How to Be Mechanical Reliability Engineer - Job Description, Skills, and Interview Questions
The Mechanical Reliability Engineer is responsible for ensuring the reliability, durability and safety of mechanical products and systems. By understanding the design and operation of mechanical components, they can identify potential problems and develop solutions to reduce downtime and increase efficiency. In order to do this, the engineer must have a thorough understanding of the design, materials and processes involved, as well as knowledge of root cause analysis and corrective action.
This knowledge is essential in order to make the necessary changes to improve reliability and reduce costs, while maintaining conformance to regulatory standards. Not only does this role require technical knowledge, but also a strong problem-solving, analytical and communication skills.
Steps How to Become
- Earn a Bachelor's Degree. To become a mechanical reliability engineer, you typically need a bachelors degree in an engineering field, such as mechanical engineering. Coursework in a mechanical engineering program typically includes classes in mathematics, physics, mechanics, and materials science.
- Gain Relevant Work Experience. Most employers look for mechanical reliability engineers who have at least several years of relevant work experience. Gaining experience in the field may include completing work-related internships or volunteering for engineering positions.
- Become Certified. Obtaining certification can help you stand out from other applicants for positions as a mechanical reliability engineer. The American Society for Quality (ASQ) offers certification in reliability engineering. To qualify for certification, applicants must have at least three years of full-time work experience in reliability engineering, as well as 60 hours of professional development activities in the field.
- Take Professional Development Courses. Professional development courses can help you stay up to date on industry trends and new technology. Many professional development courses are available online, and some may be offered through employers or professional organizations.
- Join Professional Organizations. Joining a professional organization that focuses on mechanical reliability engineering can help you stay connected with industry trends and technology. Professional organizations may offer networking opportunities, as well as job postings and resources for career advancement.
In order to stay ahead and competent as a Mechanical Reliability Engineer, it is important to stay up-to-date on the latest advancements in engineering technology. By staying informed on new developments in the field, one can gain a greater understanding of the concepts and principles that govern mechanical reliability. it is important to continuously hone one's skills through practice and education.
By participating in seminars, workshops, and certification programs, a Mechanical Reliability Engineer can increase their knowledge base and stay abreast of the latest trends in the industry. Furthermore, networking with other professionals in the field can provide great insight into the current issues and solutions that are being implemented. Finally, having a well-rounded understanding of the fundamentals and concepts of engineering can help a Mechanical Reliability Engineer stay ahead and competent by providing a solid foundation of knowledge.
You may want to check Mechanical Design Engineer, Mechanical Service Technician, and Mechanical Maintenance Technician for alternative.
Job Description
- Develop and implement preventive maintenance plans, procedures and schedules for mechanical equipment.
- Develop and implement engineering solutions to improve the reliability of mechanical equipment.
- Provide technical guidance and support for troubleshooting mechanical systems.
- Monitor and evaluate the performance of mechanical systems and components to identify potential reliability issues.
- Identify root cause of mechanical system failures and recommend corrective actions.
- Perform failure analysis and root cause investigations.
- Collaborate with production, maintenance and engineering teams to develop solutions for mechanical system problems.
- Develop and implement predictive maintenance programs for mechanical equipment.
- Develop, analyze, and review technical drawings and specifications for mechanical systems.
- Provide technical support to operations and maintenance staff.
- Perform maintenance inspections of mechanical systems and components.
- Develop system maintenance processes and procedures.
- Develop cost estimates to support maintenance activities.
- Maintain documentation of maintenance activities and results.
- Monitor compliance with safety regulations related to mechanical systems and components.
Skills and Competencies to Have
- Knowledge of mechanical engineering principles and concepts.
- Ability to analyze and evaluate mechanical systems and components.
- Understanding of reliability engineering principles and practices.
- Ability to develop and implement reliability strategies, standards, and procedures.
- Proficiency in using industry-standard software for mechanical design and analysis.
- Knowledge of failure analysis techniques.
- Familiarity with metallurgy, tribology, and material science principles.
- Understanding of industry regulations and standards related to reliability engineering.
- Ability to research and develop new solutions to mechanical engineering problems.
- Excellent problem-solving, decision-making, and analytical skills.
- Excellent communication, interpersonal, and organizational skills.
