.edu
- Life Cycle Costing | Sustainability at Harvard green.harvard.edu
- Life Cycle Costing | Harvard Energy & Facilities www.energyandfacilities.harvard.edu
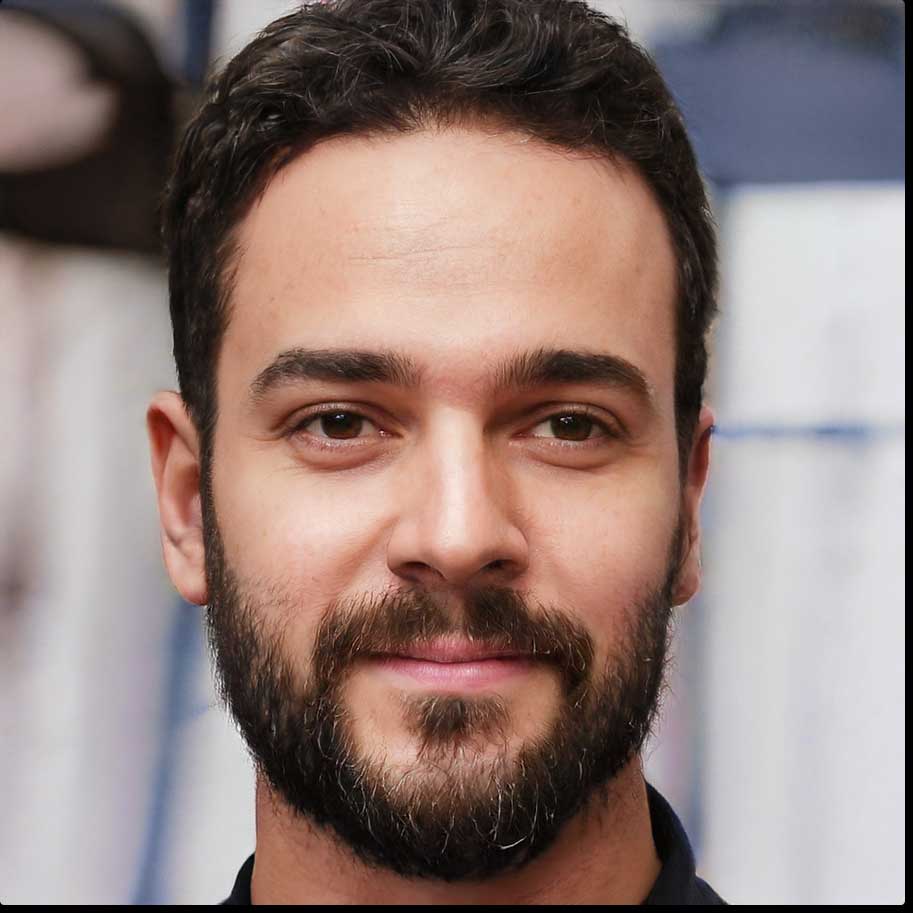