How to Be Safety Guide - Job Description, Skills, and Interview Questions
The use of drugs and alcohol can have serious and life-altering effects on an individual's physical and mental health. Substance abuse can lead to addiction, which can in turn cause numerous physical, psychological, and social problems. Physical symptoms include changes in appetite, fatigue, insomnia, and weakened immunity.
Mental health issues such as depression, anxiety, and suicidal thoughts may arise. Social problems can include relationship issues, legal troubles, and financial difficulties. In addition, substance use can lead to a decreased performance at work or school, as well as increase the risk of motor vehicle accidents.
The best way to avoid the negative consequences of drug and alcohol use is to abstain from using them altogether.
Steps How to Become
- Complete a Bachelor's Degree. To become a safety guide, you must first earn a bachelor's degree in safety management, safety engineering, or a related field.
- Obtain Certifications. Obtaining certifications in safety management or safety engineering can help you to stand out from other applicants. The certifications will demonstrate your commitment to the profession.
- Gain Experience. You should look for opportunities to gain experience in the field. This can include internships, volunteer work, and other related positions.
- Apply for Positions. Once you have the necessary qualifications, you can begin applying for safety guide positions. Look for openings in industries such as construction, manufacturing, and healthcare.
- Familiarize Yourself with Safety Regulations. You should become familiar with various safety regulations, such as OSHA standards. This will help you to ensure that safety protocols are being followed in your workplace.
- Stay Up to Date on Industry Developments. As a safety guide, you should stay up to date on industry developments and new regulations. This will help you to better protect the safety of your colleagues.
Negligence and incompetence can lead to serious consequences. When it comes to being reliable and competent, there are certain actions that should be taken. Firstly, it is important to take the time to understand the job thoroughly, and to ask questions if something is unclear.
Secondly, it is essential to plan ahead and make sure that tasks are completed on time and to the best of ones ability. Thirdly, double-checking work is important, as mistakes cost time and resources. Finally, it is important to keep communication open between colleagues, supervisors and customers in order to ensure that everyone is on the same page.
By taking these steps, one can become more reliable and competent, leading to better performance and greater success.
You may want to check Travel Guide, Study Guide, and Nature Guide for alternative.
Job Description
- Construction Worker: responsible for performing manual labor and operating heavy machinery, such as bulldozers and cranes, to construct roads, buildings, and other structures.
- Electrician: responsible for installing and maintaining electrical systems, including wiring, fixtures, and other components.
- Plumber: responsible for installing, repairing, and maintaining plumbing and drainage systems.
- Welder: responsible for joining two pieces of metal together using heat and pressure.
- Painter: responsible for painting residential, commercial, and industrial buildings.
- HVAC Technician: responsible for installing, maintaining, and repairing heating, ventilation, and air conditioning systems.
- Roofer: responsible for repairing, replacing, and installing roofs on residential and commercial buildings.
- Heavy Equipment Operator: responsible for operating heavy machinery, such as bulldozers and cranes, to move materials around a construction site.
- Demolition Worker: responsible for demolishing buildings and other structures using explosives or heavy machinery.
- Landscaper: responsible for designing and maintaining outdoor spaces, such as gardens and lawns.
Skills and Competencies to Have
- Knowledge of safe work practices
- Ability to recognize and assess hazardous situations
- Knowledge of relevant safety regulations and standards
- Ability to identify potential safety risks and hazards
- Ability to use safety equipment correctly
- Ability to recognize and act on warning signs
- Ability to communicate effectively with supervisors and peers
- Ability to operate safety equipment and perform safety checks
- Knowledge of emergency response procedures
- Ability to document safety incidents and report them to the appropriate authorities
Having a strong sense of situational awareness is the most important skill to have for staying safe. Being aware of your surroundings and being alert to any potential threats can help you to avoid dangerous situations. Being able to recognize potential signs of danger, understanding what could happen if a situation escalates, and knowing how to respond appropriately can make all the difference.
Knowing when to trust your intuition and when to get help can also be crucial. having a plan in place in case of an emergency can help to keep you safe and can increase your chances of getting out of a dangerous situation safely.
User Guide, Technical Guide, and Health Care Guide are related jobs you may like.
Frequent Interview Questions
- What experience do you have in safety management?
- How would you go about developing and implementing safety procedures?
- What strategies have you used to ensure that safety guidelines are followed in the workplace?
- How do you handle challenging safety situations?
- Describe a time when you successfully identified and addressed a safety hazard.
- How do you stay up to date on changes in safety regulations?
- What steps do you take to ensure the safety of employees in hazardous working environments?
- How would you go about educating employees on safety protocols?
- Describe a time when you had to investigate an incident and create a report.
- What strategies do you use to motivate employees to follow safety regulations?
Common Tools in Industry
- Safety Glasses. Protective eyewear designed to protect the eyes from hazardous materials or flying debris. (eg: safety glasses with side shields)
- Hard Hats. Protective headgear designed to reduce the risk of head injury from falling objects and head contact with fixed objects. (eg: full brim hard hat)
- Ear Plugs. Ear plugs are designed to reduce the noise level and protect one's hearing. (eg: foam ear plugs)
- Respirators. A device that covers the nose and mouth to filter out harmful particles in the air. (eg: N95 respirator)
- Safety Gloves. Gloves designed to protect the hands from cuts, burns, and other injuries. (eg: leather work gloves)
- Steel-Toed Boots. Protective footwear with steel toes designed to protect the feet from heavy objects falling or rolling onto them. (eg: steel-toed work boots)
Professional Organizations to Know
- American Psychological Association
- American Psychiatric Association
- National Association of Social Workers
- American Academy of Child & Adolescent Psychiatry
- American Occupational Therapy Association
- National Association of School Psychologists
- American School Counselor Association
- American Counseling Association
- National Association for Mental Illness
- American Association for Marriage and Family Therapy
We also have Museum Guide, Trekking Guide, and Buying Guide jobs reports.
