How to Be Quality Control Analyst - Job Description, Skills, and Interview Questions
When companies do not have a quality control analyst, they are at risk of producing inferior products. This can lead to a decrease in customer satisfaction, decreased profits, and a tarnished brand reputation. In addition, it can also lead to increased customer complaints, increased customer returns, and increased warranty costs.
Having a quality control analyst in place helps to ensure that products meet company quality standards by monitoring the production process and testing the finished product. This can not only improve customer satisfaction and increase profits, but also help to protect the companys brand reputation.
Steps How to Become
- Earn a Bachelor's Degree. The first step to becoming a Quality Control Analyst is to pursue a bachelor's degree in a relevant field such as quality control, engineering, or business. A degree in this field will provide you with the necessary skills and knowledge to become a Quality Control Analyst.
- Get Certified. Obtaining certification in quality control and/or engineering is recommended for those seeking to become a Quality Control Analyst. This can help demonstrate your knowledge of quality control and engineering principles, as well as give you an edge over other applicants for jobs.
- Gain Work Experience. Many employers prefer to hire Quality Control Analysts who have some previous work experience in the field. Consider gaining experience by taking on part-time or temporary jobs in quality control or engineering, or volunteering with a local organization or company to gain hands-on experience.
- Develop Expertise. To increase your chances of getting hired as a Quality Control Analyst, consider developing expertise in one specific area of quality control or engineering. This could include learning more about a particular type of machinery, software, or process that is used in the field.
- Consider Specialization. Consider specializing in a specific industry if you are looking to gain a competitive edge in the job market. By specializing in an industry such as aerospace, automotive, healthcare, or food manufacturing, you will be better prepared to tackle the unique challenges of that industry and make yourself more attractive to potential employers.
- Network. Networking is key for anyone looking for a job in any field. Consider attending industry events, joining professional associations, and connecting with other professionals in the field to increase your chances of finding a job as a Quality Control Analyst.
An effective and efficient quality control analyst is essential to maintain the standards of quality for any business. The analyst must possess an aptitude for problem solving, a keen eye for detail, and a dedication to improving processes. Having these traits allows them to identify potential issues and take corrective actions to prevent them from occurring.
Quality control analysts often utilize data analysis techniques to identify trends and root causes of problems and take steps to resolve them. they are responsible for creating and implementing quality assurance processes, monitoring production and inspecting products to ensure they meet the required standards. By doing this, the analyst can help improve overall product quality and customer satisfaction.
a successful quality control analyst is essential to the success of any business, as they provide the assurance that the final product meets customer expectations.
You may want to check Histotechnician, Cytogenetic Pathologist, and Histopathology Technician for alternative.
Job Description
- Monitor and inspect product quality to ensure compliance with standards
- Perform detailed laboratory analysis of products to identify defects
- Analyze data collected from product testing to identify trends in quality
- Develop and implement quality control systems and protocols
- Investigate customer complaints related to product quality
- Develop corrective actions to address identified quality issues
- Maintain accurate records of quality assurance activities
- Review processes and procedures to identify areas for improvement
- Coordinate with other departments to ensure quality standards are met
- Collaborate with suppliers to ensure the quality of incoming materials
- Monitor trends in customer feedback and industry standards to ensure product quality
- Train new staff members on quality assurance procedures and regulations
Skills and Competencies to Have
- Thorough knowledge of quality control processes and procedures
- Strong analytical and problem-solving skills
- Ability to interpret and analyze data
- Good communication skills, both verbal and written
- Knowledge of relevant software programs
- Highly organized and detail-oriented
- Ability to work independently and as part of a team
- Ability to make quick decisions and adapt to changing work environments
- Excellent interpersonal skills
- Ability to create and maintain accurate records
The role of a Quality Control Analyst is to ensure the quality of products and services produced by a business. As such, the most important skill for a Quality Control Analyst is attention to detail and an eye for accuracy. This means that the analyst must be able to carefully inspect products, verify accuracy of data and accurately document results.
