How to Be Continuous Improvement Advisor - Job Description, Skills, and Interview Questions
The introduction of Continuous Improvement Advisors has had a significant impact on businesses. These professionals are responsible for helping organizations identify and implement process improvements, which can lead to increased efficiency, reduced costs, and improved customer service. By assessing existing workflows and developing new solutions, they can help businesses maximize resources, reduce waste, and identify new opportunities for growth.
Continuous Improvement Advisors are often able to create improved systems to streamline operations, increase employee engagement, promote collaboration, and strengthen organizational culture. their role is instrumental in helping businesses remain competitive and successful in today's changing marketplace.
Steps How to Become
- Earn a Bachelor's Degree. To become a Continuous Improvement Advisor, you will need to have at least a bachelor's degree in business management, engineering, operations management, or a related field.
- Gain Relevant Work Experience. Once you have your degree in hand, it is important to gain relevant work experience. This could include working as a consultant in a particular industry or as a continuous improvement specialist for a company.
- Get Certified. Obtaining a professional certification in Lean Six Sigma or Lean Manufacturing is beneficial for those seeking a career in this field. There are several certifications available, so it is important to do your research and choose the one that is best suited to your specific needs and interests.
- Develop Your Skills. In order to be successful as a Continuous Improvement Advisor, you must have excellent problem-solving skills, communication skills, and be able to think strategically. Developing these skills will help you be successful in this role.
- Network. Networking is an important part of any career. Connecting with other professionals in the field and attending conferences and seminars can help you stay up to date on the latest trends and practices, as well as give you the opportunity to make valuable connections.
Continuous improvement is the process of regularly reviewing, assessing, and adjusting processes, procedures, and products in order to optimize performance. It is a key factor in the success of any organization, as it enables them to stay competitive and ensure they are providing the highest quality service or product. The process can be broken down into two categories: ideal and capable.
Ideal refers to the desired outcome of the process, while capable refers to the current level of performance. When organizations invest in continuous improvement initiatives, they are able to identify areas where they can improve, and make necessary changes to ensure they are meeting their goals. This in turn can lead to increased efficiency, improved customer satisfaction, and cost savings.
You may want to check Workforce Planning and Talent Acquisition Advisory Services, Retirement Advisor, and Career Advisor for alternative.
Job Description
- Develop and implement operational excellence strategies and processes to improve performance, strengthen customer satisfaction and increase profitability.
- Analyze and recommend changes to current systems, processes and operations to foster efficiency and cost savings.
- Lead cross-functional teams to identify opportunities for process optimization and improvement.
- Facilitate the design, implementation and monitoring of Lean Six Sigma initiatives.
- Develop and deliver training programs to support continuous improvement initiatives.
- Monitor process performance metrics, analyze trends and make recommendations for improvement.
- Leverage relevant technology to enable and streamline continuous improvement efforts.
- Conduct root cause analysis to identify potential areas of operational improvement.
- Generate performance reports to inform management of process improvement efforts and impact.
- Collaborate with stakeholders to define, document and implement process changes.
Skills and Competencies to Have
- Analytical and Problem Solving Skills
- Strategic Planning and Execution
- Process Improvement Methodologies
- Change Management
- Data Analysis and Interpretation
- Project Management
- Interpersonal and Communication Skills
- Lean and Six Sigma Principles
- Facilitation and Training
- Quality Assurance and Control
- Organizational Development
- Business Acumen
- Risk Mitigation Strategies
- Performance Measurement and Metrics
- Team Building and Leadership
Continuous Improvement Advisors are highly sought after in many industries due to their ability to identify and implement process improvement initiatives. This requires a variety of skills, but the most important skill for a Continuous Improvement Advisor to have is the ability to think analytically and strategically. Analytical thinking allows them to break down complex processes into smaller components, while strategic thinking allows them to consider the bigger picture and develop creative solutions.
they must have a deep understanding of the organization's processes and systems, as well as the ability to effectively communicate and collaborate with multiple stakeholders. By having these skills, a Continuous Improvement Advisor can analyze the existing system, identify areas for improvement, develop strategies for implementation, and then effectively communicate these changes to all stakeholders within the organization. The result is improved productivity, efficiency, and cost savings for the organization.
