How to Be Industrial Electrician - Job Description, Skills, and Interview Questions
Industrial electricians play a vital role in keeping businesses running. They are responsible for installing, maintaining, and repairing electrical wiring and components in industrial settings. Their work ensures that equipment and machinery are functioning properly, safely, and efficiently.
Without the expertise of industrial electricians, businesses would not be able to operate as efficiently, resulting in potential loss of profits and customer satisfaction. their work helps to reduce the risk of fires and injuries caused by faulty wiring and electrical systems. As such, industrial electricians are integral to the success of businesses, as they are essential for preventing costly damages and promoting a safe working environment.
Steps How to Become
- Earn a High School Diploma or GED. Industrial electricians need to have a high school diploma or GED to be considered for positions.
- Attend a Vocational School or College. Many industrial electricians attend a vocational school or college to learn the specific skills they need to be successful in the field.
- Obtain an Apprenticeship. Most industrial electricians start their careers as apprentices in order to gain hands-on experience. Apprenticeships usually last for four to five years and involve on-the-job training as well as classroom instruction.
- Become Licensed. In most states, industrial electricians must be licensed to work. Licensing requirements vary from state to state, so it is important to check with the local licensing board in order to determine what is needed in order to become licensed.
- Take Continuing Education Courses. Continuing education courses are often required for industrial electricians in order to stay current on the latest technology and safety standards.
Industrial electricians play a critical role in keeping businesses and industrial facilities running smoothly and safely. It is important for them to stay up to date with modern technology and best practices, and to maintain their qualifications, in order to ensure that their work is of the highest quality. To do this, electricians can access educational materials such as industry magazines, webinars, seminars, and conferences.
They can also take advantage of online courses and certifications offered by trade organizations to stay ahead of emerging trends and techniques. attending workshops and networking with other electricians can help them stay informed of the latest developments in the field. Keeping up to date and qualified helps industrial electricians to provide the best service possible to their employers and customers.
You may want to check Licensed Electrician, Maintenance Electrician, and Plant Electrician for alternative.
Job Description
- Troubleshoot and repair electrical systems and components.
- Inspect and test electrical systems and components.
- Diagnose and repair malfunctioning systems, apparatus, and components using test equipment and hand tools.
- Install, maintain, and repair electrical wiring, fixtures, control systems, and related equipment.
- Plan layout of wiring and equipment.
- Read and interpret drawings and diagrams to determine work procedures.
- Follow National Electrical Code (NEC) standards and state and local building regulations.
- Connect wires to circuit breakers, transformers, and other components.
- Provide technical advice on electrical maintenance and repairs.
- Monitor system performance and make necessary adjustments.
Skills and Competencies to Have
- Knowledge of electrical theory and principles
- Ability to work with various electrical systems, components, and wiring
- Knowledge of safety regulations and best practices
- Ability to read and interpret electrical schematics and blueprints
- Proficiency in the use of hand and power tools
- Excellent troubleshooting and problem-solving skills
- Ability to work independently and as part of a team
- Ability to lift and move heavy equipment
- Attention to detail and good organizational skills
- Knowledge of National Electrical Code (NEC)
Industrial electricians play a crucial role in maintaining the safety and efficiency of industrial operations. Having the right skills and knowledge is essential for an industrial electrician to carry out their job safely and effectively. One of the most important skills for an industrial electrician is the ability to read and comprehend technical diagrams, as this provides them with the necessary information to interpret circuit diagrams and safety information.
they need to be able to troubleshoot and diagnose electrical problems, as well as understand the principles of electrical theory and circuit design. Furthermore, industrial electricians must also possess a working knowledge of electrical components and their functions, so they can properly install, repair and maintain equipment. Finally, they must have strong communication skills in order to work efficiently with other team members, and ensure that electrical systems are functioning properly.
Without these important skills, industrial electricians would not be able to effectively perform their job and keep industrial operations safe and efficient.
Foreman Electrician, Commercial Electrician, and Residential Electrician are related jobs you may like.
Frequent Interview Questions
- What experience do you have as an industrial electrician?
- How do you troubleshoot electrical problems?
- How do you read and interpret wiring diagrams and schematics?
- What safety protocols do you follow when working with electrical systems?
- Describe a project you completed as an industrial electrician.
- What challenges have you encountered when working with industrial electrical systems?
- How do you ensure that each component of a system is working properly?
- What methods do you use to ensure a job is done correctly and efficiently?
- How do you stay up-to-date on advancements in industrial electrical engineering?
- Describe your experience working with a team of electricians on a large-scale project.
Common Tools in Industry
- Multimeter. An electronic measuring device used to measure voltage, current, and resistance. (eg: Fluke 87V)
- Wire Strippers. A tool used to strip the insulation from electrical wires. (eg: Klein 11045)
- Cutters/Pliers. A tool used to cut and shape wires. (eg: Irwin Vise-Grip)
- Screwdrivers. A tool used to drive screws into various materials. (eg: Stanley Screwdriver Set)
- Arc Welders. A welding machine used to join two pieces of metal together using an electrical arc. (eg: Miller Maxstar 200)
- Clamp Meter. An electronic device used to measure current without breaking the circuit. (eg: Fluke 376FC)
- Insulated Gloves. Protective gloves made with insulated material to protect against electric shock. (eg: Ergodyne ProFlex 901P)
- Voltage Tester. A device used to check the voltage of electrical outlets and wiring. (eg: Klein NCVT-1)
- Crimpers. A tool used to connect two pieces of metal or wire together. (eg: Knipex 7-Piece Crimping Pliers Set)
- Welding Helmet. A helmet with a face shield that protects the eyes, face, and neck from sparks and other debris during welding. (eg: Lincoln Electric Viking 3350)
Professional Organizations to Know
- National Electrical Contractors Association (NECA)
- International Brotherhood of Electrical Workers (IBEW)
- International Association of Electrical Inspectors (IAEI)
- Institute of Electrical and Electronics Engineers (IEEE)
- National Fire Protection Association (NFPA)
- American Society of Safety Engineers (ASSE)
- American Society of Heating, Refrigerating, and Air-Conditioning Engineers (ASHRAE)
- American Society for Testing and Materials (ASTM)
- National Electrical Manufacturers Association (NEMA)
- National Electrical Safety Code (NESC)
We also have Power Plant Electrician, Aircraft Electrician, and Marine Electrician jobs reports.
