How to Be Mechanical Inspector - Job Description, Skills, and Interview Questions
Steps How to Become
- Earn a high school diploma or equivalent. Most employers require prospective inspectors to hold a minimum of a high school diploma or GED.
- Pursue postsecondary studies in mechanical engineering. While a college degree isn't necessary to become a mechanical inspector, having a background in mechanical engineering can make you more marketable. Courses in mathematics, physics and computer-aided design (CAD) may be beneficial.
- Obtain certification as a mechanical inspector. The American Society for Non-destructive Testing offers professional certification for mechanical inspectors. You must pass a written exam and have at least two years of experience in the field before you qualify for certification.
- Join a professional organization. Organizations such as the American Society for Non-destructive Testing and the American Society of Mechanical Engineers offer access to job postings, networking opportunities and continuing education courses.
- Apply for mechanical inspector jobs with manufacturing companies, engineering firms and inspection services. When applying, be sure to mention that you are certified by the American Society for Non-destructive Testing.
Mechanical inspectors are essential for ensuring that all mechanical components of a system are functioning properly and safely. The inspector's job is to identify any potential risks and hazards, and to recommend repairs or replacements if necessary. When hiring a mechanical inspector, it is important to ensure that they are reliable and capable.
This will ensure that the system is inspected thoroughly and all potential hazards are identified. Doing so can help to prevent costly repairs or replacements in the future and can help to protect the system from potential harm. reliable and capable mechanical inspectors are able to identify any issues before they become major problems, helping to minimize disruption and reduce overall system downtime.
You may want to check Weights and Measures Inspector, Pipeline Inspector, and Playground Equipment Inspector for alternative.
Job Description
- Inspect mechanical components, assemblies and systems to ensure they meet design specifications and quality standards.
- Perform visual and dimensional inspections of mechanical components and assemblies.
- Utilize precision measuring instruments such as calipers, micrometers and gauges.
- Test mechanical systems for proper operation and performance.
- Document inspection results in inspection reports and logbooks.
- Test and adjust mechanical systems, components and assemblies to ensure they meet performance requirements.
- Analyze test results and recommend modifications or repairs to ensure quality standards are met.
- Review blueprints and other documentation to determine inspection criteria and procedures.
- Develop and maintain quality control standards and procedures.
- Train and mentor junior mechanical inspectors.
Skills and Competencies to Have
- Knowledge of basic mechanical engineering principles and concepts
- Experience using inspection tools such as calipers, micrometers, gauges, and other measuring devices
- Ability to read and interpret blueprints, drawings, and specifications
- Proficiency in the use of computers, including spreadsheet and word processing applications
- Knowledge of applicable safety regulations and industry best practices
- Excellent problem-solving skills
- Attention to detail and quality control
- Strong communication and interpersonal skills
- Ability to work independently and as part of a team
- Ability to stand for extended periods of time
A successful Mechanical Inspector must possess a wide array of skills in order to ensure that all mechanical components and systems are functioning properly. Attention to detail, critical thinking, problem-solving skills, and the ability to analyze and interpret data are essential for performing effective inspections. Furthermore, the ability to look at a system holistically, as well as understanding the laws and regulations governing the inspection process, are key skills for a successful Mechanical Inspector.
Having a solid knowledge base of the mechanical components being inspected is also important in order to properly identify any potential issues. Finally, strong communication skills are essential for providing clear direction and feedback to both management and other inspectors. All of these skills lead to successful inspections, which in turn ensure that all mechanical systems are safe and reliable for use.
Leak Detection System (LDS) Inspector, Railroad Track Inspector, and Refrigeration and Air Conditioning Unit Inspector are related jobs you may like.
Frequent Interview Questions
- How have you prepared yourself to be a Mechanical Inspector?
- What experience do you have in inspecting mechanical components and systems?
- Describe your knowledge of mechanical engineering principles?
- What steps would you take to ensure accuracy when performing inspection procedures?
- How would you handle a situation where an inspection result did not meet the required standards?
- What challenges have you faced in your previous roles as a Mechanical Inspector?
- How do you stay updated on industry trends and equipment designs?
- What safety protocols do you follow when performing mechanical inspections?
- Describe your experience with interpreting technical drawings and blueprints.
- How would you handle difficult conversations with clients regarding inspection results?
Common Tools in Industry
- Calipers. A measuring tool used to measure the length, width, and depth of objects. (eg: measuring the diameter of a bearing)
- Micrometer. A precision measuring tool used to measure small distances, usually in thousandths of an inch. (eg: measuring the thickness of a sheet of metal)
- Gauge Block Set. A set of blocks with precisely machined grooves that can be used to check the accuracy of measurements. (eg: checking for flatness of a machined surface)
- Bore Gages. A tool used to accurately measure the inside diameter of a hole. (eg: measuring the bore diameter of a cylinder)
- Magnetic Particle Testing Equipment. An inspection tool used to detect surface and subsurface flaws in ferromagnetic materials. (eg: detecting cracks in a steel casting)
- Hardness Tester. A device used to measure the hardness of a material or object. (eg: testing the strength of a steel bolt)
- Ultrasonic Testing Equipment. An instrument used to detect flaws, measure thickness, and measure material properties in metal parts. (eg: inspecting the welds in an aircraft wing)
- X-Ray Equipment. A device used to detect internal flaws and defects in a variety of materials. (eg: inspecting the integrity of welds in a pressure vessel)
Professional Organizations to Know
- American Society for Quality (ASQ)
- American Welding Society (AWS)
- National Institute for Metalworking Skills (NIMS)
- American Society of Mechanical Engineers (ASME)
- Society of Manufacturing Engineers (SME)
- International Organization for Standardization (ISO)
- International Society of Automation (ISA)
- National Fire Protection Association (NFPA)
- American Society of Civil Engineers (ASCE)
- American Society of Heating, Refrigerating, and Air-Conditioning Engineers (ASHRAE)
We also have Telecommunications Tower Inspector, Building Code Inspector, and Radiation Protection Inspector jobs reports.