Mechanical Reliability Engineers must have a wide range of skills to be successful in their role. A deep understanding of engineering principles and mechanics is essential, as they are responsible for developing strategies and systems to ensure the reliability of mechanical components and systems. strong analytical skills are important for analyzing data and making decisions based on their findings.
Furthermore, effective communication, problem-solving, and project management skills are necessary for creating and implementing comprehensive reliability plans. Finally, knowledge of reliability analysis and testing techniques is also essential in order to identify potential risks and develop and implement mitigation strategies. With these skills, Mechanical Reliability Engineers can ensure the efficient operation of their company's equipment, help reduce downtime, and save costs.
Mechanical Equipment Engineer, Mechanical Design Manager, and Mechanical Prototype Engineer are related jobs you may like.
Frequent Interview Questions
- What experience do you have in mechanical reliability engineering?
- Describe a challenging project you have recently worked on and how you overcame it.
- What have you done to improve the reliability of mechanical systems?
- How do you assess the reliability of a mechanical system?
- What methods do you use to ensure the accuracy of mechanical reliability data?
- Describe a time when you identified a potential issue with a mechanical system and implemented a solution.
- What tools do you use to troubleshoot mechanical faults?
- How do you assess the cost-effectiveness of mechanical reliability solutions?
- How do you ensure that mechanical systems comply with safety standards?
- What processes do you follow to ensure that mechanical systems are maintained properly?
Common Tools in Industry
- Stress Analysis Software. Used to predict how an object or structure will react under a certain amount of stress. (e. g. ANSYS)
- Finite Element Analysis Software. Used to analyze the behavior of complex structures in response to a variety of loading conditions. (e. g. ABAQUS)
- Failure Modes and Effects Analysis (FMEA). Helps identify potential failure modes and their associated effects, as well as potential causes and corrective actions. (e. g. FMEA-Pro)
- Computer-Aided Design (CAD) Software. Used to create detailed plans and drawings of machines and components. (e. g. Autodesk Inventor)
- Reliability Block Diagrams (RBDs). Used to graphically represent the reliability of a system by breaking it down into smaller components and analyzing their interdependencies. (e. g. Fault Tree Analysis)
- Finite State Machines (FSMs). Used to model a systems behavior by representing its internal states and transitions between them. (e. g. Visual Paradigm)
- Root Cause Analysis (RCA). Used to systematically identify the root cause of a failure or issue by analyzing its symptoms and effects. (e. g. TapRooT®)
- Statistical Analysis Software. Used to analyze large datasets and identify trends or correlations. (e. g. Minitab)
Professional Organizations to Know
- American Society for Quality (ASQ)
- Institute of Industrial and Systems Engineers (IISE)
- Institute of Mechanical Engineers (IMechE)
- International Council on Systems Engineering (INCOSE)
- International Federation for the Promotion of Mechanism and Machine Science (IFToMM)
- International Organization for Standardization (ISO)
- Society of Automotive Engineers (SAE)
- Society of Maintenance and Reliability Professionals (SMRP)
- Society for Maintenance and Reliability Professionals of India (SMRPI)
- The Institute of Reliability Engineers (IRE)
We also have Mechanical R&D Engineer, Mechanical Project Manager, and Mechanical Design Specialist jobs reports.
Common Important Terms
- Failure Modes and Effects Analysis (FMEA). A process used to identify potential issues that could cause a system to fail, and the effects those issues might have on the system.
- Reliability Centered Maintenance (RCM). A strategy used to determine the most cost-effective maintenance schedule for a system, taking into account its operating environment, failure modes, and other factors.
- Risk Management. The process of assessing, monitoring, and managing risks within an organization.
- Root Cause Analysis (RCA). A process used to identify the underlying cause of an issue or error.
- Life Cycle Cost Analysis (LCCA). An analysis of the costs associated with the acquisition, operation, and disposal of a system over its life cycle.
- Statistical Analysis. The use of descriptive statistics and other methods to analyze data and gain insight into trends and relationships.
- Quality Assurance (QA). A set of processes and procedures used to ensure that products or services meet a certain quality standard.
- Reliability Engineering. The discipline of engineering that focuses on ensuring that a system meets its reliability goals.
Frequently Asked Questions
What is a Mechanical Reliability Engineer?
A Mechanical Reliability Engineer is a professional who ensures that mechanical systems and components are designed, manufactured, operated, and maintained in a reliable and cost-effective manner.
What qualifications are required for a Mechanical Reliability Engineer?
