How to Be Machine Tool Operator - Job Description, Skills, and Interview Questions
Being a machine tool operator is a very important role in the manufacturing industry. It requires an individual to have a strong technical background, as well as great problem-solving and organizational skills. As a machine tool operator, you have the responsibility of setting up, operating, and maintaining the machinery that is used in the production process.
This involves understanding each machineâs capabilities and limitations, and being able to diagnose and fix any problems that may arise. By effectively managing the machinery, machine tool operators can ensure that production is running smoothly and efficiently. This, in turn, causes a higher quality of product, less waste, and faster production rates â ultimately leading to increased profits for the company.
Steps How to Become
- Obtain a High School Diploma or GED. Most employers require applicants for machine tool operator positions to have a high school diploma or GED.
- Enroll in a Machine Tool Operator Training Program. Some employers may offer on-the-job training, but most look for applicants who have completed a formal machine tool operator training program. These programs are typically offered at community colleges and technical schools and can take anywhere from several weeks to several months to complete.
- Gain Work Experience. Many machine tool operators gain entry-level experience through internships or apprenticeships. This allows them to gain hands-on experience while learning the fundamentals of the trade.
- Obtain Certification. Employers may look for certified machine tool operators. The National Institute for Metalworking Skills (NIMS) offers certification in various areas, such as computer numerical control (CNC) machining, manual machining, CAD/CAM programming, and other machine tool operations.
- Develop Job Skills. Machine tool operators must continuously develop their skills and stay up-to-date on new technologies in order to remain competitive in the job market. Staying abreast of advances in the field is essential for career growth and advancement.
Operating a machine tool requires skill and knowledge and can be a tedious process. To ensure reliable and efficient operation, operators must understand the principles and operations of the machine tool, including the types of tools and materials required, the functions of the machine, and the correct cutting speeds and feeds. Operators must also be aware of the safety standards and regulations associated with their operation.
operators must regularly maintain the machine tool, ensuring that all parts are in good working order and that all components are properly lubricated and adjusted. Finally, operators must be able to quickly diagnose and troubleshoot any problems that arise during the operation of the machine tool. By following these steps, operators can ensure reliable and efficient operation of their machine tool.
You may want to check Machine Maintenance Supervisor, Machine Shop Foreman, and Machine Vision Engineer for alternative.
Job Description
- CNC Machine Operator: Operates computer numerically controlled (CNC) equipment to fabricate precision parts from a variety of materials.
- Lathe Operator: Sets up and operates a variety of lathe machines to turn, bore, thread, form, or face metal or plastic materials.
- Milling Machine Operator: Sets up and operates milling machines to mill, shape, and drill metal or plastic materials into desired shapes and sizes.
- Drill Press Operator: Sets up and operates a variety of drill presses to drill, bore, ream, mill, or countersink metal or plastic parts.
- Grinding Machine Operator: Sets up and operates grinding machines to grind, sharpen, and smooth surfaces of metal or plastic workpieces.
- Saw Operator: Sets up and operates a variety of saws to cut metal, plastic, wood, or other materials into desired shapes.
- Press Operator: Sets up and operates a variety of presses to shape, form, trim, or cut metal or plastic parts.
- Tool and Die Maker: Designs, builds, repairs, and modifies jigs, fixtures, dies, molds, and other tools used in the manufacturing process.
- Quality Control Inspector: Inspects machined parts for conformance to specifications using a variety of measuring instruments.
- Machine Maintenance Technician: Performs routine maintenance on machine tools and ensures their safe and efficient operation.
Skills and Competencies to Have
- Knowledge of machine tools and their operation
- Ability to read and interpret blueprints, schematics and technical drawings
- Ability to operate manual and computer-controlled machinery
- Ability to make adjustments to tooling and machining parameters as needed
- Knowledge of operating safety protocols
- Dexterity and manual coordination
- Ability to understand and follow written and verbal instructions
- Ability to maintain accurate records of production
- Knowledge of quality assurance standards
- Ability to troubleshoot machine and tooling problems
Being a machine tool operator requires a great deal of precision and skill. It is important to understand the fundamentals of machine tools, their components, and how to operate them safely. having a strong attention to detail, good hand-eye coordination, and problem-solving skills are essential for this job.
