How to Be Printer Quality Assurance Technician - Job Description, Skills, and Interview Questions
The Printer Quality Assurance Technician is responsible for ensuring the quality of printed products meets the standards set by the customer. To do this, they must thoroughly inspect the printed materials for accuracy and completeness. If any problems are found, the technician must take corrective action to ensure that the product is of the highest quality.
The technician must also keep detailed records of every product tested, and these records must be accurate in order to ensure that any future problems can be quickly identified and corrected. The quality assurance process is a critical element in maintaining a successful printing business, as customers rely on the assurance that their products will meet their expectations. As a result, the Printer Quality Assurance Technician plays a key role in helping to ensure a high level of customer satisfaction.
Steps How to Become
- Obtain a high school diploma or equivalent. Printer Quality Assurance Technicians must have a basic educational background to qualify for the position.
- Acquire experience in the printing industry. Experience in the field is essential for obtaining a job as a Printer Quality Assurance Technician. Previous experience in printing, design, or graphic arts is beneficial.
- Obtain certification in the field. Although certification is not always required, it can help an individual stand out from other applicants. There are several organizations that offer certification in printing technology and quality assurance.
- Become knowledgeable in troubleshooting and repair of printers. Printer Quality Assurance Technicians must have a thorough understanding of how printers work and be able to troubleshoot and repair them when needed.
- Become familiar with various types of software used in the printing industry. Printer Quality Assurance Technicians must be knowledgeable in a variety of software programs that are used in the printing industry.
- Develop strong organizational and communication skills. Printer Quality Assurance Technicians must be able to organize their work and communicate effectively with customers and other personnel.
In order to become an ideal and qualified Printer Quality Assurance Technician, one must possess a strong technical background and excellent problem-solving skills. This profession requires a level of knowledge in computer and printer repair and maintenance, as well as familiarity with printing standards and protocols. Furthermore, having a good eye for details and being able to identify errors quickly is essential.
If a person has all of these skills, they will be able to monitor the quality of printed materials, identify and troubleshoot printer malfunctions, and ensure that the printers are working efficiently and accurately. As a result, they will be able to maintain the quality of the printed materials, which will create a better customer experience and lead to customer satisfaction.
You may want to check Printer Operator Supervisor, Printer Technician Supervisor, and Print Room Manager for alternative.
Job Description
- Perform routine inspections and tests on a variety of printing equipment to ensure quality standards are met.
- Monitor the performance of printers and other related equipment to identify any potential issues.
- Troubleshoot equipment errors and malfunctions to determine root cause and corrective action.
- Analyze customer complaints and feedback to determine potential quality issues.
- Develop and implement process control plans and procedures to enhance product quality.
- Update and maintain product and process documentation.
- Research and recommend new technologies, products, or processes to improvequality standards.
- Prepare quality control reports and present findings to management.
- Ensure compliance with all applicable safety standards, regulations, and policies.
- Train other personnel on quality assurance processes and procedures.
Skills and Competencies to Have
- Knowledge of printer hardware, software, and networking
- Ability to troubleshoot and diagnose printer problems
- Ability to perform maintenance and repair tasks on printers
- Familiarity with industry-standard print quality assurance methods and techniques
- Knowledge of color management, calibration, and other print quality-related processes
- Attention to detail and precision when inspecting printed documents
- Ability to evaluate the quality of prints according to customer specifications
- Ability to work independently with minimal supervision
- Excellent communication skills, both verbal and written
- Strong organizational and time management skills
The success of any Printer Quality Assurance Technician depends on their ability to possess the right set of skills. First and foremost, they must be detail-oriented and have an eye for quality. This means that they must be able to detect any discrepancies or abnormalities in the printing process and take the necessary steps to correct them.
In addition, they must possess great problem solving and troubleshooting skills in order to identify and determine the root cause of any issue. They must also be knowledgeable in the use of special inspection tools, such as magnifying glasses, calipers and microscopes, in order to perform detailed inspections. Furthermore, they must have excellent communication skills in order to collaborate with other technicians and managers.
All of these skills combined make a Printer Quality Assurance Technician an invaluable asset in any organization.
Printer Sales Representative, 3D Printer Technician, and Print Production Planner are related jobs you may like.
Frequent Interview Questions
- What experience do you have in printer quality assurance?
- How do you prioritize tasks to ensure printers are functioning correctly?
- What strategies do you use to troubleshoot printer issues?
- What methods do you use to ensure the highest level of quality for printers?
- Describe a time when you identified a problem with a printer and adjusted it to better meet customer needs.
- How do you stay up to date on the latest printer technology?
- How comfortable are you with using complex software to diagnose and repair printers?
- How do you handle difficult customer service situations related to printer issues?
- What processes do you use to ensure the proper maintenance of printers?
- Describe a time when you successfully identified and resolved a complex printer issue.
Common Tools in Industry
- Multimeter. a device used to measure electrical current, voltage, and resistance. (eg: measuring the electrical current of a printer)
- Oscilloscope. an electronic instrument used to measure the voltage and time relationship of a signal. (eg: testing the voltage of a printer's motor)
- Automated Print Quality Analysis Software. software used to analyze the quality of printed documents. (eg: analyzing the print resolution of a printed document)
- Digital Caliper. an instrument used to precisely measure distances between two points. (eg: measuring the gap size between two printer parts)
- Inkjet Printer Profiling Software. software used to calibrate inkjet printers for consistent color accuracy. (eg: calibrating an inkjet printer for accurate color printing)
- Colorimeter. an instrument used to measure the color of light or other radiant energy. (eg: measuring the color accuracy of a printed document)
- Microscope. an instrument used to magnify small objects or details of objects. (eg: examining the printed ink dots on a printed document)
Professional Organizations to Know
- Association for Quality Assurance Professionals (AQAP)
- American Society for Quality (ASQ)
- European Society for Quality Research (ESQR)
- International Association for Quality (IAQ)
- Quality Assurance Institute (QAI)
- Institute of Quality Assurance (IQA)
- Japan Quality Assurance Organization (JQAO)
- International Organization for Standardization (ISO)
- International Quality Federation (IQF)
- Quality Management Institute (QMI)
We also have Digital Print Finisher, Print Finisher Quality Inspector, and Wide Format Printer Operator jobs reports.
