How to Be Director of Logistics - Job Description, Skills, and Interview Questions
The success of the logistics industry is dependent on efficient directors of logistics who can ensure that goods are delivered in a timely and cost effective manner. An effective director of logistics will be able to successfully manage the complex network of shipping, storage, and delivery systems, as well as coordinate personnel, equipment and resources. By doing so, they will be able to maximize the efficiency of the entire system by minimizing costs and streamlining processes.
if the director of logistics is able to effectively manage inventory levels and transportation routes, they can reduce lead times and improve customer satisfaction. the success of the logistics industry depends on directors of logistics who are able to effectively manage all aspects of the supply chain.
Steps How to Become
- Obtain a bachelors degree. A degree in logistics, supply chain management, business administration, or a related field is typically needed to become a director of logistics.
- Gain experience. Most companies require directors of logistics to have experience in the field, such as working as a logistics coordinator or manager.
- Get certified. A Certified Professional Logistician (CPL) certification from the Association for Supply Chain Management (ASCM) is highly recommended for directors of logistics.
- Demonstrate leadership skills. Directors of logistics must possess strong leadership, organizational, and communication skills, so its important to demonstrate these qualities while working in logistics.
- Become familiar with relevant technology. Directors of logistics need to understand the various software and systems used in the industry to keep track of shipments, manage inventory, and streamline processes.
- Apply for director of logistics jobs. After gaining the necessary qualifications and experience, you can start applying for director of logistics jobs.
The logistics industry is a rapidly evolving and increasingly competitive sector, and staying ahead requires staying up-to-date and qualified in the field. The most successful logistics directors understand the importance of proactively keeping up with the latest trends and technologies in the industry. This involves regularly attending conferences, workshops, and webinars, and actively pursuing continuing education opportunities.
Continuous learning is also essential, and staying abreast of changes in industry regulations, standards, and best practices is critical. By developing an in-depth knowledge base, it is possible to develop effective strategies and utilize new technologies to optimize processes and enhance customer service. it is important to stay connected with colleagues in the field in order to share ideas and network with potential partners or clients.
Finally, it is important to have experience and expertise in a certain specialization, such as transportation, warehousing, supply chain management, or inventory control. With the right qualifications and dedication to staying informed and connected, logistics directors can remain ahead of the curve and remain competitive in the field.
You may want to check Financial Director, Director of Operations, and Strategic Planning Director for alternative.
Job Description
- Develop, implement and monitor logistics strategies, processes and systems.
- Coordinate the activities of staff and third-party providers to ensure that the organization meets its logistics objectives.
- Design, develop and maintain logistical relationships with vendors, suppliers, and customers.
- Establish and monitor key performance indicators and metrics in order to ensure the effective delivery of services.
- Analyze logistics data and develop reports on a regular basis.
- Negotiate contracts and pricing with vendors and suppliers.
- Monitor and review the accuracy of shipping and receiving documents.
- Establish effective communication systems with all stakeholders to ensure the timely delivery of goods and services.
- Manage and develop the logistics team to ensure they are providing exceptional customer service.
- Develop procedures and policies to ensure the most efficient use of resources.
- Keep up to date with changes in the logistics sector and suggest ways to improve efficiency.
- Oversee the development, implementation and maintenance of quality assurance processes and procedures.
Skills and Competencies to Have
- Knowledge of international customs regulations and procedures
- Knowledge of supply chain processes and best practices
- Ability to develop and implement cost-effective logistics strategies
- Excellent problem-solving and analytical skills
- Strong organizational and time-management skills
- Ability to work effectively in a team environment
- Excellent communication and negotiation skills
- Proficiency in Microsoft Office Suite, including Excel
- Ability to manage multiple tasks simultaneously
- Knowledge of transportation regulations, laws and compliance standards
Effective communication is the most important skill to have when it comes to directing logistics. Having the ability to effectively communicate with other departments, vendors, and customers is essential for a successful logistics operation. Being able to effectively communicate instructions, expectations, and outcomes can help ensure that deadlines are met, resources are properly allocated, and deliveries are made on time.
