How to Be Supply Chain Planner - Job Description, Skills, and Interview Questions
The increasing complexity of global supply chains has caused a significant demand for Supply Chain Planners. With this demand, there is an increased focus on understanding and managing the complexities of the supply chain process, from forecasting and inventory management to logistics and production planning. The role of the Supply Chain Planner is to ensure that all aspects of the supply chain are functioning efficiently, taking into account factors such as cost, quality, and delivery times.
As such, they are essential in ensuring that companies are able to keep up with customer demand, while staying competitive in their markets. This has led to improved customer satisfaction and increased revenues for many businesses.
Steps How to Become
- Obtain a Bachelor's Degree. To become a supply chain planner, you will need to have a bachelor's degree in a field such as business, logistics, supply chain management, or a related field.
- Consider Professional Certifications. Professional certifications can help to demonstrate your knowledge and skills in the field of supply chain planning and management. Consider getting certified through the American Production and Inventory Control Society (APICS) or the Institute for Supply Management (ISM).
- Gain Experience. Many employers prefer to hire supply chain planners who have experience in the field. Consider gaining experience through internships, volunteer positions, or entry-level jobs in the industry.
- Network. Connecting with other professionals in the field can help you to find job opportunities and stay up to date on industry news and trends. Consider joining professional organizations, attending conferences and workshops, and connecting with other professionals through LinkedIn and other social media sites.
- Find a Job. Once you have the necessary education, certifications, and experience, you can start looking for job opportunities as a supply chain planner. Contact recruiters, search job boards, and reach out to your professional network for assistance finding job openings that match your qualifications.
Good supply chain planners must stay updated and competent in their knowledge and skills in order to remain effective. To do this, they must stay informed on the latest industry trends and technological advancements, as well as invest time in developing their own skills. This can be done by enrolling in professional development courses, attending seminars and conferences, or reading industry publications.
By staying aware of new trends, technology, and techniques, supply chain planners are better able to anticipate customer needs and develop effective strategies for meeting them. by continually honing their skills, supply chain planners will be better equipped to analyze data, develop cost-efficient solutions, and provide quality service that meets customer expectations. As a result, companies can benefit from increased efficiency, reduced costs, and improved customer satisfaction.
You may want to check Urban Planner, Marketing Planner, and Network Planner for alternative.
Job Description
- Analyze supply chain operations and identify areas of improvement.
- Monitor inventory levels and ensure efficient supply chain operations.
- Develop strategies to reduce costs and improve efficiency in the supply chain.
- Monitor supplier performance and develop relationships with key suppliers.
- Maintain strong communication with internal departments and external partners.
- Prepare and analyze reports on supply chain performance and metrics.
- Create and implement supply chain management plans and strategies.
- Develop processes and procedures to support effective supply chain operations.
- Develop, manage and monitor supplier contracts to ensure compliance with company policies and procedures.
- Track and report on supply chain performance metrics.
- Negotiate prices, terms, and conditions with suppliers.
- Forecast demand for materials and adjust purchasing plans to meet changing needs.
- Coordinate activities related to warehousing, transportation, and distribution of goods.
- Manage quality control processes for incoming materials and products.
- Monitor compliance with international trade regulations and other applicable laws.
Skills and Competencies to Have
- Analytical thinking and problem-solving skills
- Knowledge of supply chain processes and best practices
- Familiarity with inventory management systems
- Ability to interpret data and develop solutions
- Ability to identify potential risks and develop contingency plans
- Excellent communication and interpersonal skills
- Time management and organizational skills
- Knowledge of applicable government regulations
- Project management skills
- Experience working with cross-functional teams
- Knowledge of warehouse operations
- Knowledge of industry trends and customer demands
Having an effective supply chain planner is essential for any business to succeed. The ability to analyze data and develop strategies to optimize the supply chain process can have a huge impact on a companys bottom line. The most important skill for a supply chain planner to have is the ability to recognize trends and anticipate potential supply chain disruptions.