Common Important Terms
- Electromechanics. The study of the operation of electrical and mechanical components in a system.
- Wiring Diagrams. Detailed drawings that illustrate how electrical components are connected together.
- Electrical Troubleshooting. The process of diagnosing and resolving problems with electrical systems or components.
- Circuit Breakers. Devices that can open or close an electrical circuit to protect it from damage due to overload or short circuit.
- Transformers. Electrical machines that use electromagnetic induction to change the voltage level of an alternating current.
- Motor Control. The use of motor controllers to regulate the speed and direction of a motor.
- Relays. Devices used to control an electrical circuit by energizing and de-energizing parts of the circuit.
- Programmable Logic Controllers (PLCs). Computers that are programmed to control and monitor complex industrial processes.
- Testing and Troubleshooting. The process of testing electrical systems for safety and reliability, as well as identifying and resolving problems.
Frequently Asked Questions
What is an Industrial Electrician?
An Industrial Electrician is a skilled tradesperson who specializes in the installation, maintenance and repair of electrical systems in industrial and commercial settings.
What qualifications do Industrial Electricians need?
Industrial Electricians usually need to have completed a relevant apprenticeship program and possess a relevant certification or license. They may also need to have experience working with high-voltage and hazardous equipment.
What type of work do Industrial Electricians do?
Industrial Electricians typically install, repair and maintain complex electrical systems and components in industrial and commercial settings. They may also be responsible for troubleshooting electrical problems, diagnosing system malfunctions and performing routine maintenance.
What safety protocols should Industrial Electricians follow?
Industrial Electricians must strictly adhere to safety procedures when working with high-voltage and hazardous equipment, including wearing the proper protective gear, following local codes and regulations, and properly disposing of hazardous materials.
What tools do Industrial Electricians use?
Industrial Electricians typically use a variety of specialized tools and equipment, such as power drills, multimeters, voltmeters, wire cutters, soldering irons and screwdrivers. They may also use personal protective equipment such as safety glasses, ear protection and hard hats.
What are jobs related with Industrial Electrician?
Web Resources
- Industrial Electrician - Northeast Iowa Community College www.nicc.edu
- Industrial Electrician | Western Technical College www.westerntc.edu
- Industrial Electrician Career Profile: Job Description, Duties and ... www.rsi.edu
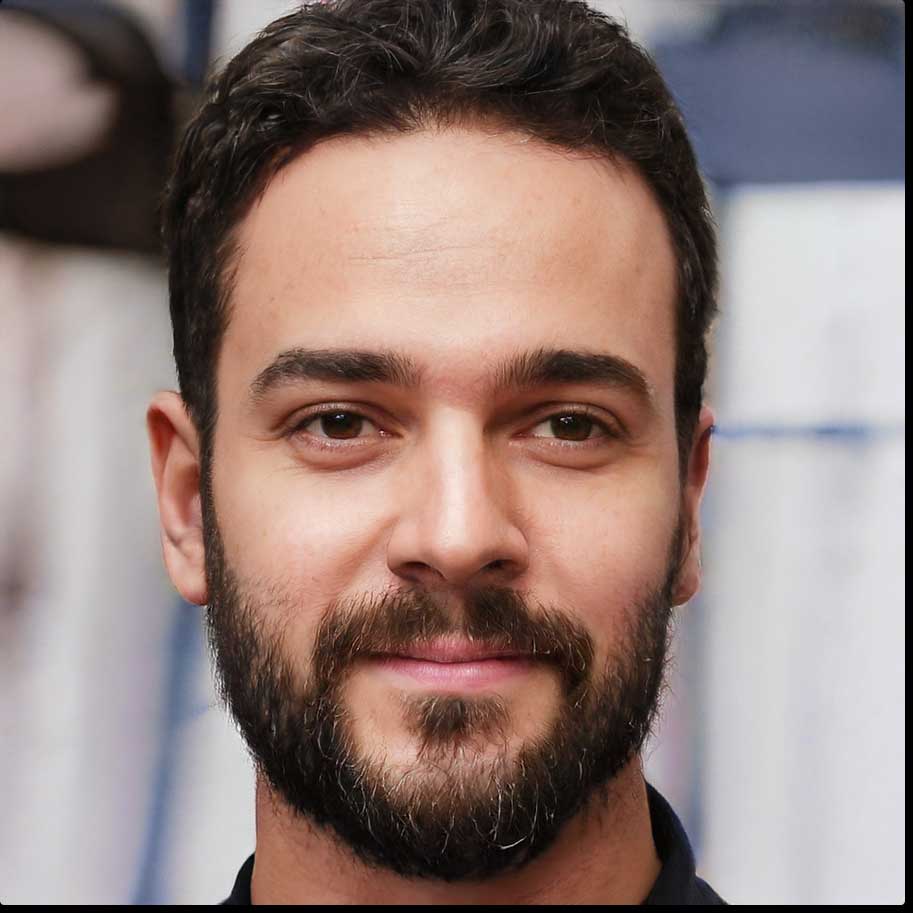