Communication also helps maintain strong relationships with customers, vendors, and other departments by allowing everyone to be on the same page and understand the expectations of each other. Furthermore, effective communication can help reduce confusion and conflicts between departments or customers. In order to be successful in directing logistics, the Director of Logistics must be able to effectively communicate their ideas, expectations, and outcomes.
Regulatory Affairs Director, Production Director, and Technical Director are related jobs you may like.
Frequent Interview Questions
- What experience do you have in logistics?
- How do you handle the pressure of managing multiple projects simultaneously?
- What strategies do you employ to motivate your team?
- Describe a time when you successfully implemented a new process or procedure to improve efficiency.
- How do you ensure that all deliveries are made on time and in accordance with customer specifications?
- What steps do you take to ensure accuracy and quality control in your logistics operations?
- Describe your approach to working with vendors and suppliers.
- How do you stay up to date on best practices in the industry?
- In what ways have you used technology to streamline logistics processes?
- What challenges have you faced while managing logistics operations, and how did you overcome them?
Common Tools in Industry
- Warehouse Management System (WMS). A comprehensive system that automates and optimizes the storage, movement, and tracking of goods within a warehouse. (Eg: Manhattan Warehouse Management System)
- Transportation Management System (TMS). A system that helps companies plan, execute, and manage freight shipments. (Eg: Transwide TMS)
- Supply Chain Management (SCM) Software. Software that optimizes the flow of information and materials between suppliers, manufacturers, distributors, and customers. (Eg: Oracle SCM Cloud)
- Logistics Execution System (LES). A software platform that manages the entire order fulfillment process from order entry to delivery. (Eg: SAP LES)
- Route Optimization Software. Software that uses algorithms to determine the most efficient route for a delivery. (Eg: OptimoRoute)
- Inventory Control Software. Software that tracks stock levels and helps manage inventory levels. (Eg: Fishbowl Inventory)
- Freight Brokerage Software. Software that helps manage and streamline the process of negotiating contracts and services with freight carriers. (Eg: MercuryGate TMS)
- Warehouse Labor Management System (WLMS). A software system designed to automate and optimize warehouse staff productivity. (Eg: HighJump WMS)
Professional Organizations to Know
- Council of Supply Chain Management Professionals (CSCMP)
- Institute for Supply Management (ISM)
- American Production and Inventory Control Society (APICS)
- International Warehouse Logistics Association (IWLA)
- Association of Transportation Management Professionals (ATMP)
- International Air Cargo Association (IACA)
- International Association of Refrigerated Warehouses (IARW)
- National Customs Brokers & Forwarders Association of America (NCBFAA)
- Transportation Intermediaries Association (TIA)
- National Shippers Strategic Transportation Council (NASSTRAC)
We also have Director of Marketing, Quality Assurance Director, and Creative Director jobs reports.
Common Important Terms
- Warehousing. The process of storing goods in a warehouse, which is typically a large, secure facility that is used to store raw materials, finished products, and other items for later use.
- Inventory Management. The process of tracking and managing the inventory of goods, including tracking stock levels, ordering new items, and managing the supply chain.
- Supply Chain Management. The management of the interconnected flow of goods from the point of origin to the point of consumption, including sourcing of raw materials, production, logistics, and distribution.
- Logistics. The management of the movement of goods from one location to another, including the planning and coordination of transportation, warehousing, and delivery.
- Route Optimization. The process of optimizing the delivery routes of goods to maximize efficiency and minimize costs.
- Route Planning. The process of planning the most efficient route for delivery vehicles or other transportation vehicles.
- Fleet Management. The management of a companys fleet vehicles, including maintenance, repairs, and scheduling.
Frequently Asked Questions
What is the role of the Director of Logistics?
The Director of Logistics is responsible for overseeing the planning, implementation, and monitoring of all logistical operations within an organization. This includes managing supply chains, inventory control, transportation, and warehousing.
What qualifications are needed to be a Director of Logistics?
