How to Be Musical Instrument Maker - Job Description, Skills, and Interview Questions
The demand for musical instrument makers has steadily increased over the past few years due to an increase in the popularity of playing music. As people become more interested in learning to play instruments, they are turning to instrument makers to provide them with the tools they need. This increased demand has created more jobs for instrument makers as well as opportunities for those who specialize in certain types of instruments such as string instruments, woodwinds, or percussion.
As instrument makers become more experienced and skilled in their craft, they can often create custom-made instruments that are tailored to the individual needs of the musician. This provides musicians with an instrument that perfectly fits their playing style and allows them to express themselves in a unique way. the increased demand for instrument makers has also led to more collaboration between musicians and instrument makers, which has allowed them to work together to create new sounds and genres of music.
This has further expanded the range of instruments available to musicians and has opened up a new world of possibilities for music.
Steps How to Become
- Earn a High School Diploma. The first step to becoming a musical instrument maker is to earn a high school diploma. Many students may choose to specialize in courses such as woodworking, metalworking, and electronics.
- Pursue Post-Secondary Education. After earning a high school diploma, aspiring musical instrument makers may want to pursue post-secondary education in order to gain a more comprehensive understanding of the craft. Colleges and universities may offer degree programs in music technology or related fields, such as instrument repair or building.
- Develop Technical Skills. Musical instrument makers must be skilled with a variety of tools and techniques in order to create quality instruments. Working with wood, metal, and electronics can involve intricate detail work, so it is important to have the proper skills.
- Find an Apprenticeship. Apprenticeships with experienced craftspeople are a great way to gain hands-on experience in the field. Instrument makers may also need to have experience working with computer-aided design (CAD) software in order to create plans for instruments.
- Join a Professional Association. Joining a professional organization, such as the Craftsmanship Guild or the Guild of American Luthiers, can provide invaluable resources for learning about the craft. It can also be a great way to meet other instrument makers and exchange ideas.
- Start Your Own Business. Once you have gained the necessary skills and experience, you may want to consider starting your own business as an instrument maker. This can be a rewarding career path that allows you to create custom instruments for clients around the world.
Musical instrument makers create instruments to be used by musicians. To become a reliable and competent instrument maker, it is essential to have a deep understanding of the craft, materials, and techniques. This requires a great deal of time and dedication to learning the nuances of instrument design and construction.
It is also important to have the right tools and materials on hand, as well as a good understanding of the physics behind sound production. Furthermore, it is necessary to have the ability to repair instruments, as well as the creativity to design new ones. With dedication and practice, one can become a reliable and competent musical instrument maker.
You may want to check Mastering Engineer, Arranger, and Music Teacher for alternative.
Job Description
- Woodworker: responsible for creating and building musical instruments from wood.
- Metalworker: responsible for creating and building musical instruments from metal.
- Finisher: responsible for finishing the musical instruments to a high standard.
- Luthier: responsible for assembling and maintaining stringed musical instruments.
- Acoustician: responsible for designing, testing and building instruments to ensure they produce the best sound possible.
- Electronics Technician: responsible for installing and maintaining electrical components in musical instruments.
- Technician: responsible for repairing and restoring musical instruments.
- Painter/Artist: responsible for painting, staining and designing custom finishes on musical instruments.
- Sales Representative: responsible for selling musical instruments to customers.
- Researcher: responsible for researching new materials and technologies to improve the sound and playability of musical instruments.
Skills and Competencies to Have
- Knowledge of musical instruments and their construction
- Ability to read and interpret plans and specifications
- Experience with hand tools, power tools and measuring devices
- Attention to detail and accuracy
- Ability to interpret musical scores
- Understanding of acoustic principles
- Ability to diagnose and repair musical instruments
- Knowledge of woodworking techniques
- Knowledge of musical instrument finishes
- Ability to communicate effectively with customers
- Knowledge of electronic components for amplified instruments
- Knowledge of musical instrument parts suppliers
- Ability to work independently or as part of a team
Musical instrument making is a skill that requires creativity, technical knowledge, and passion for music. The ability to craft and create a beautiful, high-quality instrument is a craft that takes time and dedication to learn. A successful instrument maker must have strong problem-solving skills, be detail-oriented, and have the ability to use a variety of tools and materials.
they must have an understanding of acoustics and the science behind creating instruments that sound great. Finally, they must have a good understanding of the history of music and instruments and be able to apply traditional techniques to create unique and modern instruments. All these skills combined make a successful musical instrument maker.
