How to Be CNC Lathe/Mill/Drill Operators - Job Description, Skills, and Interview Questions
CNC lathe/mill/drill operators are responsible for the efficient operation of Computer Numerical Control (CNC) machinery, which is used to shape materials such as metal and plastics into complex geometrical components. The operators must understand the process of programming, setting up, and running the machines, and they must be able to identify and troubleshoot any issues that may arise. As a result, CNC lathe/mill/drill operators must possess a combination of effective knowledge of the machines, manual dexterity, and the ability to work with precision.
Furthermore, they must be able to read and interpret technical drawings and blueprints in order to create the desired product. In addition, they must create quality assurance checks and maintain accurate records of the production process. the performance of CNC lathe/mill/drill operators directly affects the accuracy and quality of the finished product.
Steps How to Become
- Obtain a high school diploma or equivalent. Most employers prefer applicants who have a high school diploma or its equivalent.
- Consider enrolling in a CNC machinist training program. CNC machinist training programs typically include instruction in operation and maintenance of CNC machines, programming and setup, machine operation and safety. Most programs last between six months and two years, depending on the intensity of the program.
- Obtain on-the-job experience. Many employers require CNC lathe/mill/drill operators to have some prior experience with CNC machines before they will be considered for a job. Some employers provide on-the-job training as well. Check with local employers to see if this is an option.
- Become certified. Certification is not required for CNC lathe/mill/drill operators, but it can help demonstrate knowledge and experience. Certification is available through organizations such as the National Institute for Metalworking Skills (NIMS).
- Maintain certifications and stay informed on industry developments. As with any industry, staying informed on new developments and keeping certifications up-to-date are important for CNC lathe/mill/drill operators.
In order to stay ahead and capable as a CNC Lathe/Mill/Drill Operator, it is important to have a strong understanding of computer numerical control (CNC) technology and machine operations. staying up-to-date on the newest trends in machining technology and attending seminars and workshops can help operators stay ahead of the curve. By doing so, operators are able to use the latest tools and techniques to maximize efficiency and accuracy, while also keeping their skills sharp.
Furthermore, operators should ensure that their machines are maintained properly and kept in good condition for optimal performance and safety. With the right knowledge, experience, and tools, CNC Lathe/Mill/Drill Operators can stay ahead of the competition and be more capable in their jobs.
You may want to check Robotics Operators, Telephone Operator, and Grader Operator for alternative.
Job Description
- CNC Lathe Operator
- CNC Mill Operator
- CNC Drill Operator
- CNC Programmer
- Tool & Die Maker
- Quality Inspector
- Maintenance Technician
- Production Supervisor
- Machine Shop Supervisor
Skills and Competencies to Have
- Understanding of CNC machine tools and their operations
- Ability to read blueprints, sketches, and diagrams
- Mechanical aptitude and knowledge of shop mathematics
- Proficiency in programming CNC machines
- Knowledge of cutting tools and tooling systems
- Ability to monitor and adjust machine settings
- Ability to troubleshoot and solve mechanical problems
- Knowledge of safety practices and procedures
- Ability to maintain accurate records and logs
- Attention to detail and accuracy in work product
Having the right skills for CNC Lathe/Mill/Drill Operators is essential for success in the industry. Good mathematical skills are crucial in order to accurately calculate feed rates, speeds, and depths of cut, as well as to understand complex programs and instructions. strong problem solving and troubleshooting skills are necessary, since machines can often malfunction or experience errors.
Attention to detail is also important as any mistakes can be costly. Good hand-eye coordination is also important, as operators must be able to accurately adjust the machines and guide the tools. Finally, the ability to work with computers and technology is essential in order to operate the machines and understand their programming.
All of these skills combined make a successful CNC Lathe/Mill/Drill Operator and can lead to increased job security, higher wages, and greater job satisfaction.
Radio Operator, Powerhouse Technician/Operator, and Wheel Loader Operator are related jobs you may like.
Frequent Interview Questions
- What experience do you have in operating CNC machines?
- How familiar are you with the various types of CNC machines?
- Describe a time when you had to troubleshoot a problem with a CNC machine.
- How do you ensure that the settings and adjustments on a CNC machine are correct?
- What safety protocols do you follow when operating CNC machines?
- How do you ensure accuracy and quality when operating CNC machines?
- What measures do you take to minimize scrap and waste when working with CNC machines?
- How do you stay current with advances in CNC technology?
- What techniques do you use to optimize cycle time and efficiency when working with CNC machines?
- Describe your experience in programming CNC machines.
Common Tools in Industry
- Lathe. A machine used to shape metal and other materials into round forms, usually cylindrical shapes (eg: turning a metal rod into a screw).
- Mill. A machine used to cut, shape, and finish materials (eg: cutting a groove in a metal plate).
- Drill. A machine used to make a hole, especially in metal (eg: drilling pilot holes for screws).
- Bandsaw. A saw with a long, continuous blade used for cutting metal, wood, and other materials (eg: cutting a pipe to length).
- Grinding Wheel. A wheel used to sharpen metal or other materials (eg: sharpening drills to a point).
- Router. A machine used to cut and shape wood and other materials (eg: routing an inlay pattern on a wooden board).
Professional Organizations to Know
- Association for Manufacturing Technology (AMT)
- The National Institute for Metalworking Skills (NIMS)
- Society of Manufacturing Engineers (SME)
- American Machine Tool Distributors Association (AMTDA)
- International Association of Machinists and Aerospace Workers (IAMAW)
- National Tooling and Machining Association (NTMA)
- International Organization for Standardization (ISO)
- American National Standards Institute (ANSI)
- European Federation for Precision Machinery Manufacturers (EFPM)
- National Institute of Standards and Technology (NIST)
We also have Combination Welder Operators, Truck Operator, and Plant Operator jobs reports.