Mergers and Acquisitions Advisory Services, Innovation Advisor, and IT Infrastructure and Operations Advisor are related jobs you may like.
Frequent Interview Questions
- How have you helped to improve processes in the past that have resulted in significant cost savings?
- Describe a challenging process improvement project you have worked on and how you overcame it.
- What techniques do you use to identify process improvement opportunities?
- What techniques do you use to measure and evaluate the success of process improvement initiatives?
- Have you ever led a major process improvement project? If so, what were the results?
- How do you ensure that all stakeholders are involved in the process improvement process?
- How do you stay up-to-date with the latest trends in continuous improvement?
- What strategies do you use to help employees embrace change and adopt new processes?
- What are your thoughts on using data analysis to identify and address process improvement issues?
- How do you balance the need for quick process improvement changes with the need for sustained, long-term improvements?
Common Tools in Industry
- Lean Sigma. A process improvement methodology that combines Lean methodology and Six Sigma to reduce waste, improve quality, and increase customer satisfaction. (eg: Using Lean Sigma to reduce manufacturing cycle time by 20%)
- Kaizen. A continuous improvement technique that encourages employees to identify and present ideas for improvement. (eg: Implementing Kaizen to reduce scrap and rework)
- Value Stream Mapping. A tool used to visualize, analyze, and optimize the flow of materials and information across the entire value stream. (eg: Developing a Value Stream Map to reduce lead times in the supply chain)
- Six Sigma. A set of techniques used to improve processes and reduce defects. (eg: Applying Six Sigma to reduce customer complaint resolution time)
- Root Cause Analysis. A method of troubleshooting that helps to identify the underlying cause of a problem or issue. (eg: Utilizing Root Cause Analysis to reduce downtime in production)
- Process Mapping. A method of documenting the flow of work in a process, which can help identify areas for improvement. (eg: Drawing a Process Map to identify bottlenecks in order processing)
- Process Improvement Plan. A tool used to create action plans for making improvements. (eg: Developing a Process Improvement Plan to improve the accuracy of sales forecasts)
Professional Organizations to Know
- Association for Operations Management (APICS)
- International Association for Six Sigma Certification (IASSC)
- Lean Enterprise Institute
- American Society for Quality (ASQ)
- International Quality Federation (IQF)
- Project Management Institute (PMI)
- Institute of Industrial and Systems Engineers (IISE)
- International Organization for Standardization (ISO)
- International Institute of Business Analysis (IIBA)
- Manufacturing Skill Standards Council (MSSC)
We also have Customer Service Advisor, Technology Advisor, and Procurement Advisor jobs reports.
Common Important Terms
- Kaizen. A Japanese business philosophy centered around continuous improvement and striving for excellence.
- Lean Manufacturing. A system of production that maximizes efficiency by reducing waste and increasing customer value.
- Six Sigma. A set of tools and methods used to improve processes, reduce variation, and increase customer satisfaction.
- Quality Management. A set of practices and processes aimed at ensuring the quality of products and services.
- Process Improvement. A systematic approach to improving processes and procedures, with the goal of increasing efficiency and effectiveness.
- Value Stream Mapping. A tool used to analyze and improve a process by understanding its inputs, outputs, and steps.
- Root Cause Analysis. A method used to identify the underlying causes of a problem in order to take corrective action.
- Benchmarking. The practice of comparing performance against other organizations or entities in order to improve efficiency and effectiveness.
Frequently Asked Questions
What is a Continuous Improvement Advisor?
A Continuous Improvement Advisor is an individual who provides advice and guidance to organizations on how to streamline their processes and operations, in order to improve efficiency and effectiveness.
What kind of processes does a Continuous Improvement Advisor focus on?
A Continuous Improvement Advisor typically focuses on processes related to quality, cost, time, customer service, and safety.
