How to Be Chemical Plant Operators - Job Description, Skills, and Interview Questions
Chemical plant operators play an essential role in the production process of a variety of industries. They are responsible for controlling and monitoring the various pieces of equipment that are used to mix, process and produce chemicals. As a result of their diligent work, they ensure that the chemical plant functions in a safe and efficient manner.
The operators must operate the equipment properly and be aware of any potential risks involved in the production process. In addition, they must also have the necessary knowledge to interpret complex data and make adjustments when necessary. Without the expertise of these chemical plant operators, companies would not be able to produce the products they need in a timely and cost-effective manner.
Therefore, chemical plant operators are essential for the success of any company that deals with hazardous chemicals.
Steps How to Become
- Obtain a high school diploma or equivalent. Most employers prefer to hire chemical plant operators who have at least a high school diploma or equivalent.
- Obtain on-the-job training. Many employers prefer to hire chemical plant operators who have prior experience in the field or who have obtained on-the-job training.
- Pursue formal training. Many employers prefer to hire chemical plant operators who have completed formal training programs in chemical engineering, industrial technology, or a related field.
- Obtain certification. Most states require chemical plant operators to obtain certification from the National Institute for Chemical Plant Operators (NICPO).
- Consider obtaining additional certifications. Depending on the type of chemical plant, certain operators may be required to obtain additional certifications such as hazardous materials handling certification, confined spaces certification, and more.
- Apply for a job. Once the necessary qualifications are met, individuals can begin applying for jobs as chemical plant operators.
The job of a Chemical Plant Operator requires significant training and experience to be successful. Those interested in becoming Chemical Plant Operators must have a thorough understanding of the chemical processes involved, as well as the safety protocols necessary to protect workers and the environment. In order to become a proficient Chemical Plant Operator, individuals must complete a specialized program or apprenticeship, gaining hands-on experience and knowledge in plant operations and safety.
they must possess strong technical abilities, problem-solving skills, and be able to work independently as well as with a team. By possessing these skills, Chemical Plant Operators are able to successfully operate the equipment and systems of the plant, ensuring the safety and efficiency of the operation.
You may want to check Blast Hole Drill Operator, Forklift Operator, and Asphalt Paver Operator for alternative.
Job Description
- Monitor and operate chemical plant equipment to control chemical processes.
- Adjust and control chemical process variables such as temperature, pressure, and flow rate.
- Monitor plant systems to ensure efficient operation and process consistency.
- Start up, shut down, and troubleshoot equipment when needed.
- Follow plant safety protocols and wear appropriate safety equipment.
- Monitor and replenish chemicals used in the process.
- Perform routine maintenance on equipment.
- Complete necessary paperwork and documentation.
- Analyze process data and adjust operations to maintain process consistency and meet production goals.
- Ensure compliance with environmental regulations and safety standards.
Skills and Competencies to Have
- Knowledge of safety regulations
- Ability to operate, maintain, and troubleshoot plant machinery
- Knowledge of relevant laws and regulations
- Ability to read and interpret technical schematics and diagrams
- Familiarity with production processes and equipment
- Ability to multi-task and prioritize tasks
- Ability to work in a team environment
- Good problem-solving and analytical skills
- Good written and verbal communication skills
- Ability to stay organized and adhere to deadlines
Chemical Plant Operators are essential for the production of chemicals and materials in industrial plants. The most important skill for a Chemical Plant Operator is an understanding of the chemical process, safety protocols, and the ability to troubleshoot and problem-solve. A Chemical Plant Operator must have a good grasp of mathematics, chemistry, engineering, and computer systems to be able to monitor and analyze the process.
They must also be able to detect any abnormalities within the system. they must be able to interpret the results of tests and experiments in order to identify any potential problems that could arise. Having the ability to think critically and use problem-solving skills is key in this role.
Without these skills, a Chemical Plant Operator could put the entire process at risk, leading to costly mistakes and potential disasters.
Tower Crane Operator, Truck Operator, and Gas Compressor Operator are related jobs you may like.
Frequent Interview Questions
- What experience do you have working in a chemical plant?
- What safety protocols do you follow when working with hazardous chemicals?
