How to Be Quality Auditor - Job Description, Skills, and Interview Questions
The role of a Quality Auditor is critical for ensuring high standards of product quality and safety. Quality Auditors examine products and processes to ensure compliance with established standards, and upon finding any discrepancies, they take corrective action. This ensures that all products meet their intended requirements and that any defects or flaws are identified and addressed promptly.
As a result, customers receive products that are safe, reliable, and of consistent quality, leading to improved customer satisfaction and loyalty. this leads to increased sales, improved profitability, and a positive reputation for the company.
Steps How to Become
- Obtain a Bachelor's Degree. A basic requirement to become a Quality Auditor is to have a bachelor's degree in a related field, such as engineering, business administration, or industrial technology.
- Earn a Quality Auditor Certification. Individuals can obtain a Certified Quality Auditor (CQA) certification from the American Society for Quality (ASQ). This certification requires a passing score on the CQA exam and 3 years of professional experience in quality auditing.
- Gain Professional Experience. Professional experience in the quality audit field is essential for becoming a Quality Auditor. Individuals should look for internships or entry-level positions in quality audit departments to gain experience.
- Get Familiar with Quality Audit Tools. Quality Auditors should be familiar with the various tools used in the quality audit process, such as ISO 9000, Six Sigma, and other process control and improvement tools. Becoming knowledgeable about these tools will help ensure success in the quality audit field.
- Join Professional Organizations. Joining professional organizations such as the ASQ is a great way to stay up-to-date on industry trends and connect with other Quality Auditors.
In order to ensure that Quality Auditors remain updated and capable, they should maintain a consistent program of continuing education. This allows them to stay up to date with industry best practices and the latest advancements in quality assurance techniques. Doing so also enables them to be more effective in their roles, by having a greater understanding of the principles of quality management, and how to apply them to ensure the highest standards of quality in the products and services being offered.
Quality Auditors should participate in regular training programs, such as seminars and workshops, so they can further develop their skills and stay aware of the latest developments in their field. By consistently keeping their knowledge and skills up to date, Quality Auditors can ensure that they are able to provide the highest level of service to their organization.
You may want to check Senior Inventory Auditor, Human Resources Auditor, and Inventory Auditor for alternative.
Job Description
- Quality Auditor: Responsible for ensuring that products and services meet the established quality standards. Conducts inspections, tests and reviews processes to ensure compliance with internal and external standards.
- Quality Assurance Manager: Responsible for creating and maintaining a quality assurance program to ensure the highest level of customer satisfaction. Oversees the quality of products and services; evaluates processes and procedures; identifies areas for improvement; and implements changes as needed.
- Quality Improvement Analyst: Responsible for identifying and analyzing areas where quality can be improved, recommending solutions to management and implementing these solutions. Monitors performance metrics to track the results of the improvements.
- Quality Engineer: Responsible for designing, developing, and testing products to ensure they meet quality standards. Creates and maintains quality assurance plans, develops test methods and protocols, and performs tests on components or products.
- Quality Control Technician: Responsible for inspecting, testing, and evaluating products to ensure they meet quality requirements. Inspects parts and materials; documents results; and communicates findings to supervisors.
Skills and Competencies to Have
- Knowledge of Quality Management Systems
- Understanding of Quality Control and Quality Assurance principles
- Skill in using quality control and assurance testing methods
- Ability to interpret technical drawings, specifications and standards
- Proficient with data analysis techniques
- Excellent attention to detail
- Excellent written and verbal communication skills
- Problem-solving skills
- Knowledge of Lean Manufacturing principles
- Ability to work independently with minimal supervision
The quality auditor is responsible for ensuring that products meet the required standards of quality. To do this, they must possess a range of skills, such as attention to detail, problem-solving, critical thinking, and communication. Attention to detail is essential for quality auditing, as the auditor must be able to spot even the smallest flaws in a product.
Problem-solving skills are also necessary to identify and resolve any issues with the product. Critical thinking allows the auditor to analyze processes and procedures in order to improve quality and efficiency. Finally, effective communication skills enable the auditor to communicate their findings and suggestions for improvement to management.
All of these skills combined enable the quality auditor to fulfill their role and ensure that products meet the highest standards of quality.
Senior Information Systems Auditor, Senior Environmental Compliance Auditor, and Business Process Auditor are related jobs you may like.
Frequent Interview Questions
- What experience do you have in quality auditing?
- Describe a difficult and successful audit you've conducted.
- What processes and procedures do you use to ensure quality?
- How do you ensure adherence to quality standards?
- How do you go about identifying and addressing non-conformance issues?
- How would you handle a situation where a process or procedure is not in compliance with the standards?
- What challenges have you faced while conducting audits and how did you overcome them?
- Describe a time when you identified an issue that was not immediately obvious to others.
- What methods do you use to evaluate supplier performance?
- How do you stay up to date with changes in quality standards and regulations?
Common Tools in Industry
- Quality Checklist. A tool used to ensure that a product meets its quality requirements by verifying that it meets specific standards (e. g. ISO 9001).
- Root Cause Analysis. A tool used to identify the underlying cause of a problem and develop solutions to prevent it from happening again (e. g. 5 Whys).
- Process Mapping. A tool used to visualize, analyze and improve processes by identifying areas of waste and inefficiency (e. g. Value Stream Mapping).
- Statistical Process Control. A tool used to monitor a process to ensure that it meets quality requirements and identify any potential problems (e. g. Control Charts).
- Audits. A tool used to assess compliance with internal and external regulations, and identify any potential risks (e. g. Internal Audits).