Common Important Terms
- Acceptance Criteria. The criteria that must be met in order for a product or service to be accepted.
- Tolerances. The range of allowable variation in a measurement.
- Gauging Standards. Standards for measuring and testing components for accuracy.
- Geometric Dimensioning and Tolerancing (GD&T). A set of symbols used to describe the dimensions, tolerances and other design requirements of a part.
- Visual Inspection. The process of visually checking a component or product for defects or discrepancies.
- Calibration. The process of adjusting a device to meet a predetermined standard.
- Non-Destructive Testing (NDT). Testing methods used to inspect components and products without causing damage or destruction.
- Quality Control. Processes used to ensure the consistent quality of a product or service.
Frequently Asked Questions
What is the role of a Mechanical Inspector?
A Mechanical Inspector is responsible for ensuring the safety and quality of mechanical equipment and systems by performing inspections, tests, and evaluations. They may also be involved in design, installation, maintenance, and repair of mechanical systems.
What qualifications are required to become a Mechanical Inspector?
Generally, a Mechanical Inspector should have a high school diploma or equivalent, and some experience in the area of mechanical engineering. In addition, they need to have knowledge of relevant codes and standards, be able to read and interpret blueprints, technical drawings and schematics, and possess problem-solving and communication skills.
What types of systems do Mechanical Inspectors inspect?
Mechanical Inspectors inspect components and systems such as engines, turbines, pumps, valves, compressors, and other mechanical components for compliance with safety standards and regulations. They may also inspect HVAC systems, boilers, cooling towers, and other industrial equipment.
How do Mechanical Inspectors perform their inspections?
Mechanical Inspectors usually use specialized equipment such as thermometers, pressure gauges, flow meters, oscilloscopes, and other testing instruments to measure the performance of mechanical systems. They also use visual inspection techniques such as checking for corrosion or wear on components.
What is the average salary of a Mechanical Inspector?
According to the U.S. Bureau of Labor Statistics, the median annual wage for Mechanical Inspectors is $53,830 per year as of May 2019.
What are jobs related with Mechanical Inspector?
- Boiler Inspector
- Swimming Pool/Spa Inspector
- Automotive Inspector
- Underground Storage Tank Inspector
- Mold Inspector
- Hazardous Materials (HazMat) Inspector
- Chemical Process Safety Management (PSM) Inspector
- Radon Gas Testing System (RGTS) Inspector
- Fire Alarm Systems Inspector
- Air Quality Management System (AQMS) Inspector
Web Resources
- Mechanical Inspector - ITQAN itqaninstitute.edu.sa
- Mechanical Inspection III | Asheville-Buncombe Technical abtech.edu
- Quality Inspector Mechanical Career Services | Nebraska careers.unl.edu
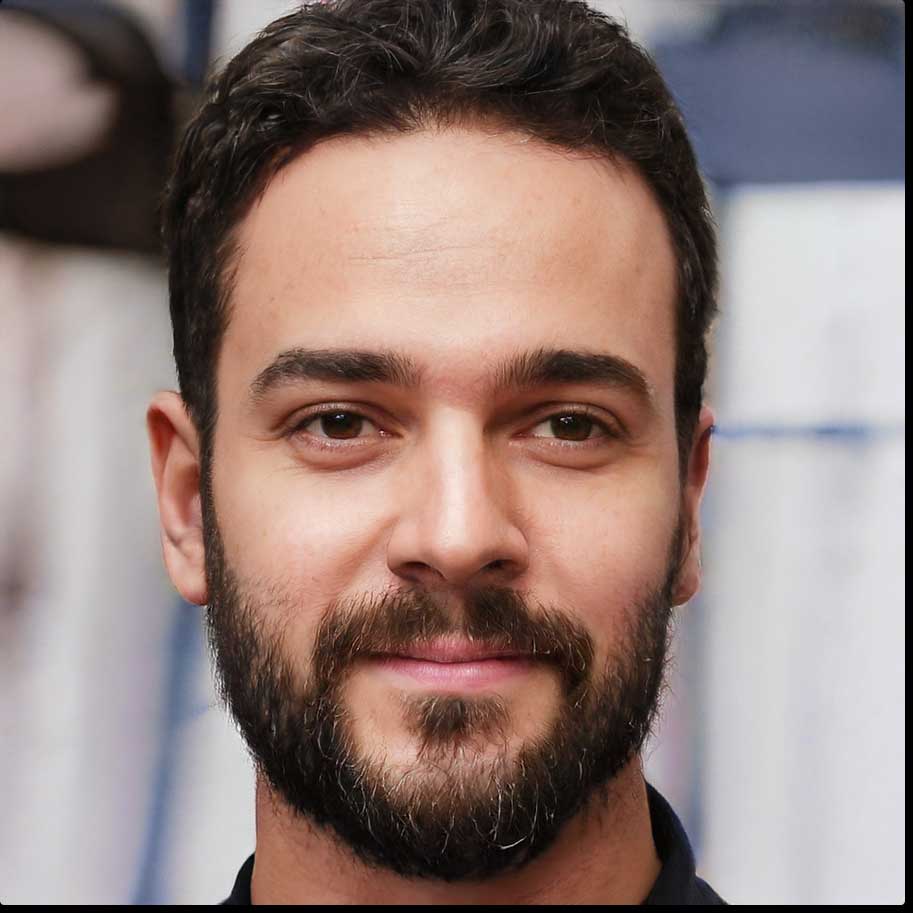