Music Business Manager, Event Coordinator, and Music Videographer are related jobs you may like.
Frequent Interview Questions
- What experience do you have making musical instruments?
- What is your approach to designing musical instruments?
- What challenges have you faced in the past when building musical instruments?
- Have you ever designed a new type of musical instrument?
- How do you ensure accuracy and quality when crafting musical instruments?
- What is your preferred method of joining materials when making musical instruments?
- What methods do you use to finish and varnish musical instruments?
- Are you familiar with traditional tools and techniques for making musical instruments?
- How have you adapted to the changing landscape of musical instrument making over the years?
- What additional skills or knowledge do you bring to this job that could benefit the production of musical instruments?
Common Tools in Industry
- Lathe. A machine used to shape metal and wood by rotating it against a cutting tool. (e. g. A lathe can be used to cut a guitar neck from a piece of wood. )
- Band saw. A powered saw with a long, narrow blade used for making curved and irregular cuts. (e. g. A band saw can be used to cut out the body of a guitar. )
- Drill press. A machine that uses a rotating drill bit to make precise holes in wood, metal, and other materials. (e. g. A drill press can be used to make the holes for the guitar strings and tuning pegs. )
- Sander. A power tool used to smooth surfaces by abrading them with sandpaper. (e. g. A sander can be used to smooth out the edges of a guitar body. )
- Router. A power tool used to shape and hollow out wood, plastic, or other materials. (e. g. A router can be used to shape a guitars sound hole. )
- Soldering iron. An electrical tool with a heated tip used for melting and joining two pieces of metal together. (e. g. A soldering iron can be used to join two pieces of metal for the bridge of a guitar. )
Professional Organizations to Know
- Association of Stringed Instrument Artisans (ASIA)
- Violin Making Association of America (VMAA)
- National Association of Professional Band Instrument Repair Technicians (NAPBIRT)
- International Guild of Musical Instrument Makers and Repairers (IGMIMR)
- American Lutherie Association (ALA)
- The American Federation of Violin and Bow Makers (AFVBM)
- The British Violin Making Association (BVMA)
- European Musical Instrument Makers Association (EMIMA)
- International Society of Bassists (ISB)
- Percussive Arts Society (PAS)
We also have Music Programmer, Music Producer, and Vocal Coach jobs reports.
Common Important Terms
- Luthier. A craftsman who builds and repairs stringed instruments such as violins, guitars and other string instruments.
- Woodworking. The craft of creating and manipulating wood to create objects, furniture and instruments.
- Acoustics. The science of sound and its phenomena, including the study of sound waves, vibration and resonance.
- Intonation. The adjustment of the pitch of a musical instrument to produce a desired sound.
- Tuning. The process of adjusting the strings of a musical instrument to the right pitch.
- Stringed Instrument. A musical instrument that uses a set of strings that are plucked or bowed to produce sound.
- Frets. Small metal bars on the neck of a guitar or other instrument that are used to produce different notes.
- Bridge. The part of a stringed instrument that supports the strings and transmits their vibrations to the body of the instrument.
- Varnish. A transparent coating applied to instruments to protect them from wear, moisture and dirt.
- Glueing. The process of joining two or more pieces of wood together with an adhesive.
Frequently Asked Questions
What is a Musical Instrument Maker?
A Musical Instrument Maker is a craftsman or luthier who builds, repairs, and restores stringed instruments such as violins, guitars, and other fretted instruments.
What qualifications does a Musical Instrument Maker need?