Common Important Terms
- Fall Protection. Fall protection is a safety measure designed to protect a person against any potential or actual danger of falling. It typically consists of harnesses, anchor points, lanyards, and other components.
- Personal Protective Equipment (PPE). Personal Protective Equipment (PPE) is any type of clothing or equipment used to protect an individual from potential hazards while they are working. Examples include hard hats, safety glasses, respirators, and protective clothing.
- Hazard Identification. Hazard identification is the process of recognizing and classifying potential risks in a work environment. It involves identifying the characteristics of the hazard and assessing how it can be managed.
- Risk Assessment. Risk assessment is the process of determining the level of risk associated with a hazard. It includes evaluating the likelihood of exposure and severity of injury or harm that could occur if the hazard is not mitigated.
- Lockout/Tagout (LOTO). Lockout/Tagout (LOTO) is a safety procedure that ensures that hazardous energy sources are isolated and cannot be used until the energy source has been released and the work has been completed.
- Confined Spaces. Confined spaces are areas that are not designed for continuous employee occupancy, but have limited or restricted means for entry and exit. Examples include tanks, pipes, vessels, and trenches.
- Hot Work. Hot work is any type of work that involves open flames, sparks, or high temperatures. Examples include welding, soldering, and metal-cutting operations.
Frequently Asked Questions
Q1: What is the purpose of the Safety Guide? A1: The purpose of the Safety Guide is to provide guidance for individuals in order to ensure safety during potentially hazardous situations and work environments. Q2: How often should I review the Safety Guide? A2: It is recommended to review the Safety Guide at least once a year to ensure you are familiar with all safety regulations and procedures. Q3: Who should use the Safety Guide? A3: The Safety Guide should be used by everyone working in hazardous environments, including employees, supervisors, and management. Q4: What are the key components of the Safety Guide? A4: The key components of the Safety Guide include recognizing and avoiding hazardous situations, proper use of safety equipment, emergency response protocols, and medical procedures. Q5: What are some examples of hazardous situations? A5: Examples of hazardous situations include working with heavy machinery, exposure to toxic chemicals or fumes, working at heights, and operating motor vehicles.What are jobs related with Safety Guide?
- Camping Guide
- Photography Guide
- Technology Guide
- Retirement Planning Guide
- Investment Banking Guide
- Shopping Guide
- Entertainment Guide
- Investment Adviser Guide
- Film Guide
- Outdoor Adventure Guide
Web Resources
- Safety Guide // University Safety // Marquette University - m.mu.edu m.mu.edu
- Safety Guide // University Safety // Marquette University www.eop.mu.edu
- Lab Safety Guide | Environmental Health and Safety ehs.stonybrook.edu
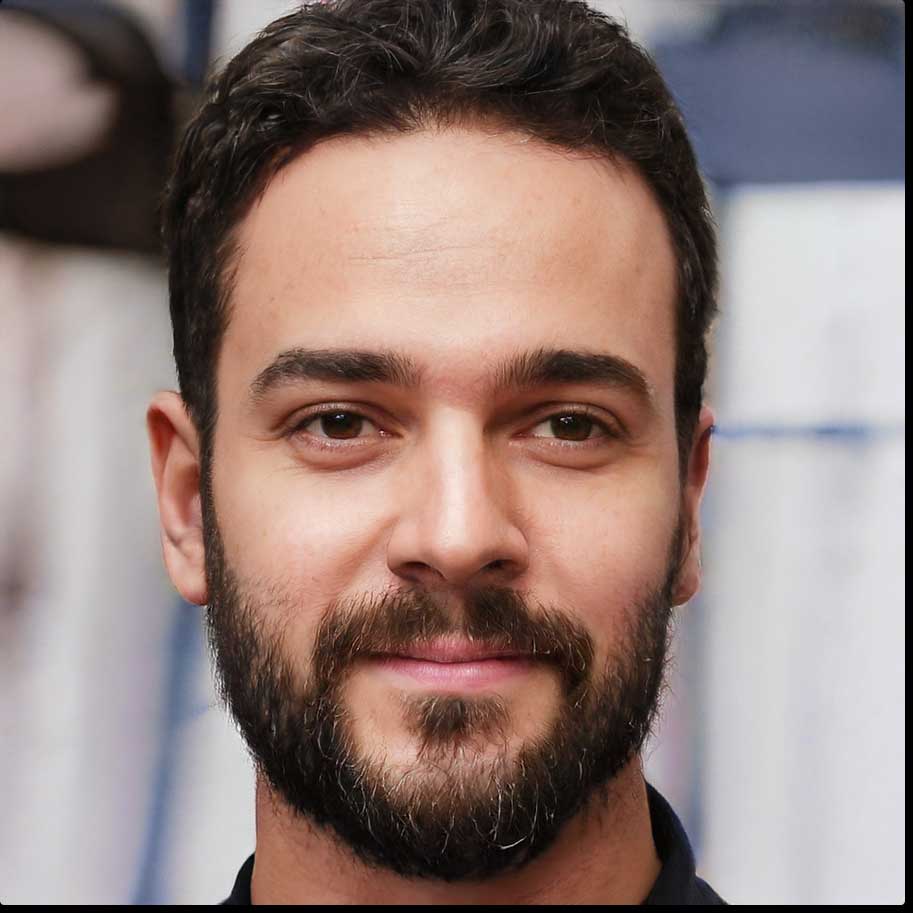