How to Be Driller Operator - Job Description, Skills, and Interview Questions
Driller operators are essential for the successful execution of many industrial operations. They are responsible for creating holes in the ground for a variety of reasons, such as drilling for oil and gas, installing pipes, and creating foundations. As a result, driller operators must have a strong knowledge of drilling techniques, equipment, and safety protocols.
They must also be able to adjust the equipment in response to changing terrain and rock conditions. Furthermore, driller operators must be able to interpret data and make decisions quickly in order to protect personnel and equipment. If the driller operator fails to perform their duties correctly, it can lead to costly delays or even serious accidents.
Consequently, driller operators must have a thorough understanding of their role and the tools at their disposal in order to carry out their work efficiently and safely.
Steps How to Become
- Obtain a high school diploma or GED. Driller operators typically need at least a high school diploma or GED.
- Gain experience in the oil and gas industry. You'll need to have experience in the oil and gas industry before you can become a driller operator. This can include working as a rig hand, roustabout, or other oilfield service professional.
- Get certified. Depending on the state you are working in, you may need to get a certification to work as a driller operator. Check with your state's oil and gas regulatory agency for more information.
- Obtain a commercial driver's license (CDL). A CDL is necessary for operating large trucks and other vehicles used in the oil and gas industry.
- Take safety courses. Most employers require that their driller operators have taken safety courses, such as OSHA 10-hour or 30-hour courses.
- Join professional organizations. Joining professional organizations, such as the International Association of Drilling Contractors, can help you network and stay up to date on the latest technologies and trends in the industry.
You may want to check Tower Crane Operator, Backhoe Operator, and Process Control Room Operator for alternative.
Job Description
- Operate a drill rig or other drilling equipment to drill holes for oil, gas, or other materials.
- Monitor the drilling process to ensure that drilling is carried out in accordance with established procedures and safety regulations.
- Monitor and adjust the drilling speed and pressure as needed to maintain the desired depth and diameter of the drilled hole.
- Inspect and maintain drilling equipment to ensure safe and efficient operation.
- Set up and assemble drilling equipment, such as pumps, tanks, hoses, and valves, in accordance with safety regulations.
- Direct crew members in loading, unloading, and positioning of drilling rigs and related equipment.
- Analyze drill samples to monitor progress and make adjustments as necessary.
- Troubleshoot mechanical problems with drilling equipment and make repairs as needed.
- Monitor and record data on the depth and diameter of each drilled hole.
- Adhere to all applicable safety protocols and procedures.
Skills and Competencies to Have
- Mechanical aptitude
- Ability to operate hand and power tools
- Knowledge of safety protocols
- Ability to read and interpret technical drawings
- Knowledge of drilling techniques
- Physical strength and stamina
- Ability to lift heavy objects
- Ability to work in confined spaces
- Good communication skills
- Attention to detail
- Ability to work well in a team environment
- Good problem solving skills
Drilling is a complex and demanding job that requires a great deal of skill and expertise. The most important skill for a driller operator is the ability to safely and accurately control the drill and its equipment. This requires a high level of experience and knowledge of the drilling process, as well as the ability to problem solve and make quick decisions.
A driller operator must also be able to understand and interpret data, including seismic surveys and well logs, in order to identify the best drilling locations and techniques. In addition, the operator must be able to work with a range of different tools and machinery, from heavy machinery to precision tools, in order to carry out various tasks. Finally, the driller operator must be able to work with other members of a drilling crew, from the engineers to the rig crew, in order to ensure a safe and efficient operation.
Being a successful driller operator requires a combination of technical knowledge and practical experience, which will all contribute to a successful drilling operation.
Heavy Equipment Mechanic /Operator, Pipe Layer Operator, and Concrete Pump Operator are related jobs you may like.
Frequent Interview Questions
- What experience do you have as a Driller Operator?
- What safety protocols do you follow when operating a drill?
- How do you ensure the drill is functioning correctly?
- What do you do to make sure the drilling process runs smoothly?
- How do you handle unexpected issues that arise while drilling?
- What strategies do you use to maximize drilling efficiency?
- How do you troubleshoot and address mechanical issues with the drill?
- What measures do you take to ensure the accuracy of the drilling process?
- How do you handle difficult terrain or challenging conditions while drilling?
- What is your experience working with a team to carry out complex drilling projects?
Common Tools in Industry
- Drill Rig. A heavy-duty machine used to bore deep into the earth to extract mineral deposits (eg: Oil rig).
- Drilling Machine. A machine used to cut cylindrical holes in a material (eg: Metalworking drill press).
- Jackhammer. A tool used to break up hard surfaces like asphalt and concrete (eg: Pneumatic jackhammer).
- Boring Machine. A machine used to enlarge existing holes in a material (eg: Horizontal boring machine).
- Core Drill. A drill designed to cut into a material in order to obtain a cylindrical core sample (eg: Diamond core drill).
- Auger. A tool used to bore into the ground to create holes for planting trees or posts (eg: Post hole auger).
