How to Be Garage Builder - Job Description, Skills, and Interview Questions
The need for garage builders has increased dramatically over the past few years due to the rise of vehicle ownership and the demand for additional storage space. As a result, builders have been called upon to construct garages to meet this growing demand. Without garages, many homes would be unable to accommodate the increase in cars and other items that require secure storage.
Garage builders provide an essential service by constructing garages that meet the needs of homeowners, including customizing the size, style, and features of the garage to make it fit perfectly into the area it is being built. They also ensure that the garage is built safely and is up to code with all necessary permits and regulations. In addition, garage builders can provide advice on the best materials, designs, and features to suit the homeowner's needs.
Steps How to Become
- Research the Building Regulations. Before you begin building a garage, you should familiarize yourself with the building regulations in your area. These regulations will dictate the size, location, and materials of your garage.
- Obtain Permits. Most states and localities require permits in order to build a garage. Contact your local building authority to find out what permits you need and how to obtain them.
- Design Your Garage. Once you know the requirements for your garage, it's time to start designing it. You can work with a contractor or use software to design the garage. Make sure to consider the materials you'll use, the size you need, and any other features you'd like to include.
- Purchase Materials. After you've designed your garage, it's time to purchase the materials necessary to build it. This includes lumber, nails, screws, concrete, siding, and any other materials you may need.
- Clear the Area. Before you begin building, you'll need to clear the area where the garage will be located. Remove any debris or other obstructions that could interfere with the construction of your garage.
- Build the Frame. Once the area is clear, it's time to begin building the frame for your garage. Start with the walls, then move on to the roof and flooring. Make sure to follow your plans exactly when constructing the frame.
- Install Doors and Windows. Once the frame is complete, you can install the doors and windows. Make sure to measure twice and cut once to ensure that everything fits properly.
- Add Siding and Trim. After the doors and windows are installed, it's time to add the siding and trim. This will help protect your garage from the elements and give it a finished look.
- Paint. Once the siding and trim are installed, it's time to paint your garage. Choose a paint color that complements your home and provides an attractive contrast with the siding and trim.
- Install Electrical Components. If you plan to use electricity in your garage, you'll need to install electrical components such as outlets, switches, and lights. Be sure to hire a professional electrician to handle this task if you're not comfortable with electrical work.
- Finalize Details. Once all of the major components of your garage are installed, it's time to finish up the details. This includes items such as shelving, storage cabinets, racking systems, and anything else that will make your garage more functional and organized.
- Enjoy Your Garage. Now that your garage is complete, it's time to enjoy it! Whether it's for storing tools and supplies or parking your vehicles, your new garage will provide years of convenience and enjoyment.
Staying ahead and qualified in the garage building industry requires dedication to learning new skills, staying up to date with the latest trends, and gaining certifications. Keeping on top of industry news and staying informed of new technologies is essential to staying competitive. Learning new skills such as welding, carpentry, and masonry can also help.
Having certifications can also be beneficial as they show potential clients that you have the knowledge and experience necessary to do the job. Finally, networking with other professionals in the industry can help you stay ahead and keep up with the latest advancements in the field. By taking the time to invest in these areas, you can ensure you stay ahead and qualified in the garage building industry.
You may want to check Fireplace Installer/Builder, Bricklayer Builder, and Structural Steel Building Erector/Builder for alternative.
Job Description
- Carpenter: Responsible for measuring and cutting lumber, assembling frames, and installing doors and windows.
- Drywall Installer: Responsible for hanging and finishing drywall, including taping, mudding, sanding, and painting.
- Electrician: Responsible for installing wiring, outlets, circuit breakers, and other electrical components.
- Plumber: Responsible for installing pipes, fixtures, and other plumbing components.
- Concrete Finisher: Responsible for pouring and finishing concrete floors, walls, and other surfaces.
- Painter: Responsible for preparing surfaces and applying paint and other finishes.
- Insulation Installer: Responsible for installing insulation in walls, floors, ceilings, and other areas.
- Roofing Installer: Responsible for installing roofing materials such as shingles, tiles, and metal panels.
Skills and Competencies to Have
- Construction skills: Ability to read blueprints and build structures according to safety regulations and building codes.