- How do you track and monitor the performance of the equipment at a chemical plant?
- Describe a time when you had to troubleshoot a technical issue in a chemical plant.
- How do you ensure that all processes and procedures are followed according to specifications?
- What challenges have you faced in the past related to efficient operation of a chemical plant?
- How do you stay current on industry trends and best practices?
- How do you handle complex problem-solving scenarios within the chemical plant?
- What steps would you take to improve operational efficiency at a chemical plant?
- How do you ensure compliance with environmental regulations related to chemical plants?
Common Tools in Industry
- Process Control System. A system that monitors, records, and regulates the production process within a chemical plant. (e. g. DeltaV by Emerson Automation Solutions)
- Process Flow Diagram (PFD). A diagram showing the flow of raw materials and chemicals used in a particular industrial process. (e. g. PFD for an ethylene plant)
- Chemical Analysis Software. Software used to analyze the chemical composition of a given sample. (e. g. Thermo Scientific Chromeleon Chromatography Software)
- High-Pressure Vessels. Containers designed to store and handle high-pressure gases or liquids. (e. g. carbon steel and stainless steel pressure vessels)
- Safety Equipment. Protective gear used to protect chemical plant operators from hazardous materials and conditions. (e. g. safety glasses, gloves, and respirators)
- Data Acquisition Systems. Systems used to collect data from various instruments and sensors in a chemical plant. (e. g. Campbell Scientifics CR1000 Data Logger)
- Computers. Computers are used to store, analyze, and control the various processes in a chemical plant. (e. g. Dell OptiPlex desktop computers)
- Instrumentation. Devices used to measure and monitor various parameters in a chemical plant such as temperature, pressure, and flow. (e. g. Emerson Rosemount Pressure Transmitter)
- Automation Software. Software used to automate processes and reduce manual labor in a chemical plant. (e. g. Siemens Simatic Automation Software)
- Industrial Valves. Used to control the flow of fluids in a chemical plant. (e. g. butterfly valves, gate valves, and ball valves)
Professional Organizations to Know
- Society of Chemical Industry (SCI)
- American Institute of Chemical Engineers (AIChE)
- National Association of Chemical Distributors (NACD)
- International Society of Automation (ISA)
- Association of Chemical Industry of Texas (ACIT)
- American Society of Safety Engineers (ASSE)
- National Fire Protection Association (NFPA)
- American Society of Mechanical Engineers (ASME)
- Institute of Industrial and Systems Engineers (IISE)
- National Association of Corrosion Engineers (NACE)
We also have Process Control Room Operator, CNC Machine Operator, and Excavator/Dozer/Grader/Scraper/Loader/Hoe Operators jobs reports.
Common Important Terms
- Process Control Systems. Process control systems use a combination of automated and manual techniques to measure and control process variables such as temperature, pressure, flow rate, and chemical composition.
- Distillation. Distillation is a process of separating mixtures based on differences in their boiling points.
- Reaction Kinetics. Reaction kinetics is the study of the rate at which chemical reactions occur and the factors that affect it.
- Hazardous Materials Management (HMM). HMM is the practice of safely handling, storing, and disposing of hazardous materials, such as chemicals and gas tanks.
- Instrumentation. Instrumentation is the use of measuring and controlling devices to monitor, control, and optimize chemical plants.
- Process Simulation. Process simulation is the use of computer models to simulate the behavior of complex chemical processes.
- Process Safety Management (PSM). PSM is an organized approach to managing the risks associated with the use of hazardous materials.
- Quality Assurance (QA). QA is a systematic approach to ensuring that products meet certain standards and requirements for safety, quality, and reliability.
Frequently Asked Questions
What type of education is required to be a Chemical Plant Operator?
To become a Chemical Plant Operator, a high school diploma or equivalent is typically required. However, some employers may prefer candidates with an associate degree in a related field, such as process technology or chemical technology.
What are the primary duties of a Chemical Plant Operator?
The primary duties of a Chemical Plant Operator include monitoring and controlling the production process, setting up and adjusting equipment, testing the quality of products and materials, troubleshooting malfunctions, and performing routine maintenance on equipment.