Professional Organizations to Know
- International Association of Drilling Contractors (IADC)
- American Petroleum Institute (API)
- National Driller Association (NDA)
- International Union of Operating Engineers (IUOE)
- International Society of Explosives Engineers (ISEE)
- Association of Energy Service Companies (AESC)
- Society of Petroleum Engineers (SPE)
- National Ground Water Association (NGWA)
- American Society of Mechanical Engineers (ASME)
- American Society of Safety Professionals (ASSP)
We also have Production Line Operators, Bulldozer Operator, and Production Control Room Operator jobs reports.
Common Important Terms
- Drilling Rig. The main structure used to drill into the earth for oil and gas extraction.
- Drilling Fluids. A mixture of chemicals, water and air used to lubricate and cool the drill bit, flush cuttings from the well and protect the borehole from collapsing.
- Downhole Tools. Equipment used to manipulate the wellbore such as stabilizers, reamers, drill bits and logging probes.
- Directional Drilling. Process of drilling a hole in a curved or angled direction, typically with the use of a downhole motor and mud motor.
- Mud Logging. Process of recording data related to the drilling process such as depth, rate of penetration, lithology etc.
- Blowout Prevention (BOP). Equipment and systems installed on a drilling rig to prevent uncontrolled releases of oil or gas during drilling.
Frequently Asked Questions
What type of machinery is operated by a Driller Operator?
A Driller Operator operates a variety of drilling equipment, such as diamond core drills, rotary drills, and percussion drills.
What is the primary task of a Driller Operator?
The primary task of a Driller Operator is to bore holes in the earth for the purpose of exploration, resource extraction, and other industrial needs.
What qualifications are required to become a Driller Operator?
To become a Driller Operator, individuals typically need to have a high school diploma or equivalent, as well as experience or training in operating drilling equipment.
What safety measures must be taken when operating drilling equipment?
When operating drilling equipment, safety measures must be taken to protect the operator and other personnel from potential hazards. This includes wearing appropriate personal protective equipment (PPE), following safety protocols, and having emergency shut-off procedures in place.
How deep can a Driller Operator bore into the earth?
The depth that a Driller Operator can bore into the earth depends on the type of drilling equipment being used, but typically ranges from several hundred feet to several thousand feet.
What are jobs related with Driller Operator?
- Gas Compressor Operator
- Loader Operator
- Robotics Operators
- Truck Operator
- Asphalt Paver Operator
- Wheel Loader Operator
- Machine Operator
- Drilling Operator
- Dredge Operator
- Sewerage Treatment Plant Operators
Web Resources
- Educational Webinar Series | The Driller www.thedriller.com
- Directional Drilling & Hydro Excavation Operator Training www.nwtc.edu
- 8.2: Drilling Contracts | PNG 301: Introduction to www.e-education.psu.edu
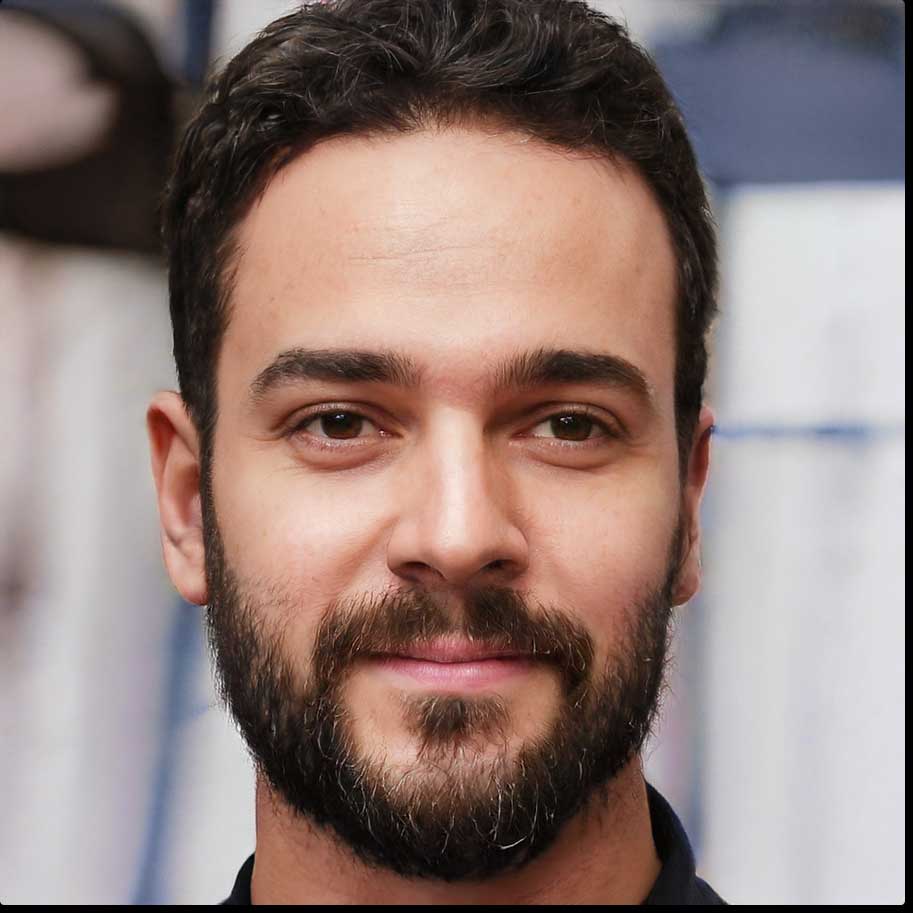