A Mechanical Reliability Engineer typically needs to have a bachelor's degree in engineering, such as mechanical engineering or a related field, and experience in mechanical engineering, reliability engineering, or a related field.
What are the duties of a Mechanical Reliability Engineer?
The duties of a Mechanical Reliability Engineer include analyzing mechanical system designs, developing reliability plans and strategies, conducting failure analysis, developing maintenance plans, and performing root cause analysis.
What tools are used by Mechanical Reliability Engineers?
Mechanical Reliability Engineers use a range of tools and techniques to analyze systems and components, including statistical analysis, risk assessment, fault tree analysis, reliability modeling, and predictive maintenance.
What are the benefits of being a Mechanical Reliability Engineer?
Being a Mechanical Reliability Engineer offers the opportunity to work in an intellectually stimulating and challenging environment, with the opportunity to contribute to the reliability of mission-critical mechanical systems.
What are jobs related with Mechanical Reliability Engineer?
- Mechanical Integrator
- Mechanical Design Technician
- Mechanical System Designer
- Mechanical Parts Technician
- Mechanical Design Analyst Intern
- Mechanical Manufacturing Technician
- Mechanical Applications Engineer
- Mechanical Systems Engineer
- Mechanical Test Engineer
- Mechanical Test Technician
Web Resources
- Mechanical Reliability Engineer | NC State Online and Distance ¦ online-distance.ncsu.edu
- Mechanical Reliability Engineer NC State Continuing and ¦ mckimmoncenter.ncsu.edu
- Reliability Engineering Courses (ENRE) | Mechanical Engineering megrad.umd.edu
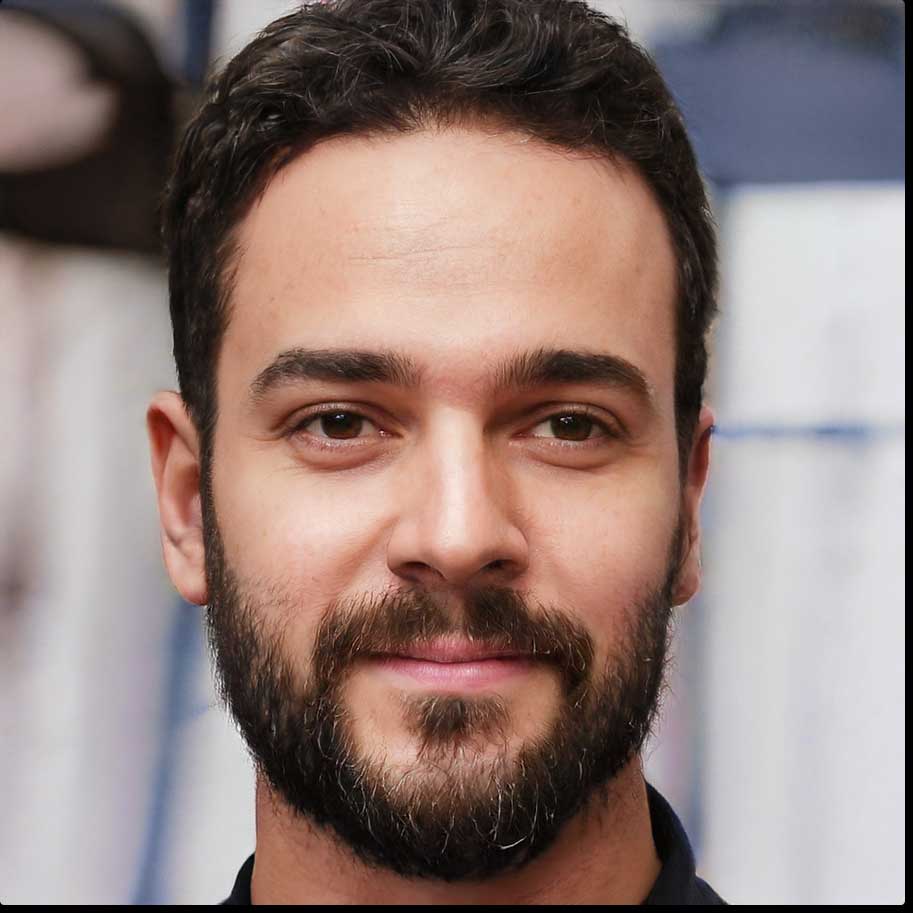