This includes the ability to identify factors such as changes in customer demand, surges or declines in raw materials, and shifts in production processes. a good supply chain planner must be able to collaborate with other departments such as sales, marketing, and procurement, in order to develop innovative solutions to ensure that all stakeholders have a successful outcome. Finally, the ability to communicate effectively with suppliers, customers, and other stakeholders is paramount for any successful supply chain planner.
By leveraging these skills and having a deep understanding of the supply chain process, companies can maximize efficiency, reduce costs, and increase customer satisfaction.
Media Planner, Inventory Planner, and Retail Planner are related jobs you may like.
Frequent Interview Questions
- Describe your experience with supply chain planning and inventory optimization.
- What strategies do you use to manage supply chain demand?
- What challenges have you faced in developing and executing a successful supply chain plan?
- How do you stay up-to-date with the latest industry trends in supply chain planning?
- How do you ensure that suppliers are meeting the necessary requirements for quality and quantity?
- How do you develop and maintain accurate forecasts of demand and supply?
- How have you used data analysis to improve the efficiency of supply chain operations?
- How do you create contingency plans to manage risks and optimize the supply chain?
- How do you use customer feedback to improve the effectiveness of supply chain planning?
- What techniques do you use to reduce costs and improve the accuracy of inventory management?
Common Tools in Industry
- Inventory Management Software. This software helps companies manage their inventory, automatically reorder stock when necessary, and track product movement. (eg: Oracle Inventory Management)
- Logistics Management System. This system helps businesses plan, execute and optimize the transportation of products from one location to another. (eg: SAP Logistics Management)
- Demand Planning Software. This software helps forecast future demand for products and services and assists in developing a plan to meet those demands. (eg: JDA Demand Planning)
- Supplier Relationship Management Software. This software helps companies manage relationships with suppliers, negotiate better pricing and ensure timely delivery of materials. (eg: Ariba Supplier Relationship Management)
- Warehouse Management System. This system helps companies track inventory levels, optimize storage space, and manage shipping and receiving processes. (eg: HighJump Warehouse Management)
- Transportation Management System. This system helps companies plan, route and optimize shipments to minimize costs and improve customer service. (eg: Descartes Transportation Management)
Professional Organizations to Know
- American Production and Inventory Control Society (APICS)
- Institute for Supply Management (ISM)
- Logistics and Supply Chain Management Society (LSCMS)
- Chartered Institute of Procurement and Supply (CIPS)
- The International Warehouse Logistics Association (IWLA)
- Council of Supply Chain Management Professionals (CSCMP)
- National Association of Purchasing Management (NAPM)
- Warehousing Education and Research Council (WERC)
- International Supply Chain Education Alliance (ISCEA)
- Supply Chain Management Association (SCMA)
We also have Business Planner, Resource Planner, and Travel Planner jobs reports.
Common Important Terms
- Supplier Relationship Management (SRM). The process of managing and optimizing the interactions between a business and its suppliers. It includes activities such as supplier selection, contract negotiation, performance management, and supplier communication.
- Demand Planning. The process of forecasting customer demand for products and services in order to ensure that the right product is available at the right time.
- Supply Chain Management (SCM). The coordination of all activities that are related to the flow of goods from the point of origin to the point of consumption, including production, inventory management, and transportation.
- Inventory Management. The process of monitoring and controlling inventory levels in order to maintain efficient operations.
- Logistics. The coordination of the movement of goods from one location to another, including the planning and execution of the transportation of goods.
- Warehouse Management. The process of managing and controlling the storage and movement of goods within a warehouse or distribution center.
Frequently Asked Questions
What is a Supply Chain Planner?
A Supply Chain Planner is an individual responsible for managing and organizing the resources, materials, and processes of a companys supply chain. This includes overseeing the flow of goods, services, and information between suppliers, manufacturers, retailers, and customers.
What are the core responsibilities of a Supply Chain Planner?