Common Important Terms
- CNC. Computer Numerical Control An automated machine that is programmed to perform a series of tasks with precision and accuracy.
- Lathe. A machine tool that rotates a workpiece on its axis to perform various operations such as cutting, sanding, drilling, and turning.
- Mill. A machine tool used for shaping or machining metal or other materials.
- Drill. A tool used for making cylindrical holes in materials, usually metal.
- CAM. Computer-Aided Manufacturing A software program used to create instructions for CNC machines to follow.
- CAD. Computer-Aided Design A software program used to create 2D and 3D models of parts and products.
- G-Code. A standardized programming language used to control CNC machines.
- Jig. A special tool used to hold a workpiece in place during machining operations.
- Chuck. A mechanical device used to hold a workpiece in place during machining operations.
Frequently Asked Questions
Q1: What is a CNC Lathe? A1: A CNC lathe is a computer numerically controlled (CNC) machine tool used for producing precision metal parts. It is capable of cutting, drilling, and turning metal parts with high accuracy and repeatability. Q2: What is a CNC Mill? A2: A CNC mill is a computer numerically controlled (CNC) machine tool used for machining metal parts. It is capable of cutting, drilling, and milling metal parts to precise specifications. Q3: What is a CNC Drill? A3: A CNC drill is a computer numerically controlled (CNC) machine tool used for drilling holes in metal parts. It is capable of drilling precise and accurate holes with high repeatability. Q4: What are the responsibilities of a CNC Lathe/Mill/Drill Operator? A4: The responsibilities of a CNC Lathe/Mill/Drill Operator include setting up and operating CNC lathes, mills, and drills to produce precision metal parts according to customer specifications. They must be able to read and interpret blueprints, understand the principles of CNC machining, and perform quality control checks on finished parts. Q5: What skills are required for a successful career as a CNC Lathe/Mill/Drill Operator? A5: Skills required for a successful career as a CNC Lathe/Mill/Drill Operator include mechanical aptitude, attention to detail, knowledge of mathematics and physics, computer programming skills, and the ability to read and interpret blueprints.What are jobs related with CNC Lathe/Mill/Drill Operators?
- Production Line Operators
- Excavator/Dozer/Grader/Scraper/Loader/Hoe Operators
- Pipe Layer Operator
- Bulldozer Operator
- Concrete Pump Operator
- Lift Truck Operator
- Sewerage Treatment Plant Operators
- Heavy Equipment Mechanic /Operator
- Power Plant Operators
- Production Control Room Operator
Web Resources
- CNC Lathe and Milling Training in CT | Goodwin College www.goodwin.edu
- CNC Machinist Lathe/Mill Operator Career Programs careercenter.dom.edu
- CNC Mill Training - University of Florida mae.ufl.edu
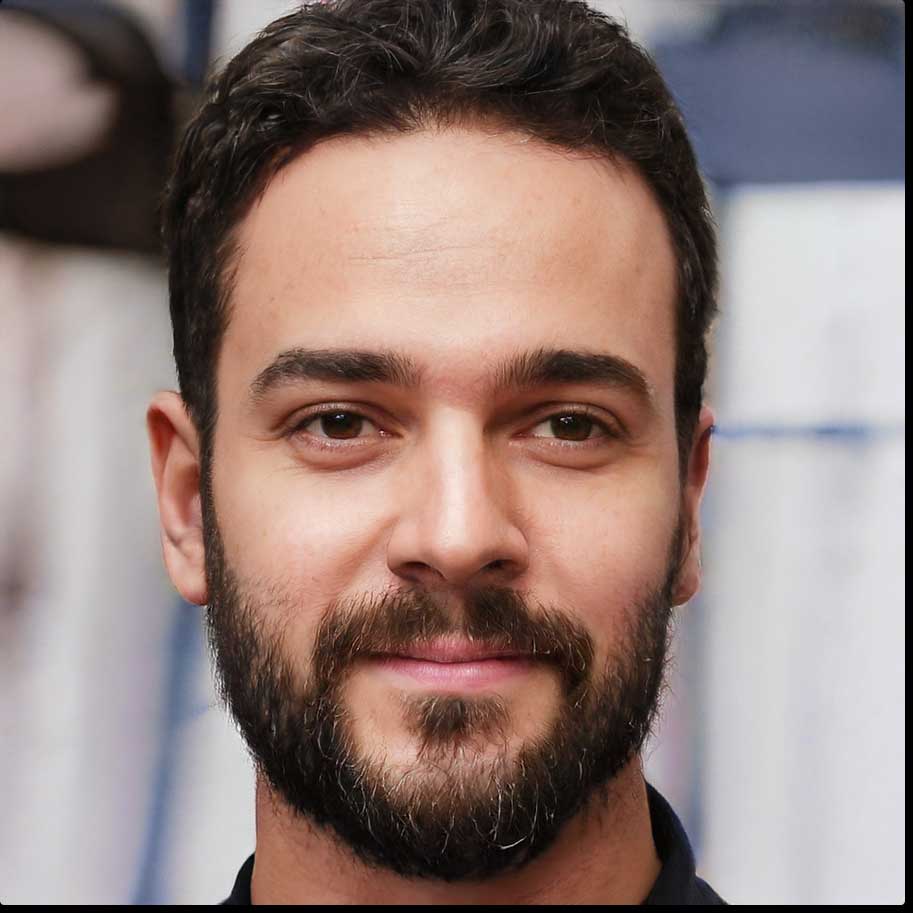