Knowing how to read and interpret blueprints and diagrams also plays a key role in becoming a successful machine tool operator. With the right combination of knowledge and experience, machine tool operators can quickly identify any potential issues with the machines and take the necessary steps to fix them or prevent them from occurring in the first place. This helps ensure that the machines are running safely and efficiently, which reduces downtime and increases productivity.
Machine Tool Programmer, Machine Shop Supervisor, and Machine Maintenance Technician are related jobs you may like.
Frequent Interview Questions
- What experience do you have operating machine tools?
- What safety procedures have you implemented when operating machine tools?
- How do you troubleshoot and repair machine tools when they malfunction?
- What is your experience with using precision measuring instruments?
- How do you adjust the feed and speed of the machine tool?
- What methods do you use to ensure the accuracy of machined parts?
- How do you maintain the machine tools in order to ensure optimal performance?
- How do you set up and operate CNC machine tools?
- What do you think are the most important considerations when operating a machine tool?
- What computer software programs have you used to program CNC machine tools?
Common Tools in Industry
- Drill Press. A machine tool for drilling holes, typically in metal, with a sharp cutting tool. (e. g. Hole Drilling)
- Lathe. A machine tool used for turning, cutting, and drilling materials. (e. g. Precision Turning)
- Milling Machine. A machine tool used for cutting and shaping metal and other materials. (e. g. Surface Milling)
- Grinder. A machine tool that uses an abrasive wheel to sharpen or shape metal pieces. (e. g. Cylindrical Grinding)
- Boring Machine. A machine tool used to bore holes in metal or other materials. (e. g. Spot Facing)
- Saw. A machine tool used for cutting materials such as wood, metal, and plastic. (e. g. Cross-Cutting)
- Shaper. A machine tool used for shaping and forming metal pieces into various shapes and sizes. (e. g. Keyway Cutting)
- Planer. A machine tool used for shaping flat surfaces on metal pieces. (e. g. Surface Planing)
Professional Organizations to Know
- Association for Manufacturing Technology (AMT)
- National Institute for Metalworking Skills (NIMS)
- International Machine Tool Show (IMTS)
- International Association of Machinists and Aerospace Workers (IAMAW)
- Society of Manufacturing Engineers (SME)
- Tooling and Manufacturing Association (TMA)
- National Tooling and Machining Association (NTMA)
- American Machine Tool Distributors' Association (AMTDA)
- The American Society of Tool and Manufacturing Engineers (ASME)
- National Tooling and Machining Association (NTMA)
We also have Machine Shop Supervisor Trainee, Machine Learning Engineer, and Machine Repair Technician jobs reports.
Common Important Terms
- CNC (Computer Numerical Control). A type of machine tool which uses computer-programmed commands to control its cutting movements.
- CAD (Computer Aided Design). A type of software which is used to generate 3D models and designs for use in the manufacturing process.
- CAM (Computer Aided Manufacturing). A type of software which is used to generate instructions for a machine tool to perform a certain task.
- G-Code. A type of programming language which is used to control CNC machines.
- Lathe. A type of machine tool which is used to shape materials into rotational symmetrical shapes.
- Milling. A type of machine tool which is used to shape materials by cutting away material from a workpiece.
- Drilling. A type of machine tool which is used to create holes in materials.
- Grinding. A type of machine tool which is used to remove material from a workpiece by abrasion.
Frequently Asked Questions
What is a Machine Tool Operator?
A Machine Tool Operator is a skilled professional who operates various types of machining tools and equipment to fabricate, modify, or repair metal, plastic, and other materials.
What skills are needed to be a Machine Tool Operator?
To be a successful Machine Tool Operator, you must have an aptitude for mathematics, mechanical aptitude and manual dexterity. You must also be able to interpret technical drawings and instructions and have the ability to operate a variety of tools and machines.