- Carpentry: Ability to cut, shape, join and fasten wood, metal and other materials to create structures.
- Electrical knowledge: Knowledge of electrical wiring, lighting, and the National Electrical Code.
- Plumbing knowledge: Knowledge of plumbing systems and their components, including pipes, fittings, and valves.
- Drywall installation: Knowledge of drywall installation techniques and materials.
- Painting: Knowledge of painting techniques and surface preparation.
- Roofing: Knowledge of different types of roofing materials and their installation techniques.
- Masonry: Ability to lay brick, stone and other masonry materials to create structures.
- Concrete work: Knowledge of concrete mixing and pouring techniques.
- Finishing work: Knowledge of finishing techniques, including trim installation and staining/painting.
Having a good eye for detail is an essential skill when it comes to being a successful garage builder. Without the ability to pay attention to the finer details, one may end up with a garage that does not meet safety standards or other requirements. Poorly made garages can also be more expensive to repair and maintain, costing more money in the long run.
To ensure quality construction, proper planning and preparation are also necessary. This includes understanding the materials and tools needed for the job, as well as having a proper blueprint to work from. the ability to read and interpret plans is also important for any successful garage builder.
By having the necessary skills and tools, a builder can create a safe and secure garage that will last for years to come.
Concrete Builder, Green Building Consultant/Builder, and Structural Steel Bridge Builder are related jobs you may like.
Frequent Interview Questions
- What experience do you have in building garages?
- What is your process for working with clients to design and build a garage?
- How do you handle changes to a project during construction?
- What safety protocols do you follow when building garages?
- What kind of materials do you use for building garages?
- How do you stay up to date on the latest technologies, tools, and techniques for garage building?
- How do you ensure that the finished product meets the clients expectations?
- What challenges have you faced when building garages in the past?
- Describe your approach to problem solving when issues arise during a garage building project.
- What do you believe sets you apart from other garage builders?
Common Tools in Industry
- Hammer . Used for pounding nails into wood, (eg: for constructing a fence).
- Tape Measure . Used for measuring distances, (eg: for determining the size of a garage).
- Circular Saw . Used for cutting wood, (eg: for creating panels for the garage walls).
- Drill . Used for creating holes in wood, (eg: for attaching panels to the framework).
- Level . Used for ensuring surfaces are flat, (eg: for making sure the floor is even).
- Paint Brushes . Used for painting surfaces, (eg: for painting the walls of the garage).
- Screw Drivers . Used for tightening and loosening screws, (eg: for installing hinges on the doors).
- Ladder . Used to access higher areas, (eg: for installing the roof of the garage).
Professional Organizations to Know
- American Institute of Architects (AIA)
- American Society of Civil Engineers (ASCE)
- Associated General Contractors of America (AGC)
- National Association of Home Builders (NAHB)
- National Association of the Remodeling Industry (NARI)
- National Council of Structural Engineers Associations (NCSEA)
- International Code Council (ICC)
- American Subcontractors Association (ASA)
- International Masonry Institute (IMI)
- American Institute of Steel Construction (AISC)
We also have Construction Builder, Concrete Pool Deck Builder, and Mobile Home Builder jobs reports.
Common Important Terms
- Framing. The construction of the basic structure of a building or other structure, typically using wood or metal frames.
- Foundation. The base of a building or structure, typically below ground level, which supports the rest of the structure.
- Concrete. A hard, strong construction material made from a mixture of cement, sand, gravel, and water.
- Masonry. The construction of structures from individual units, typically brick, stone, or concrete blocks.
- Drywall. A type of wall paneling made from sheets of gypsum plaster mounted on a metal frame.
- Roofing. The covering of a building's roof with tiles, shingles, or other materials.
- Siding. The material used to cover the external walls of a building, typically wood or vinyl.
- Insulation. Materials used to reduce heat transfer in a building, such as fiberglass, foam, and cellulose.
- Plumbing. The installation and maintenance of pipes, fixtures, and other apparatus for the distribution of water for drinking, heating, and washing in a structure.
- Electrical Wiring. The installation and maintenance of electrical wiring and other related equipment in a building or structure.