Furthermore, they must be able to identify any potential issues or discrepancies in the product or service, as well as recommend solutions to rectify them. Quality Control Analysts must be able to work independently, as well as collaborate with other departments in order to ensure that quality standards are met. Without the skill of attention to detail, a Quality Control Analyst would not be able to effectively perform their duties, resulting in a decrease in the quality of products or services, decreased customer satisfaction, and ultimately, a decrease in profits.
Clinical Cytogeneticist, Transfusion Medicine Pathologist, and Cytopathologist are related jobs you may like.
Frequent Interview Questions
- How do you ensure that quality control processes are consistently followed?
- What experience do you have in analyzing and improving quality control systems?
- How do you identify and resolve quality issues?
- How do you monitor and measure the effectiveness of quality control processes?
- What techniques do you use to ensure accuracy in data collection and analysis?
- How do you go about setting and meeting quality standards?
- What methods do you use to track customer feedback and analyze customer satisfaction?
- How do you troubleshoot complex problems and determine root causes?
- Describe a time when you took initiative to identify and address an issue with a process or product.
- What tools and techniques do you use to detect and prevent errors in the quality control process?
Common Tools in Industry
- Statistical Process Control (SPC). A quality control tool used to monitor and control a process by measuring the output of the process and taking corrective action when necessary. (e. g. A Control Chart is a common type of SPC tool used to detect trends in the output of a process. )
- Failure Mode and Effects Analysis (FMEA). A quality control tool used to identify potential failures in a process and their associated risks. (e. g. An FMEA can be used to determine the likelihood of errors occurring and the potential sources of those errors. )
- Root Cause Analysis (RCA). A quality control tool used to identify the underlying causes of a problem or issue. (e. g. A Fishbone Diagram is a common type of RCA tool used to analyze causes and effects. )
- Plan-Do-Check-Act (PDCA). A quality control tool used to identify areas for improvement, develop solutions, and monitor the success of those solutions. (e. g. A PDCA Cycle is a common type of PDCA tool used to ensure continuous improvement in processes and systems. )
- Six Sigma. A quality control methodology used to identify and eliminate defects in processes and products. (e. g. DMAIC is a common type of Six Sigma tool used to improve existing processes. )
Professional Organizations to Know
- American Society for Quality (ASQ)
- International Society for Quality in Healthcare (ISQua)
- Institute for Quality Assurance (IQA)
- International Society for Pharmaceutical Engineering (ISPE)
- International Organization for Standardization (ISO)
- Society for Quality Assurance (SQA)
- European Organisation for Quality (EOQ)
- The Quality Management Forum (QMF)
- Certified Quality Auditor (CQA)
- American Association for Laboratory Accreditation (A2LA)
We also have Medical Director, Histotechnologist, and Molecular Diagnostic Scientist jobs reports.
Common Important Terms
- Quality Assurance (QA). The process of verifying that all products meet the required quality standards.
- Quality Control (QC). The process of inspecting, testing, and verifying that products meet the established quality standards.
- Regulatory Compliance. The process of ensuring that products meet all applicable regulatory requirements.
- Statistical Process Control (SPC). A method of quality control which uses statistical methods to identify and analyze production processes and identify defects or variations in the process.
- Root Cause Analysis (RCA). A process used to identify the cause or causes of a problem or issue, with the goal of eliminating or reducing the impact of the issue.
- Design of Experiments (DOE). A systematic approach to designing, analyzing, and interpreting experiments to test the effects of different variables on a given process or product.
- Quality Improvement. The process of making changes to a product or process to improve its performance, reliability, usability, or cost-efficiency.
Frequently Asked Questions
What is the primary role of a Quality Control Analyst?
The primary role of a Quality Control Analyst is to assess the quality of products and services to ensure they meet specified standards and regulations.
What qualifications are required to be a Quality Control Analyst?
To be a Quality Control Analyst, one typically requires a bachelor's degree in a related field such as engineering, chemistry, or mathematics. Knowledge of quality control principles and experience with quality assurance tools such as Six Sigma are also beneficial.