To become a Director of Logistics, candidates should possess a minimum of a bachelor's degree in business, logistics, or a related field. Additionally, experience in supply chain management or a related field and knowledge of applicable laws and regulations are also highly valued.
What are some key responsibilities of a Director of Logistics?
A Director of Logistics is responsible for overseeing the planning and implementation of the organization's logistical operations. This includes managing inventory control, transportation, supply chain management, and warehousing. Additionally, they are responsible for maintaining accurate records and ensuring compliance with regulations and safety standards.
How much does a Director of Logistics typically earn?
The average salary for a Director of Logistics is approximately $84,000 per year. However, salaries can vary widely depending on location, experience level, and other factors.
What industry sectors commonly employ Directors of Logistics?
Directors of Logistics are employed across many industries, including retail, manufacturing, transportation, and healthcare. Additionally, they may be employed by government agencies, non-profit organizations, and logistics companies.
What are jobs related with Director of Logistics?
- Project Director
- Director of Sales
- Director of Human Resources
- Research and Development Director
- Communications Director
Web Resources
- What is a logistics director? - UAB Online Degrees businessdegrees.uab.edu
- Shelena Johnson, Director of Logistics Northwestern Black ... sites.northwestern.edu
- Guide to Becoming a Chief Logistics Officer - University of supplychainmanagement.utk.edu
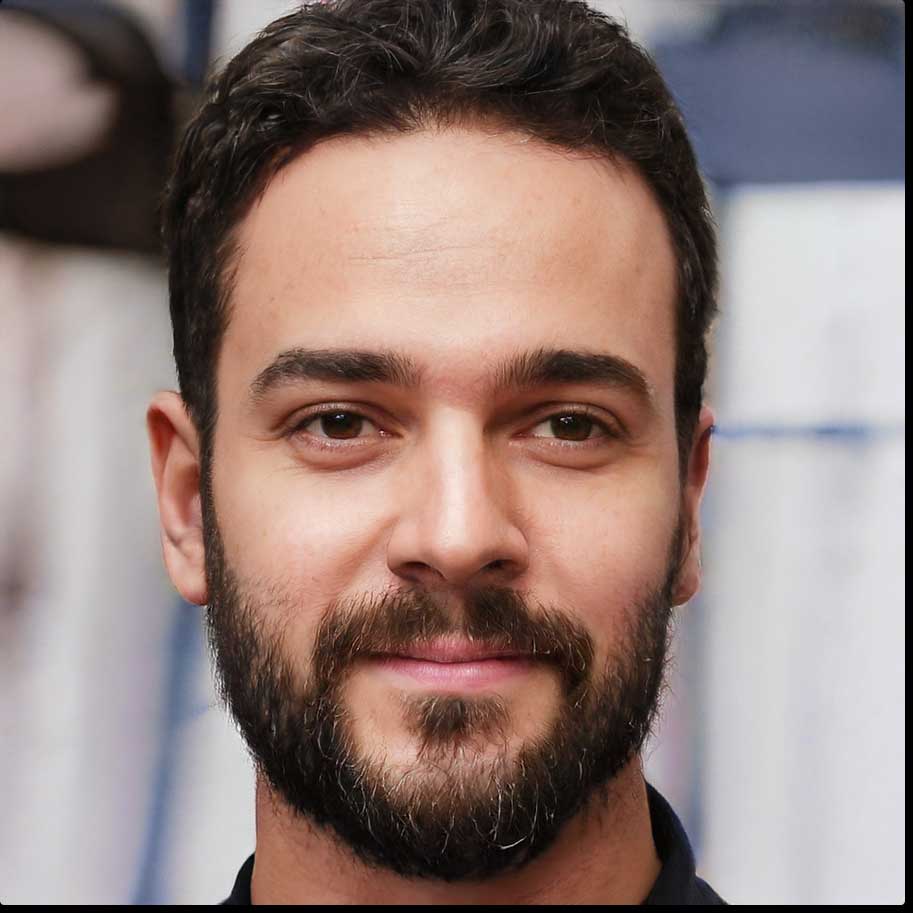