What kind of skills does a Continuous Improvement Advisor need?
A Continuous Improvement Advisor should have strong problem-solving and analytical skills, as well as knowledge of Lean Six Sigma principles, data analysis, and process design.
How can a Continuous Improvement Advisor help an organization?
A Continuous Improvement Advisor can help an organization identify areas of improvement and develop strategies to streamline processes and increase efficiency. They can also provide recommendations on changes that may need to be implemented in order to achieve desired outcomes.
What is Lean Six Sigma?
Lean Six Sigma is a process-improvement methodology that combines the tools used in Lean and Six Sigma to improve the quality and efficiency of processes. It is used to identify and eliminate waste, reduce variation, and improve customer satisfaction.
What are jobs related with Continuous Improvement Advisor?
- Administrative Advisor
- Logistics Advisor
- Performance Advisor
- Financial Planning and Analysis Advisor
- Tax Advisor
- Digital Transformation Advisor
- Strategic Communications and Public Relations Advisory Services
- Supply Chain Advisor
- Product Management Advisor
- Training Advisor
Web Resources
- Continuous Improvement and Advising - Kansas State University nacada.ksu.edu
- Continuous Improvement - Boston University www.bu.edu
- Continuous Improvement Office | CFO CFO cfo.ufl.edu
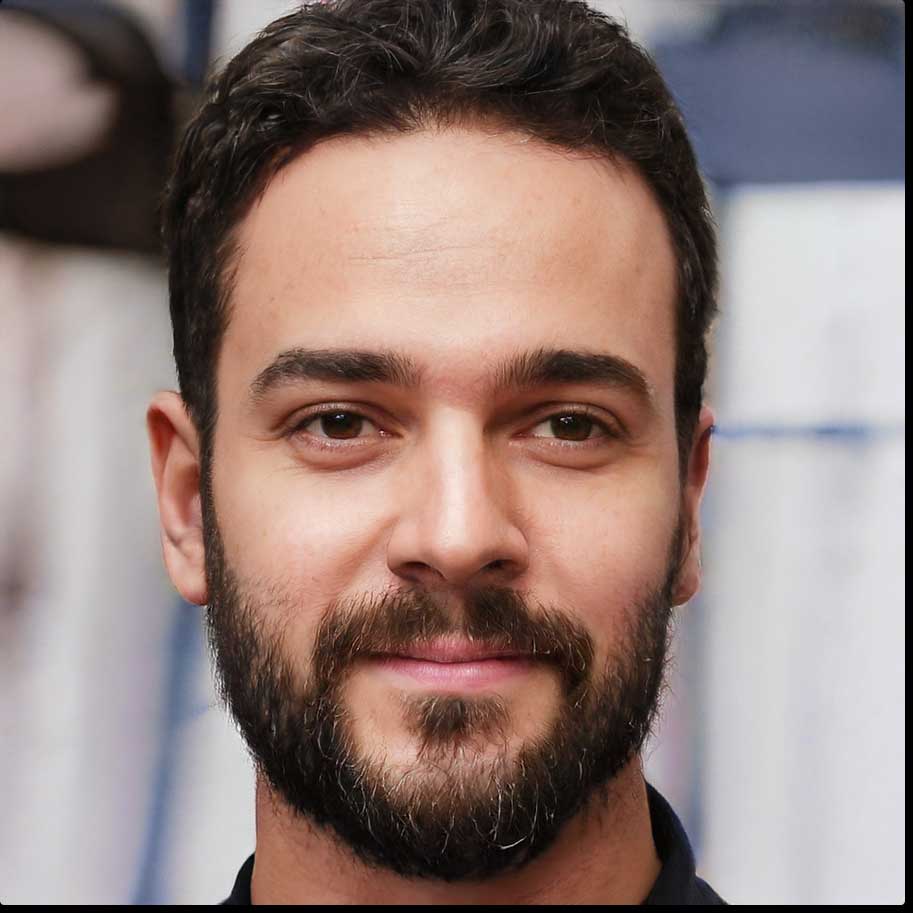