Frequently Asked Questions
What is a Garage Builder?
A Garage Builder is a software program designed to help you design and build a garage for your home. It provides tools to plan, organize, and create a customized garage that meets all of your needs.
How do I get started with Garage Builder?
To get started with Garage Builder, you'll need to purchase the software and then download it onto your computer. Once it's installed, you can use the tools to plan out your dream garage.
What kind of features does Garage Builder offer?
Garage Builder offers a variety of features such as 3D modeling, customizable templates, a materials list generator, and more. It also allows you to save your designs and collaborate with other users.
How much does Garage Builder cost?
The cost of Garage Builder depends on the version you purchase. The standard version is $99.95, while the Pro version is $199.95.
Is there a free trial version of Garage Builder?
Yes, Garage Builder offers a free 14-day trial so that you can test out the software before making a purchase.
What are jobs related with Garage Builder?
- Shed and Outbuilding Builder
- Solar Panel Builder
- Boat Dock and Ramp Builder
- Pool Builder
- Concrete Formwork Builder
- Master Builder
- Prefabricated Building Builder
- Project Builder
- Swimming Pool Construction/Builder
- Masonry Builder
Web Resources
- The Garage | Entrepreneurship@DU | Daniels College of Business daniels.du.edu
- Builder Education Series | New Hampshire Home Builders www.builder-edu.com
- Garages | Mississippi State University Extension Service extension.msstate.edu
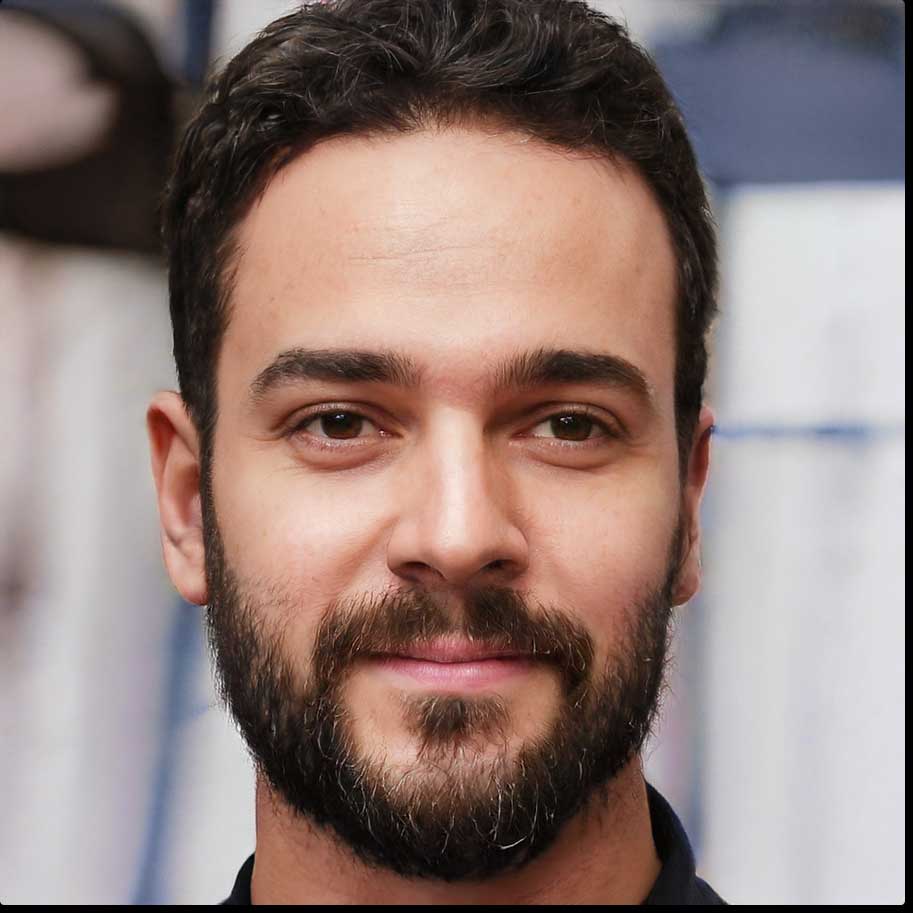