How to Be Boilermaker Supervisor - Job Description, Skills, and Interview Questions
Steps How to Become
- Obtain a High School Diploma or Equivalent. Boilermaker supervisors typically need to have at least a high school diploma or its equivalent.
- Complete an Apprenticeship. Most employers require boilermaker supervisors to have at least a few years of experience in boilermaking as a journeyman. This experience can be gained through apprenticeships in which participants learn through a combination of classroom instruction and on-the-job training.
- Earn Certification. Certification may be required or preferred by some employers. The American Boiler Manufacturers Association, for example, offers the Certified Boilermaker Supervisor (CBMS) designation. To become certified, applicants must have at least four years of experience, pass an exam, and pay a fee.
- Consider Additional Training. Depending on their job duties, supervisors may need additional training in areas such as safety and hazardous materials management.
- Seek Employment. Boilermaker supervisors can find job openings through online job boards and by contacting local boilermaking companies directly.
Boilermaker Supervisors must stay ahead and efficient in order to ensure the successful completion of their projects. One of the most important steps is to create a plan and timeline for the project that is clear and concise. This plan should include all steps involved in the project, including the necessary materials and estimated timeframes.
it is important to stay organized and keep accurate records of progress, so that any potential problems can be identified quickly. Furthermore, regular communication with the team is essential; this ensures everyone understands the project goals and deadlines, and that any issues or concerns can be addressed in a timely manner. Finally, staying ahead of schedule by planning ahead and anticipating potential problems will help to ensure the boilermaker supervisor can complete their projects efficiently and on time.
You may want to check Boilermaker Technician, Boilermaker Maintenance Worker, and Boilermaker Maintenance Technician for alternative.
Job Description
- Supervise and coordinate the day-to-day activities of Boilermakers and other personnel on job sites to ensure efficient and effective execution of project objectives.
- Develop welding procedures, fit up drawings, and other technical documentation as needed.
- Inspect and evaluate the quality of Boilermaker workmanship and equipment installation on job sites.
- Monitor Boilermaker personnel to ensure compliance with safety regulations.
- Maintain records of work progress, time worked, and materials used.
- Provide training and guidance to Boilermaker personnel in order to ensure quality workmanship.
- Recommend changes or modifications to existing procedures as needed.
- Liaise with clients and other stakeholders as needed.
- Ensure that all tools and equipment used by Boilermaker personnel are in good working order.
- Manage the scheduling of personnel and materials for job sites.
Skills and Competencies to Have
- Knowledge of safety regulations related to boiler operations
- Ability to read and interpret blueprints and schematics
- Familiarity with welding and soldering techniques
- Skilled in troubleshooting and preventive maintenance
- Ability to work independently and as part of a team
- Ability to prioritize tasks and manage multiple projects
- Understanding of boiler system operations, including fuel, air, water, and steam
- Knowledge of applicable regulations, codes, and standards
- Strong communication and interpersonal skills
- Ability to lead and motivate a team
- Proficient in Microsoft Office Suite
- Excellent organizational and problem-solving skills
- Ability to work in high-pressure situations
Boilermaker supervisors must possess a wide range of skills in order to effectively manage and oversee the day-to-day operations of a boilermaker team. The most important skill for a boilermaker supervisor to have is strong leadership. Leaders must be able to motivate team members, create a positive work environment, and establish clear expectations while respecting the diverse needs of each team member.
In addition to strong leadership, a boilermaker supervisor must also have excellent communication and interpersonal skills, as well as problem-solving abilities. This allows for clear communication between team members and management, effective conflict resolution, and the ability to create efficient solutions to any issues that may arise. Finally, a boilermaker supervisor must possess a thorough understanding of applicable safety regulations and guidelines, as well as the knowledge and experience to properly supervise a team of boilermakers.
With these skills in place, a boilermaker supervisor can ensure operations are running smoothly and efficiently while keeping safety as the top priority.
Boilermaker Laborer, Boilermaker Fitter, and Boilermaker Helper are related jobs you may like.