What type of equipment do Machine Tool Operators use?
Machine Tool Operators use a variety of tools and machines, including lathes, milling machines, drill presses, power saws, grinding machines, computer numerical control (CNC) machines, and other specialized equipment.
What are the working conditions for Machine Tool Operators?
Machine Tool Operators typically work in factories or machine shops where they may be exposed to hazardous machinery and chemicals. They may also be required to stand for long periods of time and lift and move heavy objects.
What is the job outlook for Machine Tool Operators?
The job outlook for Machine Tool Operators is positive. According to the U.S. Bureau of Labor Statistics, the median annual wage for Machine Tool Operators is $37,890 and employment is expected to grow 5 percent from 2019 to 2029.
What are jobs related with Machine Tool Operator?
- Machine Tool Design Engineer
- Machine Shop Manager
- Machine Tool Setter
- Machine Assembly Technician
- Machine Assembly Supervisor
- Machine Operator Trainee
Web Resources
- Machine Tool Operator - Technical Diploma | CVTC www.cvtc.edu
- Machine Tool Operation Technical Diploma | Madison ¦ madisoncollege.edu
- Machine Tool Operations | MATC www.matc.edu
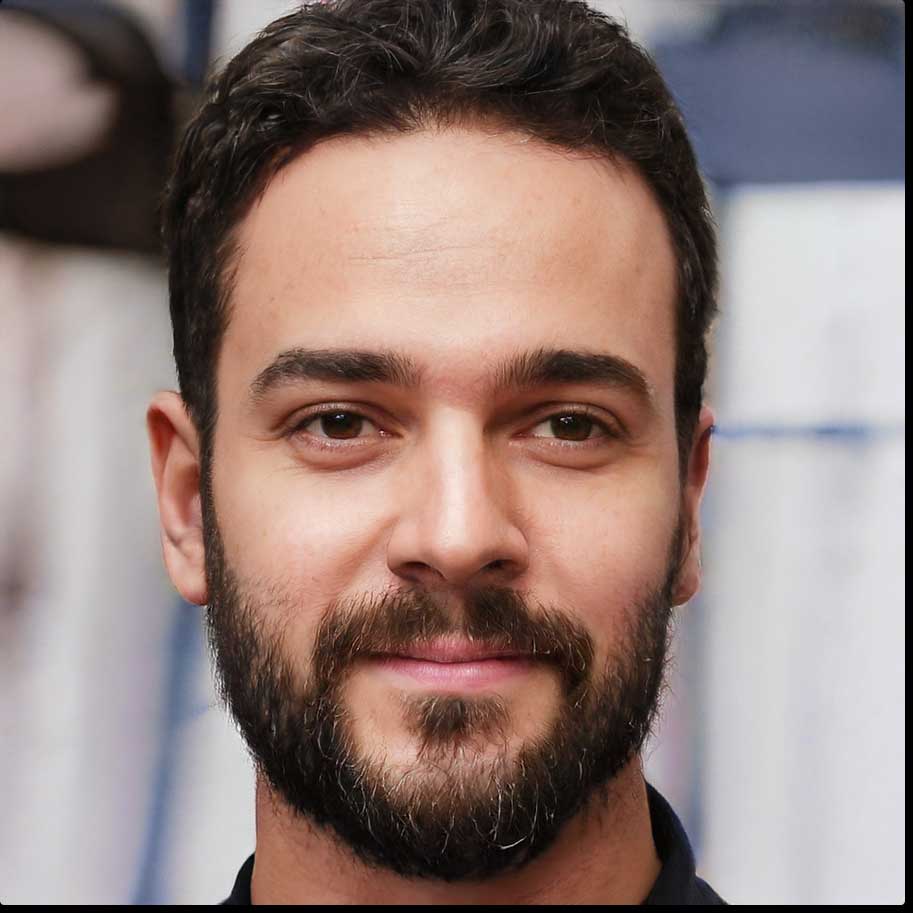