The core responsibilities of a Supply Chain Planner include making sure that the supply chain is running as efficiently as possible; forecasting demand and supply to ensure that products are available when needed; coordinating with suppliers, manufacturers, and other entities in the supply chain; tracking shipments and inventory; and developing strategies to reduce costs.
What skills do I need to be a successful Supply Chain Planner?
To be a successful Supply Chain Planner you need to have strong analytical, organizational, and problem-solving skills. You also need to be familiar with supply chain management software and processes, and have a good understanding of logistics.
What qualifications are required for a Supply Chain Planner role?
Generally, employers look for applicants with a bachelors degree in supply chain management, business administration, or a related field. Some employers may also require experience in logistics, operations management, or supply chain planning.
How much does a Supply Chain Planner earn?
The average salary for a Supply Chain Planner is $62,000 per year. However, salaries can vary greatly depending on experience level, location, and the size of the company.
What are jobs related with Supply Chain Planner?
Web Resources
- Supply Chain Planning | Sloan School of Management | MIT ¦ ocw.mit.edu
- Understanding The Role Of Supply Chain Planning www.collegian.psu.edu
- How To Do Strategic Supply-Chain Planning sloanreview.mit.edu
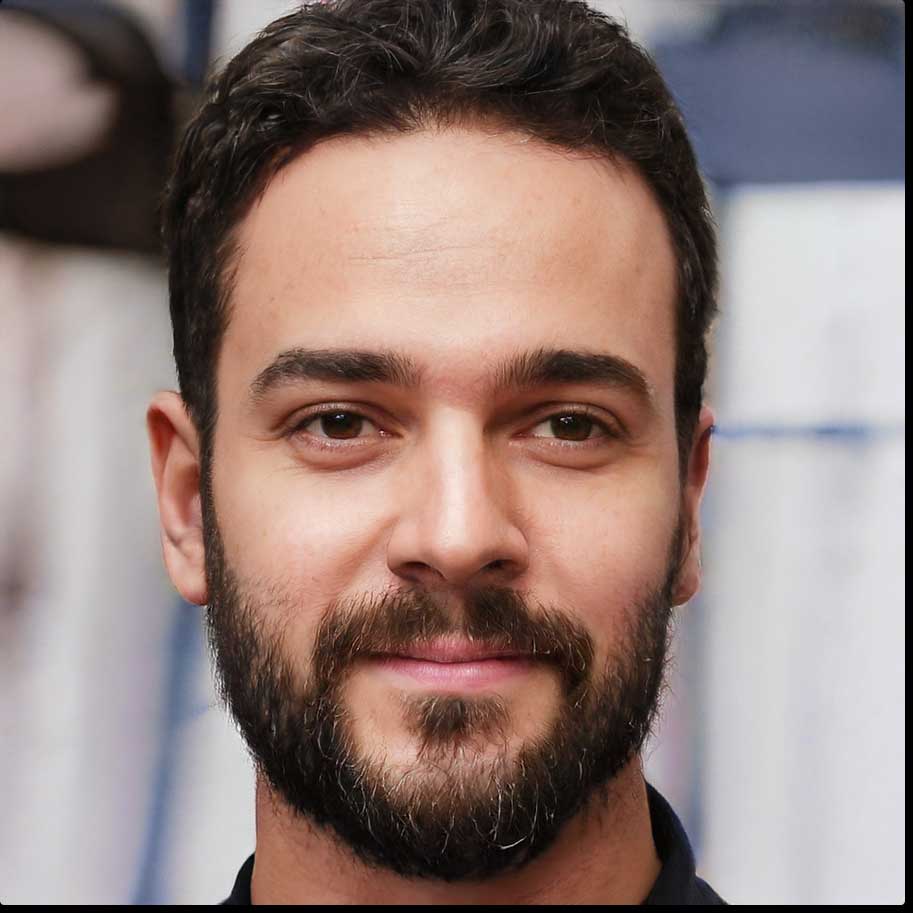