What types of safety procedures must be followed by a Chemical Plant Operator?
Chemical Plant Operators must follow strict safety procedures to minimize risks associated with hazardous materials and processes. This includes following safety protocols for handling hazardous materials, wearing protective gear, operating equipment safely and correctly, and following safety policies and procedures set by the employer.
What physical abilities are needed to be a Chemical Plant Operator?
Chemical Plant Operators must have good physical strength and dexterity. They must be able to lift and move items weighing up to 50 pounds, stand for long periods of time, and work in cramped positions. Good hand-eye coordination is also essential.
What type of work environment can a Chemical Plant Operator expect?
Chemical Plant Operators typically work in industrial settings and may be exposed to loud noises, hazardous materials, extreme temperatures, and other potential safety hazards. They must be able to work independently and use problem-solving skills to troubleshoot any issues that arise.
What are jobs related with Chemical Plant Operators?
- Offshore Pumping Platform Operator
- Combination Welder Operators
- Lift Truck Operator
- Bulldozer Operator
- Dredge Operator
- Powerhouse Technician/Operator
- Heavy Equipment Mechanic /Operator
- Loader Operator
- Elevator Operator
- Pipe Layer Operator
Web Resources
- Example Career: Chemical Plant and System Operators www.wvu.edu
- Chemical Operator - Job Training cfcc.edu
- Chemical Process Operator | Delaware Technical Community www.dtcc.edu
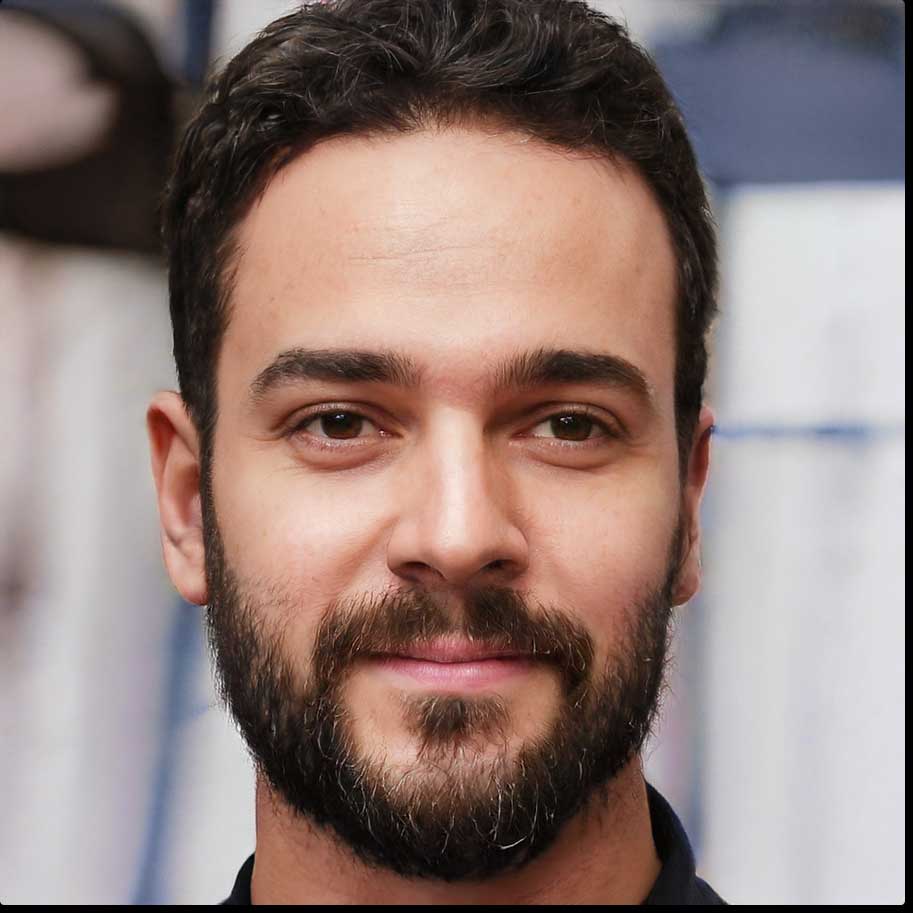