Frequent Interview Questions
- What experience do you have in supervising boilermaker teams?
- How would you ensure that safety protocols are adhered to in the work area?
- Describe your approach to delegating tasks and setting goals for team members.
- What have been some of the most challenging projects you have supervised?
- How would you develop and maintain good relationships with clients?
- What strategies do you use when dealing with difficult team members?
- How do you stay up to date on current boilermaker technologies and methods?
- How would you handle a situation where a project was not meeting its completion deadlines?
- What methods do you use to ensure that all work is completed according to quality standards?
- How do you motivate team members to perform their best?
Common Tools in Industry
- Hard Hat. Protective headgear for workers in hazardous environments (eg: construction sites).
- Respirator. Breathing device to protect against hazardous airborne particles (eg: dust, smoke, and fumes).
- Safety Glasses. Protective eyewear to guard against flying debris and hazardous materials (eg: wood chips and metal shavings).
- Work Boots. Reinforced footwear to protect feet from sharp objects and heavy loads (eg: steel-toe boots).
- Hand Tools. Small tools used to complete tasks, such as wrenches, pliers, screwdrivers, hammers, and saws.
- Power Tools. Electric or pneumatic tools used to complete tasks faster than hand tools (eg: drills, sanders, routers).
- PPE. Personal protective equipment to safeguard against workplace hazards (eg: gloves, ear plugs, face shields).
- Welding Equipment. Machines, tools, and supplies used to join two pieces of metal together (eg: welding helmet, rods, and flux).
- Lifting Equipment. Tools and machines used to lift, move, and transport heavy objects (eg: forklifts, cranes, hoists).
- Fire Extinguisher. Portable device to extinguish fires (eg: CO2 or dry chemical fire extinguishers).
Professional Organizations to Know
- American Society of Mechanical Engineers (ASME)
- National Board of Boiler and Pressure Vessel Inspectors (NBBI)
- American Boiler Manufacturers Association (ABMA)
- National Association of Power Engineers (NAPE)
- Association of Water Technologies (AWT)
- International Association of Boiler and Pressure Vessel Inspectors (IABPV)
- National Fire Protection Association (NFPA)
- American Society for Quality (ASQ)
- National Institute for Boiler and Pressure Vessel Inspectors (NIBPVI)
- Canadian Boiler Society (CBS)
We also have Boilermaker Foreman, Boilermaker Welder, and Boilermaker Inspector jobs reports.
Common Important Terms
- Boiler Systems. Boiler systems are a system of components that work together to produce hot water or steam for industrial, commercial, and residential purposes.
- Boiler Safety. Boiler safety is a set of standards and regulations designed to prevent injury or death due to improper operation of a boiler.
- Boiler Maintenance. Boiler maintenance is the practice of regularly checking and servicing boilers in order to ensure that they are operating safely and efficiently.
- Boiler Upgrades. Boiler upgrades are modifications to an existing boiler system that improve energy efficiency, fuel savings, and overall performance.
- Boiler Operation and Troubleshooting. Boiler operation and troubleshooting are processes that involve inspecting, testing, and repairing boilers to ensure their safe and efficient operation.
- National Fire Protection Association (NFPA). The NFPA is a nonprofit organization dedicated to promoting fire safety and protecting people from fire-related hazards. It sets standards for fire protection, including boiler safety regulations.
Frequently Asked Questions
What qualifications do I need to become a Boilermaker Supervisor?
To become a Boilermaker Supervisor, you typically need to have a high school diploma or GED equivalent, along with 5+ years of experience in boilermaker installation and repair. Additionally, some employers may require certifications in welding and other related trades.
What is the job description of a Boilermaker Supervisor?
A Boilermaker Supervisor is responsible for overseeing the installation, maintenance, and repairs of boilers, pressure vessels, and related equipment. They manage and train boilermaker staff, develop and implement safety policies and procedures, coordinate with other trades and contractors, and ensure that all operations are in compliance with OSHA and other regulations.
What are the primary duties of a Boilermaker Supervisor?