- Failure Mode and Effects Analysis. A tool used to identify potential problems with a product or process before they occur (e. g. FMEA).
Professional Organizations to Know
- American Society for Quality (ASQ)
- International Organisation for Standardization (ISO)
- Institute of Quality Assurance (IQA)
- Institute of Quality Assurance (IoQA)
- American National Standards Institute (ANSI)
- National Institute of Standards and Technology (NIST)
- Association for Quality and Participation (AQP)
- American Society for Testing and Materials (ASTM)
- International Register of Certificated Auditors (IRCA)
- International Quality Federation (IQF)
We also have Environmental Compliance Auditor, Government Auditor, and Senior Network Security Auditor jobs reports.
Common Important Terms
- Quality Assurance. Quality assurance is the process of ensuring that all products and services meet specified requirements and are of acceptable quality.
- Quality Control. Quality control is a process used to ensure that a product or service meets a certain set of standards or requirements.
- Defects. Defects are flaws or deviations from predetermined criteria that cause a product or service to fail to meet its intended purpose.
- Non-Conformity. Non-conformity is a deviation from requirements or specifications.
- Root Cause Analysis. Root cause analysis is a process for identifying the underlying cause of problems or defects.
- Quality Audit. Quality audit is an independent review of a product, process, system, or organization to determine whether it meets specified requirements.
Frequently Asked Questions
What is the primary role of a Quality Auditor?
The primary role of a Quality Auditor is to assess the quality of products and services to ensure they meet established standards.
What qualifications are required to be a Quality Auditor?
Generally, Quality Auditors must have a degree in a related field (e.g. engineering, quality management, etc.) and certification related to quality assurance and auditing.
What type of documents does a Quality Auditor review?
Quality Auditors typically review documents such as technical drawings, specifications, process maps, customer complaints, test plans and reports, and non-conformance reports.
What are the key responsibilities of a Quality Auditor?
Quality Auditors are responsible for conducting audits, analyzing data, writing reports, identifying areas for improvement, and making recommendations to improve the quality of products and services.
How often should a Quality Auditor conduct audits?
The frequency of audits depends on the needs of the organization. Generally, audits are conducted on a regular basis, such as monthly or quarterly.
What are jobs related with Quality Auditor?
- Senior Risk Management Auditor
- Data Quality Auditor
- Revenue Cycle Management Auditor
- Operational Risk Management Auditor
- Senior Cost Auditor
- Compliance Monitoring Auditor
- Operational Auditor
- Tax Auditor
- Payroll Auditor
- Senior Health Care Compliance Auditor
Web Resources
- What is a Manufacturing Quality Auditor | Goodwin University www.goodwin.edu
- Quality Auditor - Stanford University Careers careersearch.stanford.edu
- Diploma of Quality Auditing (fast-track) | Courses | Swinburne www.swinburne.edu.au
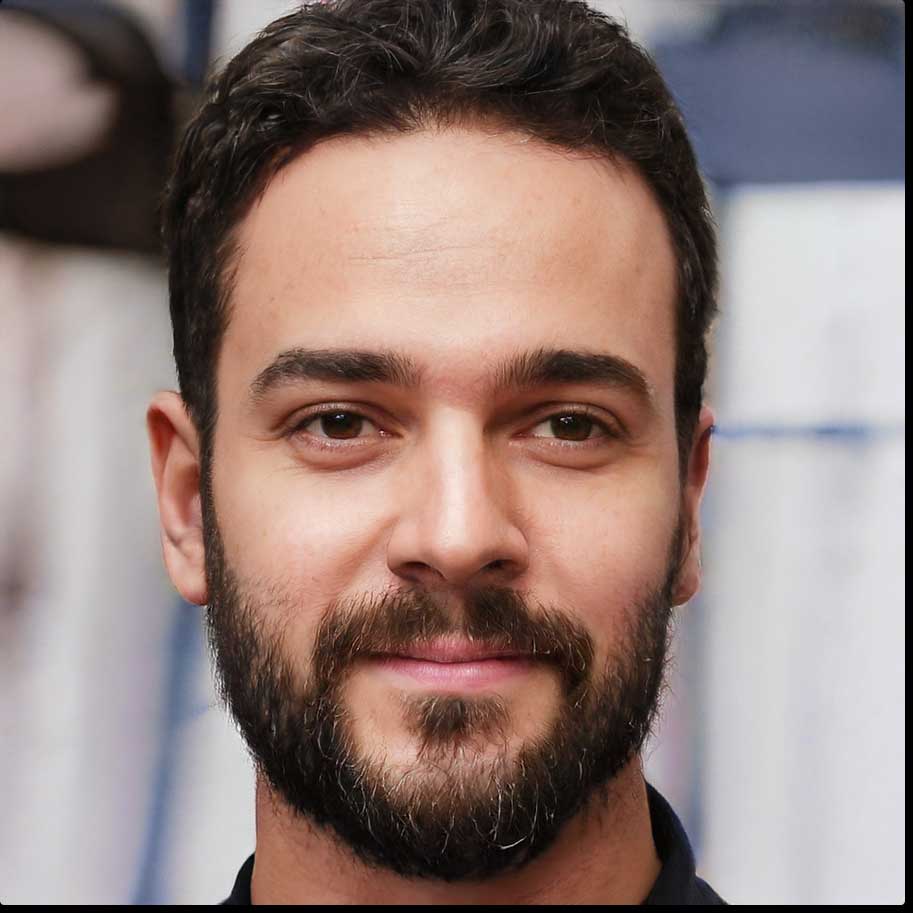