Common Important Terms
- Print Quality. The overall look and feel of a printed document, including clarity, sharpness, brightness, color accuracy, dark and light balance and other factors.
- Resolution. The amount of detail that can be seen in an image, measured in dots per inch (dpi).
- Dithering. A technique used to simulate multi-color tones in a single-color print.
- Color Theory. The study of color, including its perception and the relationships between various color combinations.
- Imaging Software. Computer programs used to manipulate digital images.
- Calibration. The process of adjusting a printer or monitor to achieve consistent results across different devices.
- Toner. A dry powder used in laser printers to produce the print image on paper.
- Inkjet Printing. A printing method that uses tiny jets of ink to create an image on paper.
- Media Types. The types of paper or other substrate used in printing.
- Printer Maintenance. Regular maintenance tasks required to keep printers operating properly, such as cleaning and replacing parts.
Frequently Asked Questions
What is a Printer Quality Assurance Technician?
A Printer Quality Assurance Technician is a professional responsible for ensuring the quality of printed material through inspections and tests.
What qualifications are required to become a Printer Quality Assurance Technician?
Generally, a Printer Quality Assurance Technician should have a high school diploma or GED and experience in the printing industry. Knowledge of printing technology, ink chemistry and color theory are also beneficial.
What types of tests do Printer Quality Assurance Technicians perform?
Printer Quality Assurance Technicians typically perform visual inspections, paper samples, color accuracy tests, line tests, and measurement tests to ensure the quality of printed materials.
How often does a Printer Quality Assurance Technician need to perform tests?
The frequency of tests performed by a Printer Quality Assurance Technician may vary depending on the specific requirements of a project. Generally, tests should be performed before, during, and after the printing process to ensure quality.
What tools do Printer Quality Assurance Technicians use?
Printer Quality Assurance Technicians use a variety of tools to perform tests and inspections, including rulers, calipers, micrometers, spectrophotometers, densitometers, and color bars.
What are jobs related with Printer Quality Assurance Technician?
- Digital Printer Operator
- Laser Printer Technician
- Print Production Manager
- Print Finisher Operator
- Print Traffic Coordinator
- Printer Administrator
- Print Finisher Supervisor
- Laser Printer Operator
- Inkjet Printer Technician
- Printer Repair Technician
Web Resources
- Quality Assurance Technician | gotoLTC gotoltc.edu
- Quality Assurance Technician Certificate - Community College of ... www.ccbcmd.edu
- Working in Quality Assurance: The Skills That You Need www.northeastern.edu
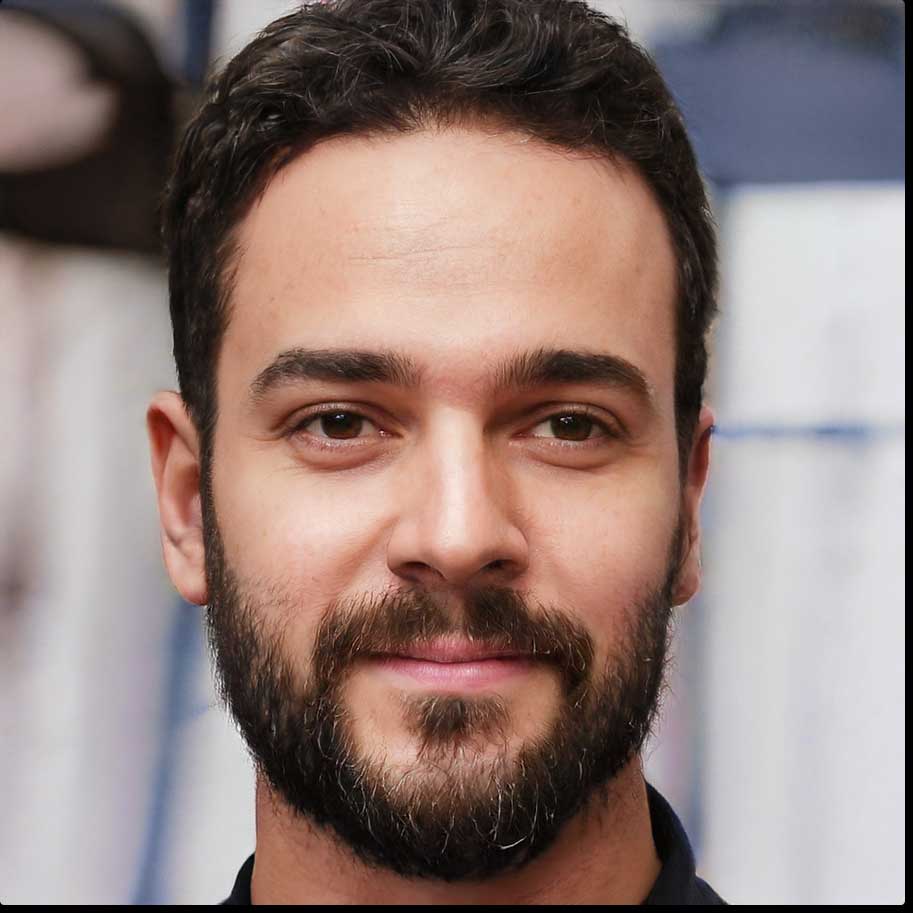