A Musical Instrument Maker typically requires a deep knowledge of the structure, sound production, and assembly of stringed instruments. They also need to have a high level of craftsmanship and experience with specialized tools.
What materials are typically used by Musical Instrument Makers?
Musical Instrument Makers often use a variety of materials such as wood, metal, and synthetic materials for the construction of their instruments. They also use glues, paints, and finishes to complete their work.
How long does it take to build a musical instrument?
The amount of time required to build a musical instrument depends on the complexity of the instrument and the skill of the luthier. Generally, it can take anywhere from a few weeks to several months to build an instrument.
What is the price range for a custom-made musical instrument?
The cost of a custom-made musical instrument can vary greatly depending on the complexity of the design, materials used, and the skill of the luthier. Generally, custom instruments can range from several hundred to several thousand dollars.
What are jobs related with Musical Instrument Maker?
- Music Journalist
- Voiceover Artist
- Instrumentalist
- Music Librarian
- Music Store Manager
- Audio Post Production Specialist
- Music Director
- Composer
- Recording Engineer
- Music Technologist
Web Resources
- Musical Instrument Making Classes | North Bennet Street School nbss.edu
- Invent a Musical Instrument | Lemelson Center for the invention.si.edu
- Musical Instrument Collection - University of Washington music.washington.edu
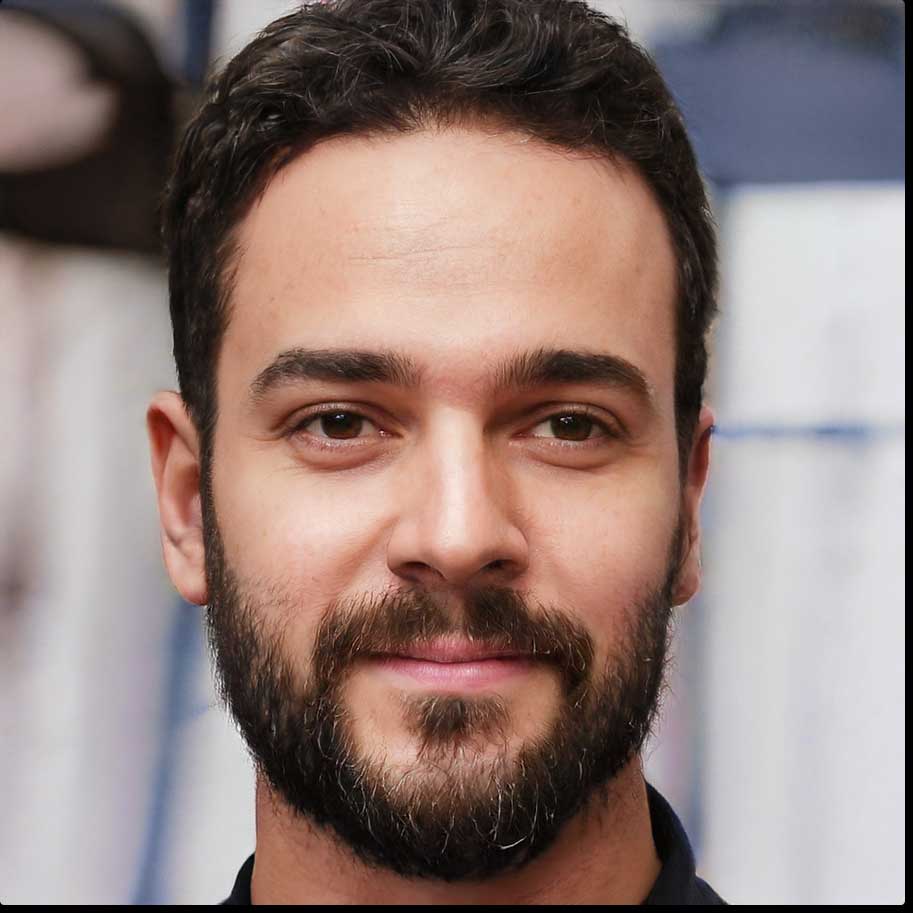