The primary duties of a Boilermaker Supervisor include overseeing the installation, maintenance, and repair of boilers and related equipment; managing and training boilermaker staff; developing and implementing safety policies and procedures; coordinating with other trades and contractors; and ensuring that all operations are in compliance with OSHA and other regulations.
How much does a Boilermaker Supervisor make?
According to the U.S. Bureau of Labor Statistics, Boilermaker Supervisors earn an average annual salary of $69,590. Salaries can vary depending on experience, location, and industry.
What is the job outlook for Boilermaker Supervisors?
The job outlook for Boilermaker Supervisors is projected to grow 5% from 2019 to 2029. This growth is due to an increase in demand for power-generating plants, refineries, and other industrial facilities that require boilers.
What are jobs related with Boilermaker Supervisor?
- Boilermaker Pipefitter
- Boilermaker Rigger
- Boilermaker Refractory Technician
- Boilermaker Machinist
- Boilermaker Fabricator
- Boilermaker Apprentice
- Boilermaker Structural Assembler
- Boilermaker Journeyman
- Boilermaker Assistant
Web Resources
- - PURDUE UNIVERSITY | BoilerLink boilerlink.purdue.edu
- Being a Boilermaker - Purdue University honors.purdue.edu
- Boilermaker Educator - Fall 2022 - Purdue University College of www.education.purdue.edu
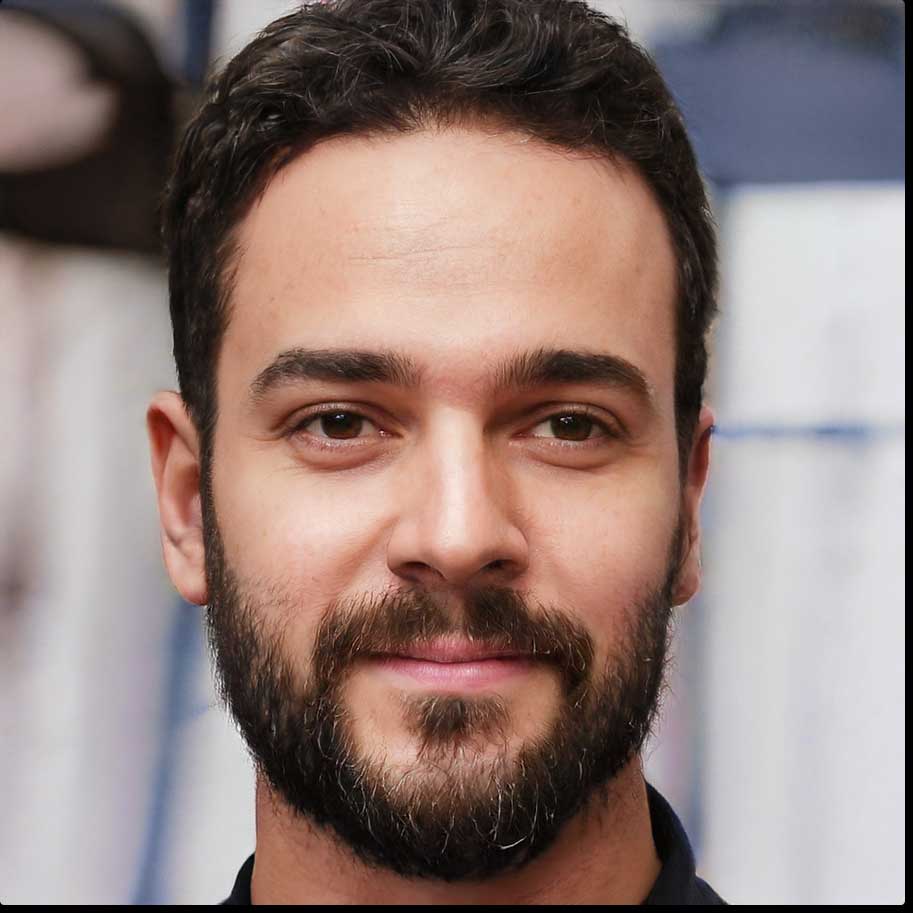