What type of environment do Quality Control Analysts typically work in?
Quality Control Analysts typically work in industrial or manufacturing settings, where they inspect and evaluate products or services to ensure they comply with quality standards.
What are the primary duties of a Quality Control Analyst?
The primary duties of a Quality Control Analyst include inspecting products or services for quality, creating detailed reports on any discrepancies found, and working with management to develop and implement quality assurance processes.
What type of salary can a Quality Control Analyst expect to earn?
According to the Bureau of Labor Statistics, the median salary for Quality Control Analysts in 2020 was $61,130 per year.
What are jobs related with Quality Control Analyst?
- Immunodiagnostics Scientist
- Forensic Pathologist
- Medical Laboratory Scientist
- Pathologist Assistant
- Medical Laboratory Supervisor
- Forensic Autopsy Pathologist
- Anatomic Pathology Technician
- Residency Program Director
- Surgical Pathology Technician
- Specimen Accessioner
Web Resources
- Example Career: Quality Control Analysts - West Virginia University www.wvu.edu
- Quality Control Analyst 3 - Stanford University Careers careersearch.stanford.edu
- Quality Control Analyst Chemistry Lab (Pharma Early Career ... careers.usc.edu
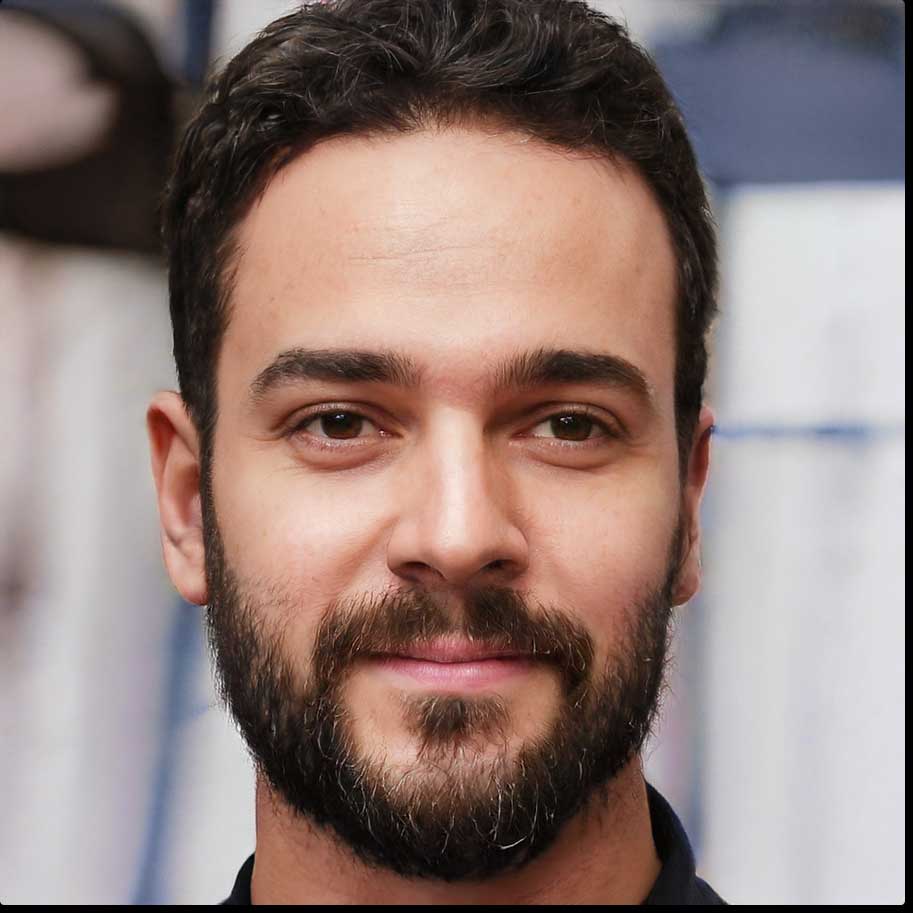